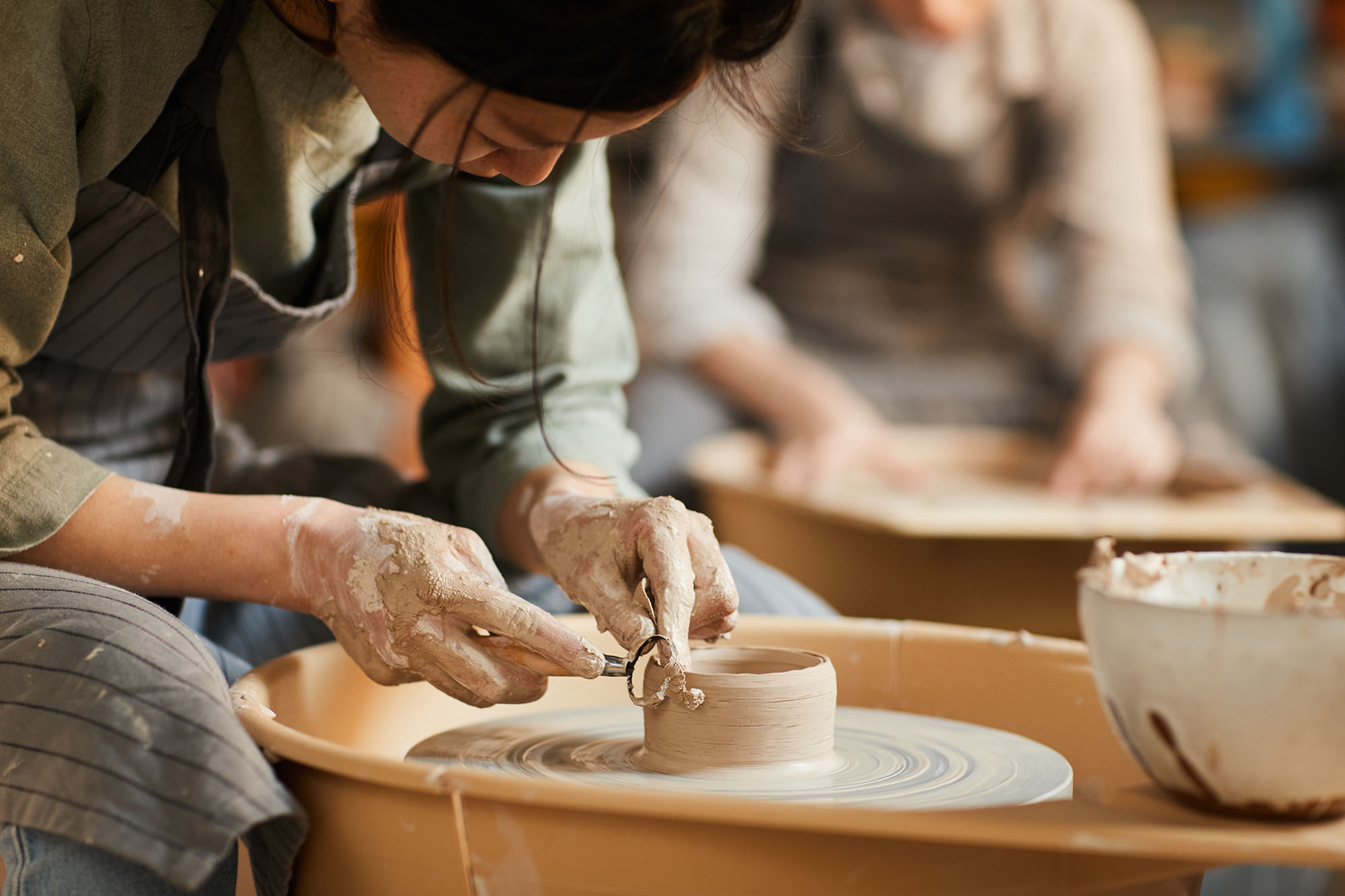
Pottery has been an integral part of human civilization for thousands of years. Whether functional or decorative, pottery objects are created through a meticulous process that involves shaping potter's clay and firing it in a kiln. The firing process, in particular, is a crucial step that transforms the pliable clay into durable and beautiful ceramic pieces. In this blog, we will delve into the pottery firing process, demystifying the various stages and exploring the magic that happens inside the kiln.
Greenware: Shaping and Drying
The journey of a pottery piece begins with a lump of clay. The potter first kneads and molds the clay, removing air bubbles and achieving a uniform consistency. Different techniques like throwing on a wheel or hand-building can be used to shape the clay into desired forms. Once the object is shaped, it enters the drying phase, known as the greenware stage. During this stage, the pottery piece gradually loses moisture, becoming firm and ready for firing.
Bisque Firing: The First Firing
The next step is to fire the greenware in a kiln. This initial firing is called the bisque firing or bisque kiln. The purpose of this firing is to remove any remaining moisture from the clay and to harden it. The kiln is heated gradually, reaching temperatures of around 1800°F (982°C), depending on the type of clay and desired results. The kiln temperature is carefully controlled to prevent cracking or breaking of the clay. After the bisque firing, the clay becomes ceramic and is referred to as bisqueware.
Glazing: Adding Color and Texture
Once the bisqueware has cooled down, it is ready for glazing. Glaze is a liquid mixture of minerals and pigments that, when fired, forms a glass-like surface on the pottery. Glaze can add color, texture and even functional properties to the ceramic object. The potter can apply glaze using various methods, such as brushing, dipping, or spraying. The glazed pottery pieces are then placed on stilts or kiln furniture to prevent them from sticking to the kiln shelves during firing.
Final Firing: The Transformation
With the glaze applied, the pottery is ready for its final transformation in the kiln. The temperature and firing duration during this stage depend on the type of clay and glaze used. The kiln is heated to higher temperatures, typically ranging from 2000°F to 2400°F (1093°C to 1315°C), depending on the desired effect. The heat causes the glaze to melt and fuse with the clay, forming a permanent bond. The kiln is carefully monitored throughout the firing process to ensure even heating and prevent any defects.
Cooling and Unloading
Once the final firing is complete, the kiln is allowed to cool down slowly. Rapid cooling can cause thermal shock, leading to cracking or shattering of the pottery. This cooling process, known as kiln cooling or thermal cycling, can take several hours or even days depending on the size of the kiln and the thickness of the pottery. Once the kiln has reached room temperature, the pots can be safely unloaded, revealing the final result of the firing process.
Post-Firing: Finishing Touches
After the pottery has been unloaded from the kiln, there are often some finishing touches required. This may involve sanding rough edges, polishing surfaces, or adding additional decorative elements. Depending on the potter's vision, the finished piece might undergo further processes, such as hand-painting, waxing, or gold leafing, to enhance its beauty and uniqueness.
The pottery firing process is an intricate dance between clay, heat, and time. Each stage contributes to the transformation of raw clay into a durable, functional, and aesthetically pleasing ceramic piece. From the initial shaping and drying to the bisque firing and glazing and finally, the transformative final firing, every step is essential in achieving the desired results.
Whether you're a potter yourself or an admirer of pottery, understanding the pottery firing process adds a new dimension to your appreciation of these artistic creations. Next time you hold a beautifully crafted ceramic mug or vase, you'll have a deeper understanding of the craftsmanship and artistry involved in taking clay from its pliable state to the remarkable transformation that happens inside the kiln.