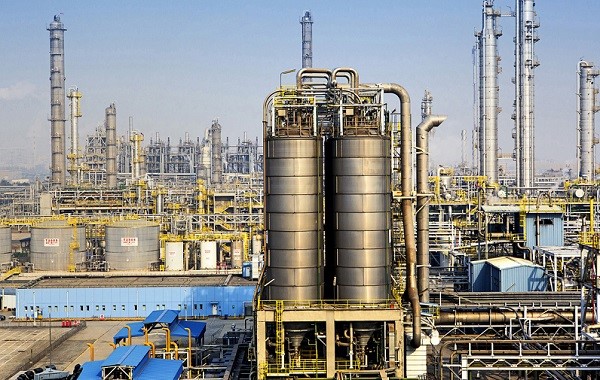
Rubber chemical intermediates are a vital part of the rubber manufacturing process compared to the finished product. These compounds are used as starting materials for producing various rubber-based products, and understanding their important role can help manufacturers make better use of them.
What are Rubber Chemical Intermediates?
Rubber chemical intermediates are chemicals that are used to produce rubber products and their derivatives. They are the building blocks for the creation of rubber items, providing strength, flexibility, durability and other properties that make them ideal for industrial use. These chemical compounds work together to give rubber its essential qualities.
How are Rubber Chemical Intermediates Used in the Manufacturing Industry?
Rubber chemical intermediates are an essential component of manufacturing industries, from the automotive and aerospace industry to electronics and medical devices. Their versatility and range of properties mean that they can be used for a variety of applications, making them invaluable to manufacturing processes. Intermediates are often used as part of rubber-based formulations that provide protection from heat, moisture and other environmental conditions. They can also provide protection against mechanical wear and tear, creating products that last longer and require less maintenance.
Advantages and Disadvantages of Using Rubber Chemical Intermediates
Rubber chemical intermediates offer a number of advantages to the manufacturing process, most notably their durability and low cost. They also require fewer resources to manufacture than other materials and can be used in a wide range of applications. However, there are some drawbacks to using such intermediates. For example, they are not as resistant to temperature and moisture as other materials, meaning they may need to be replaced more frequently or require additional protection. Additionally, the use of rubber chemicals may pose an environmental risk if not properly disposed of.
High Temperature Stability Through Advanced ETFE Coating Processes
In order to improve the temperature stability of rubber chemical intermediates, there have been a number of advanced ETFE (ethylene tetrafluoroethylene) coating processes developed. These processes involve adding coatings that are extremely thermal stable and resistant to radiation and other environmental factors. The coated material then offers excellent protection against heat, wear, and UV radiation ensuring a long-lasting product. Additionally, this process is highly efficient as it can often be applied with automated machinery allowing for mass production without relying on manual labor.
Quality Control Systems to Ensure Consistent Performance
Quality control systems are essential in the rubber chemical intermediates industry to ensure that the products created are uniform, provide consistent performance, and meet customer expectations. Processes may include automated inspections and testing procedures before, during, and after production. Additionally, manufacturing systems can also be equipped with equipment such as vision systems to capture faults or deviations from specified requirements in real-time. These quality control systems can help manufacturers maintain product quality while avoiding costly non-conforming materials.