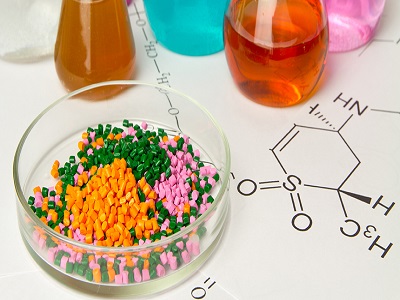
A Primer on Chemical Recycling
Mechanical techniques have been used to recycle plastics so far. An overview of the non-mechanical recycling technologies currently being developed in the emerging "chemical recycling" industry is specified below.
Plastics that are difficult or expensive to recycle mechanically can now be recycled, thanks to a variety of developing technologies in the waste management sector.
Chemical recycling methods can significantly increase recycling rates and prevent plastic waste from being disposed of in landfills or burned repeatedly by converting it back into basic chemicals and chemical feedstocks.
By allowing for the continued extraction of value from polymers that have reached the limits of their economic viability for mechanical processing, chemical recycling technologies accompany mechanical recycling processes. Previously difficult-to-recycle plastic items including films, multi-layered plastics, and laminated plastics can now be recycled chemically as an alternative to landfilling and burning. Chemical recycling also provides the supply chain for plastics with virgin-quality raw ingredients. This makes it possible to create food-grade polymers from post-consumer trash.
Mass Balance Approach
Inputs, outputs, and related information are transferred, tracked, and regulated as they pass through each stage of the relevant supply chain using the chain of custody concept known as mass balance.
To assess specific product features and guarantee the validity and transparency of related product claims, a chain-of-custody model must be chosen, with the following two options:
Renewable origin, recycled materials, etc.
Mass balance is a model where materials or goods having a set of specified qualities are mixed with materials or products without that set of characteristics by established criteria.
Chemical Recycling of Plastics
Chemical recycling refers to a variety of procedures and methods. Based on where the technologies' output is located in the supply chain for plastics, they can be divided into three different categories:
- Purification: By submerging the polymers in solvents, dissolution eliminates additives from the polymers. Plastic disintegrates, taking it back to the polymer stage. Afterward, the polymers can be reformed to create freshly recycled plastics.
- Depolymerization breaks down polymers into simpler molecules (monomers) using chemistry, solvents, and heat. These monomers are then used as secondary raw materials in the manufacture of plastic.
- Feedstock Recycling: To convert plastic waste into a gaseous (gasification) or liquid, oil-like feedstock (pyrolysis), such as refined hydrocarbons or petrochemicals, which are then further processed to form the feedstock for petrochemical-type processing, the conversion also uses chemistry, heat, or catalytic processes in a reactor.
The Advantages of Chemical Recycling, Especially Pyrolysis
Recycles plastic trash; which has traditionally been difficult to recycle, has a similar quality to virgin feedstock in terms of the plastics it produces, reduces reliance on fossil fuels, and minimizes CO2 emissions.
From Discarded Plastic to Items Of The Highest Quality
The usage of plastics has been shown to provide advantages, such as preventing food loss in packaging applications, making automobiles lighter, and insulating buildings. However, the problem of plastic trash has spread throughout the world. Approximately 250 million metric tonnes of plastic garbage are produced annually throughout the world. The fact that only about 20 percent of this plastic is recycled keeps the substance in use. Consequently, more plastic garbage should be recycled as a whole. Innovation and collaborative efforts across the value chain are necessary to address this issue and create a more circular economy for plastics. By creating cutting-edge goods and technology that encourage plastic recycling, BASF will help with this.
The ChemCycling Project of BASF
The ChemCycling project is primarily concerned with plastic trash that cannot be mechanically recycled due to technological, financial, or environmental constraints. Examples include plastics with residues, mixed plastic waste fractions, which include various plastic types and won't be further sorted, and used tires that won't be recycled in any other way. The combined use of mechanical and chemical recycling can boost total recycling rates and advance the circular economy of plastics.
Zest of The ChemCyclingTM project
Complementary: Plastic waste streams that cannot be recycled mechanically due to technological, financial, or environmental constraints can be processed by chemical recycling. For instance, whereas sorted single-stream plastic waste should be recycled mechanically, mixed post-consumer plastic waste streams, such as PE, PP, and PS, can be recycled chemically because additional sorting is not cost-effective.
Dedicated to finding solutions: The recycling landscape now includes chemical recycling, which is significant. It is not always possible to redesign plastic objects so that they are mechanically recyclable, for instance, doing so would reduce performance or increase material usage.
Outputs of virgin quality: Through chemical recycling, plastic waste streams can be transformed back into feedstock for the chemical industry and distributed to goods produced in BASF's integrated chemical production network (Verbund) using a mass balance method. These goods are made from the same materials used to make fossil fuels, and they have the same characteristics.
Utilization simplicity: Our customers can use these items in applications requiring a high standard of performance, quality, and hygiene in the same manner as products made conventionally. Examples of this might be vehicle parts that are important for safety or medical uses or food packaging. This assists in meeting higher recycled content goals for goods that have to adhere to the highest quality requirements.
Transparent certification: Independent auditors certify both the mass balance process, which determines the amount of recycled feedstock to be allotted to the product and the goods themselves.
By employing recycled feedstock, we can conserve fossil resources and reduce emissions. Additionally, mass balance-based products created from chemically recycled feedstock emit fewer greenhouse gases than conventional products made from primary fossil resources. This is so that new chemical products can be made using the waste plastic instead of incinerating it.
Commercial Models
The chemical recycling industry is seeing several startups at varying phases of development. To showcase the technique, several pilot plants are running throughout Europe, while others are growing to an industrial scale.
Commercial facilities will come in a variety of sizes, including big, centralized plants with annual throughput capacities of 30 to 200 kt, small, modular distributed units with capacities of 3 to 10 kt, and mobile units with yearly capacities of up to 3 t.
Companies that operate larger, more centrally located plants frequently provide recycling as a service. In this case, the factory would take care of receiving the waste while keeping ownership of the finished product for later sale to the chemical industry.
Operators of waste handling facilities are frequently offered the option to purchase the recycling technology solution by businesses with a dispersed, smaller facility. The facility in question will be developed remotely and delivered to be installed into already-existing garbage and material handling facilities. The waste handler will maintain ownership of the output product for subsequent sales to the chemical industry, while the technology supplier will profit from equipment sales and maintenance contracts.
Firms Involved in The Chemical Recycling Sector
Aduro Clean Technologies, Agilyx, Alterra, Amsty, Arcus, Axens, Basf Chemcycling, BiologiQ, BlueAlp, Borealis, BP, Braskem, Carbios, Clariter, Chevron Phillips, Covestro, Cyclyx, DSM, Dupont Teijin Films, Eastman, Emerson, Emmi, Enval, Evonik, Exergy Solutions, ExxonMobil, Forell Pomini, Greenback, GreenMantra, GR3N, Greiner Packaging, Honeywell, Ineos Styrosolution, Interseroh, Ioniqa (NL), Licella, Lummus, Lyondellbasell, Milliken, Mitsubishi Chemical, Neste, New Hope Energy, Nexus, Nova Chemicals, Obbotec, Omv, Orlen Unipetrol, Phigenesis, Plastic Energy, PureCycle Technologies, Pyrocell, Quantafuel, Recenso, Renewcell, Renew ELP, Sabic, Scholle IPN, Sekisui Chemical, Shell, SK Global Chemical, Soprema, Sudpack, Sumitomo Chemical, Swedish Plastic Recycling, Switch Energy, Technip Energies, Total Energies Corbion, Versalis, and Vita Group amongst other.
Contemporary Developments and Collaboration
- A Memorandum of Understanding was signed today by Shell and REMONDIS Recycling GmbH, a part of the Rethmann Group (MoU). As a result, the two businesses decide to work together long-term and strategically, with the initial goal of creating a closed loop for raw materials in the Shell Energy and Chemicals Park Rheinland, south of Cologne. The objective is to satisfy the future demands for more environmentally friendly chemical and energy products.
- Bp and Clean Planet Energy, a UK-based business building facility to transform difficult-to-recycle waste plastics into circular petrochemical feedstocks and ultra-low-sulfur diesel, have inked a 10-year offtake agreement (ULSD). The ecoPlants that Clean Planet Energy designs and constructs are intended to process plastics that are generally turned away by conventional recycling facilities and would otherwise be disposed of or burned.
- Wenew, a new worldwide Circular Economy ecosystem from Braskem, is released. The idea of Wenew symbolizes and unifies Braskem's efforts on this front. The company will move closer to a more circular future by investing in cooperatively creating an increasingly circular and sustainable world with the production chain and society. It incorporates four pillars: products, education, technology, and circular design. The development of such products, their growing availability, and the need to further leverage the concept of the circular economy across the chemical and plastic production chain led to Braskem's recognition of the dimension and importance that circular products have been gaining internally and externally, as well as the company's commitment to the cause. This led to the creation of Wenew. As a result, it was necessary to reconsider the current organization, and so Braskem was created.
- Eastman and Interzero come to a long-term PET waste supply arrangement. According to Eastman officials, this new molecular recycling facility will be the biggest material-to-material molecular recycling factory in the world once it is finished. The facility will recycle over 160,000 tonnes of difficult-to-recycle polyester trash annually once it is complete, including waste from colored and opaque PET that cannot be processed mechanically into clear and transparent rPET. In 2025, the project is anticipated to be operational.
A Big Market for Chemical Recycling
The need for recycled plastics is expanding along with the consumption of new polymers. Companies that manufacture consumer goods, such as Coca-Cola, PepsiCo, and Unilever, have made bold commitments to use a significant amount of recycled material in their packaging. Governments are also pushing for prohibitions on single-use plastics like straws, cotton swabs, plastic bags, and cutlery and are requiring a higher percentage of recycled materials to be used. Recycled plastics are sought after by the petrochemical industry to satisfy this quickly expanding market demand.
Mechanical recycling is unable to meet the market's demand for a significant quantity of recycled plastics, as was previously stated. Hence, chemical recycling has enormous promise. Although the industry is still in its early stages, it is currently expanding substantially, with six commercial plants now in operation and many more anticipated to be put into service over the coming few years.
Throughout the market forecast period, it is anticipated that the chemical recycling market size will expand as more and more people switch from conventional, non-renewable energy sources to clean, sustainable ones that do not contribute to global warming.
About Us
Reports and Insights is one of the leading market research company which offers syndicate and consulting research around the globe. At Reports and Insights we adhere to the client needs and regularly ponder to bring out more valuable and real outcomes for our customers. We are equipped with strategically enhanced group of researchers and analysts that redefines and stabilizes the business polarity in different categorical dimensions of the market.
Address :
Office: 1820 Avenue M,
Brooklyn, NY 11230,
United States
E-mail: [email protected]