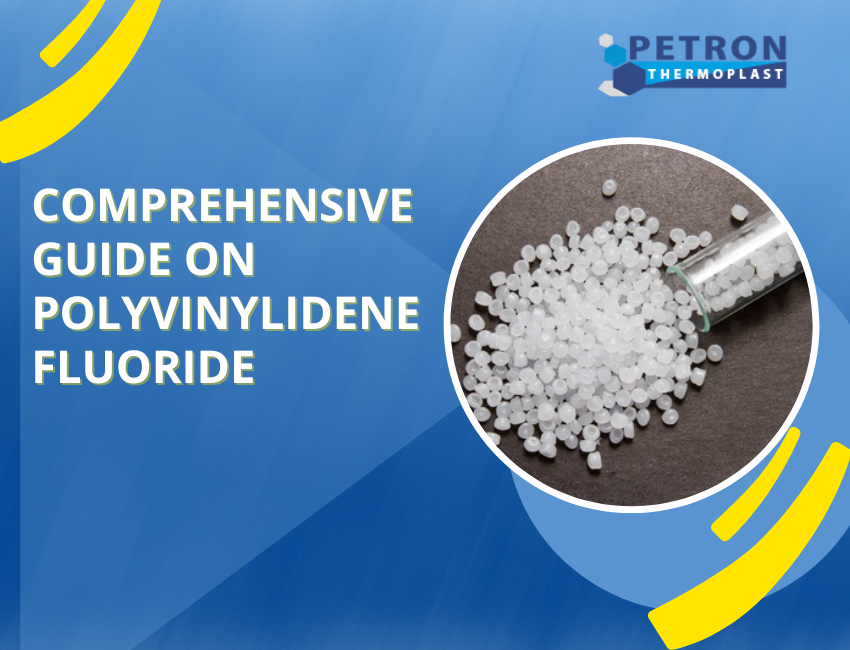
Polyvinylidene fluoride (PVDF) is a highly versatile polymer that has gained popularity in various industrial applications due to its remarkable properties. This comprehensive guide on Polyvinylidene Fluoride aims to provide readers with a complete understanding of the material, including its properties, applications, processing techniques, and benefits.
Polyvinylidene Fluoride (PVDF) Properties
PVDF is a thermoplastic polymer that belongs to the fluoropolymer family. It is characterized by its high melting point, excellent chemical resistance, and mechanical strength. PVDF is also highly stable and resistant to weathering, making it ideal for outdoor applications.
One of the unique properties of PVDF is its ability to resist chemical attack from a wide range of chemicals, including acids, bases, solvents, and oils. It is also highly resistant to UV radiation, making it suitable for outdoor applications where exposure to sunlight is a concern.
PVDF is also an excellent electrical insulator, making it ideal for use in electrical components and wiring. It has a low dielectric constant and a high dielectric strength, allowing it to withstand high voltage applications without breaking down.
PVDF Applications
PVDF has a wide range of applications due to its unique properties. One of the most common applications is in the chemical processing industry, where it is used for chemical storage tanks, piping systems, and valves. PVDF is highly resistant to chemical attack, making it an ideal material for use in harsh chemical environments.
Another common application of PVDF is in the electrical and electronics industry. It is used in wiring, cable insulation, and electrical components due to its excellent electrical insulation properties. PVDF is also highly resistant to heat, making it ideal for use in high-temperature applications.
PVDF is also used in the medical industry for applications such as medical tubing, implants, and surgical instruments. It is highly biocompatible, meaning it does not react with the body's tissues and does not cause any adverse reactions.
Processing Techniques
PVDF can be processed using various techniques, including injection molding, extrusion, and compression molding. Injection molding is a popular technique for producing complex parts with tight tolerances. Extrusion is used for producing long continuous lengths of PVDF profiles and tubing.
Compression molding is used for producing larger parts that require higher strength and rigidity. The process involves heating the PVDF material and then compressing it into the desired shape using a mold.
Benefits of Using PVDF
PVDF has numerous benefits over other materials, including:
- High chemical resistance
- Excellent electrical insulation properties
- High mechanical strength
- Good weathering resistance
- High melting point
- Biocompatibility
PVDF Ball Valve
A PVDF ball valve is a type of valve that is made from PVDF material. It is commonly used in chemical processing plants for controlling the flow of corrosive chemicals. PVDF ball valves are highly resistant to chemical attack and have excellent mechanical strength, making them ideal for use in harsh chemical environments.
What are the 5 Phases of PVDF?
PVDF (Polyvinylidene fluoride) is a polymer with five distinct phases that it can undergo. These phases are:
1. Alpha Phase:
This is the most common phase of PVDF, and it is the phase that is typically present when the polymer is in its crystalline state. In this phase, the molecular chains are packed in a tightly ordered manner, which results in a high degree of crystallinity and stiffness.
2. Beta Phase:
The beta phase is a less-ordered crystalline phase of PVDF that occurs at lower temperatures than the alpha phase. This phase has a lower degree of crystallinity than the alpha phase, which results in a lower stiffness and improved flexibility.
3. Gamma Phase:
The gamma phase of PVDF is a highly disordered, amorphous phase that occurs at even lower temperatures than the beta phase. In this phase, the molecular chains are not ordered in any particular way, which results in a very low degree of crystallinity and a highly flexible polymer.
4. Delta Phase:
The delta phase of PVDF is a metastable phase that is formed when the polymer is rapidly cooled from a high temperature. This phase is characterized by a higher degree of crystallinity than the alpha phase, which results in increased stiffness and reduced flexibility.
5. Epsilon Phase:
The epsilon phase of PVDF is the most recently discovered phase, and it is formed when the polymer is subjected to high pressures. In this phase, the molecular chains are highly ordered in a direction perpendicular to the pressure, which results in a high degree of stiffness in that direction.
What is the Solvent Casting of PVDF?
Solvent casting is a technique used to prepare thin films of a polymer by dissolving it in a suitable solvent and then casting the solution onto a substrate, followed by the evaporation of the solvent to obtain a solid film. PVDF (polyvinylidene fluoride) is a polymer widely used in various applications such as batteries, membranes, and sensors due to its unique properties, including high thermal stability, mechanical strength, and chemical resistance.
The solvent casting of PVDF involves dissolving the polymer in a suitable solvent, such as dimethylformamide (DMF), dimethylacetamide (DMAc), or N-methyl-2-pyrrolidone (NMP), to form a solution. The solution is then poured onto a flat substrate, such as glass or silicon, and allowed to dry at room temperature or under controlled conditions, such as in a vacuum oven or under a nitrogen atmosphere, to obtain a thin film.
The thickness and properties of the PVDF film can be controlled by varying the concentration of the polymer solution and the casting conditions, such as temperature and humidity. The resulting PVDF films can be used in various applications such as sensors, membranes, and energy storage devices.
Conclusion
In conclusion, PVDF is a highly versatile polymer that has numerous benefits over other materials. Its unique properties make it ideal for various industrial applications, including chemical processing, electrical and electronics, and medical applications. PVDF is also highly resistant to chemical attack and has excellent mechanical strength, making it an ideal material for use in harsh chemical environments. As the demand for high-performance polymers continues to grow, PVDF is expected to remain a popular choice for various industrial applications.
Read also: