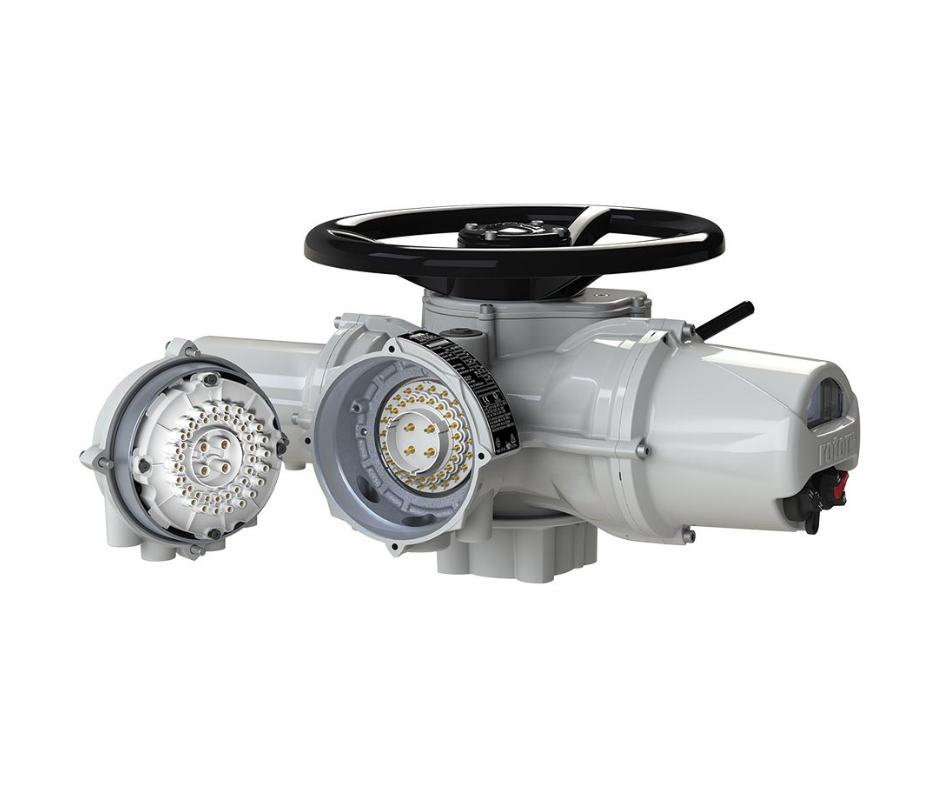
An Electric Valve Actuator is a type of mechanical device that opens and closes a valve. Its main features include High torque from a standstill, Overtorque protection, Fieldbus communication feedback, and Limit switches. It is also useful for reducing energy costs. The features and benefits of an Electric Valve Actuator should be discussed in detail when selecting an actuator for your application.
High Torque from a Standstill
When designing a hydraulic valve system, the Electric Valve Actuator must be able to deliver high torques from a standstill. This is necessary for high-pressure and large-diameter valves. A high torque valve actuator should be stable and mechanically efficient. It should also have a low voltage so that it will not exceed the preset load.
A torque switch prevents overload by sensing high torques in the valve. If it detects an overload situation, it shuts down the actuator and stops the process. Any situation that trips this switch is likely to disrupt the process and damage the equipment.
Over Torque Protection
Electric valve actuators can be vulnerable to over-torque. Using an over-torque protector is a cost-effective way to prevent damage to valves. It eliminates the costly downtime and traffic disruption caused by damaged valves. These valve protection devices work with both manual and electric actuators and protect valves in either direction of rotation. They are available with a variety of options for different torque capacities and operating temperatures.
Over-torque protection for electric valve actuators is critical for a safe valve control system. If it is not used properly, it can lead to serious equipment damage. The protection device should be able to detect the over-torque condition and automatically shut off power when the valve is closed or opened. The safety device should also have mechanical limit stops to protect the motor from over-travel.
Fieldbus Communication Feedback
Electric valve actuators can receive feedback via digital signals that are transmitted over the Fieldbus communication protocol. These signals are sent by a digital electronic circuit and are used to adjust the valve's position. The new Fieldbus technology enables two-way communication, which allows for more flexibility when implementing control strategies. With FieldBus technology, control architectures can be improved and plant availability improved. This technology also reduces wiring costs.
In addition to the 4-20mA signal that indicates valve position, actuators can also send discrete feedback signals. These signals may include a torque feedback signal or a general fault signal. They can be programmed to send feedback based on specific requirements.
The life cycle of Valve Actuator
One of the most important things to consider when buying an electric valve actuator is the life cycle of the device. This is important because an electric valve actuator produces heat when it operates. This heat can be harmful, causing damage to the electric valve actuator. Fortunately, there are ways to minimize the impact of heat on the life cycle of an electric valve actuator.
The first phase of an electric valve actuator's life cycle is the operation phase. This is the longest part of the cycle. During this time, the safety instrumented functions must remain operational to maintain SILs. Traditionally, plant turnarounds were scheduled every two or three years, but with the rise in system reliability, plant turnarounds are now scheduled more frequently, reducing SILs.