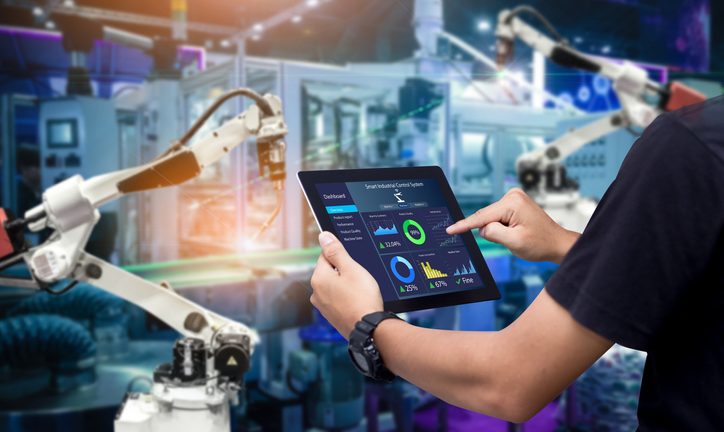
As we can see that smart factories are now becoming the future of manufacturing that offering a new level of efficiency and productivity to those spending in them.
Industry 4.0, integrated with increasingly advanced analytics, is playing a key role in driving the smart factory movement.
Innovative technologies likewise big data, IoT, artificial intelligence (AI) and the cloud assure that those who handle and maintain manufacturing environments can gain on the front foot and dynamically manage these environments, with comparatively low levels of investment.
The capability of this new span of responsive machinery is costly, allowing a higher level of communication, exposure and, hence, yield between all stakeholders. Business owners can forecast and handle the failures of their machinery and, with this suppliers can reduce their maintenance costs.
The development of predictive maintenance
For many years, condition monitoring, as well as predictive maintenance, have been a norm for the few and a dream for the majority. The cost, as well as the complexity of collecting and monitoring sufficient data to drive substantial results, has restricted predictive maintenance to the defense and aerospace sectors.
Hence, the evolution of Industry 4.0, where production assets are attached to the internet and capable to interact, integrated with AI and advanced analytics, has revealed the concept of predictive maintenance to a much broader range of industries as well as use cases.
The term of a smart factory is completely dependent on the connectivity enabled by Industry 4.0. Machines that can sense and interact can offer a huge amount of valuable data. Hence, this data requires to be filtered and monitored if it is to be translated into pragmatic insight for manufacturers.
Much like the collecting of machine data, actually, this analysis would have been a highly manual attempt, including teams of expensive data scientists. Signified algorithms are essential because the condition data outputs from machines — even two of the same make and model — are as isolated as a human fingerprint. AI does the heavy lifting here, fine-tuning the performance of each algorithm to improve its accuracy.
Industry 4.0 is an essential part of this process. Automation is only feasible because of the data that is collected from the machines, but it also needs computing power to monitor that data. This crucial analysis is executed elsewhere on the internet, in the cloud, where the resources present to power the AI and run the algorithms constantly, in any case of where the machines are placed.
The advantages of minimizing downtime
Current developments in condition monitoring and predictive maintenance, made easy, in part, via Industry 4.0, are remarkably improving the performance of industrial machinery, while making the job of operating and maintaining it simpler and more efficient.
Unplanned downtime is a big drawback for any manufacturing environment. In the automotive sector, for instance, each minute that crucial machinery is offline will charge the factory tens of thousands of pounds.
Collecting data and connecting with services in the cloud are already deriving remarkable improvements in machine effectiveness and efficiency. The longer-term capability of these technologies has yet to be noticed, but it is clear that it will be precisely transformative.