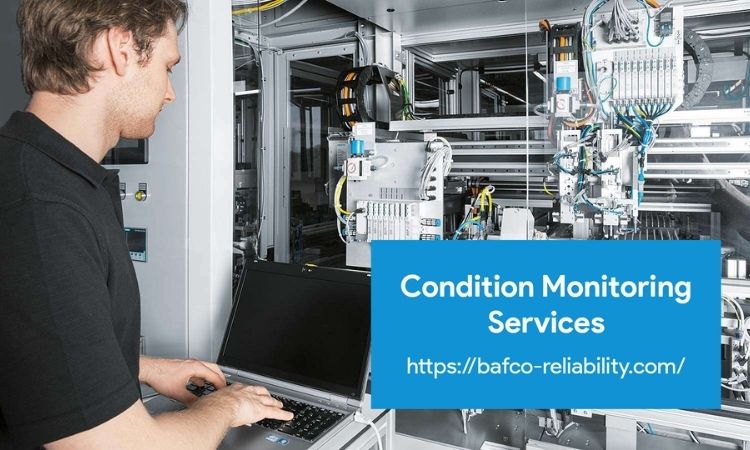
Proper condition monitoring and effective predictive maintenance (PdM) strategies can help you extend the life of your equipment and avoid costly downtime and repairs.
To help you implement condition monitoring and effective predictive maintenance (PdM) strategies, here are some best practices that can help you optimize your condition monitoring process.
- Extend the life of equipment through condition monitoring services. Hone in on what is really happening with your equipment, generate reports for your team based on condition indicators, identify trends, and make improvements based on the data.
- Tune into condition monitoring performance to enhance your business results. It sounds simple, but if you are tuning in to what is happening with your equipment that can impact its long-term health—and not just reading an automated email report—then you're getting full value from your condition monitoring solution.
- Optimize your equipment performance through effective maintenance. Condition monitoring can provide data to support PdM efforts, but only if the data is gathered correctly and acted upon in a timely manner. If you are not already using condition monitoring for this purpose, then start doing it now! Take advantage of the full value that condition-based maintenance (CBM) offers, including increased uptime, better fuel economy, and reduced emissions.
- Ensure your condition monitoring reports are accurate and actionable for optimal results. Are you generating the right data? And are you making quality decisions based on that data? These two questions can make or break your condition monitoring program. If you are not getting the data you need, or if it is not actionable, then you are wasting your time and money.
- Optimize condition monitoring costs with ease-of-use solutions. Be sure to consider an easy-to-use solution that will minimize operator training time and ensure all team members contribute reports, regardless of their expertise level.
- Keep your condition monitoring team happy by providing the right tools. A successful condition monitoring program depends on all members of the team working well together, so it's important to support your operators with tools that can help them be more effective at their jobs.
- Implement a laser alignment service to extend equipment life and save money in the long run. Any laser alignment services will include verification of laser accuracy after laser alignment, laser maintenance, and laser inspection services.
Condition monitoring is beneficial for increasing equipment life and avoiding costly repairs. Laser alignment services are also helpful in these regards as well as minimizing energy loss due to misalignment. Following the tips above can help you implement a successful condition monitoring program.
How to Make Your Equipment Last Longer:
Condition monitoring services can help you extend the life of your equipment. Determine how well condition monitoring works for your organization by paying attention to its performance. Ensure that your equipment performs at peak efficiency through regular maintenance and get accurate reports with a simple solution. Support operators by providing tools for success and implementing a laser alignment service in addition to condition monitoring to increase the longevity of your equipment.
Here are a few ways to maintain your vibration monitoring equipment:
- Test vibration monitors for accuracy at least once per year. If vibration monitor accuracy is found below, then calibrate or replace the vibration monitor as necessary.
- Maintain vibration monitoring equipment- Ensure all screws are tightened, worn parts are replaced, lubrication is applied where needed and other routine maintenance tasks are completed.
- Use vibration data to improve equipment performance- Proper vibration data interpretation will enable a company to identify trends, condition indicators and make improvements based on the vibration monitoring data collected.
- Tune into vibration monitoring performance- It sounds simple, but if you are tuning in to what is happening with your vibration monitoring equipment that can help you avoid vibration-related failures.
- Take vibration monitoring data to the next level with vibration analytics. Vibration analytics will provide insight into vibration patterns in your equipment, which can improve uptime and reduce maintenance costs by identifying potential problems before they arise, leading to proactive PdM efforts.
- Use vibration data to optimize performance. It is important to use vibration monitoring as a tool, not as the end-all solution to vibration problems. If vibration data points to an issue, but other factors such as lubrication and coolant levels indicate otherwise, take those factors into consideration as well before making any decisions about how best to address vibration issues with equipment.
Bafco Reliability provides vibration monitoring machines and vibration monitoring services. We can provide vibration monitoring solutions for customers who need vibration monitoring equipment, vibration monitors, vibration monitoring systems, or vibration testing.
Contact us today to learn about our vibration monitoring options. We will be happy to discuss how we can help you with your vibration monitoring needs.