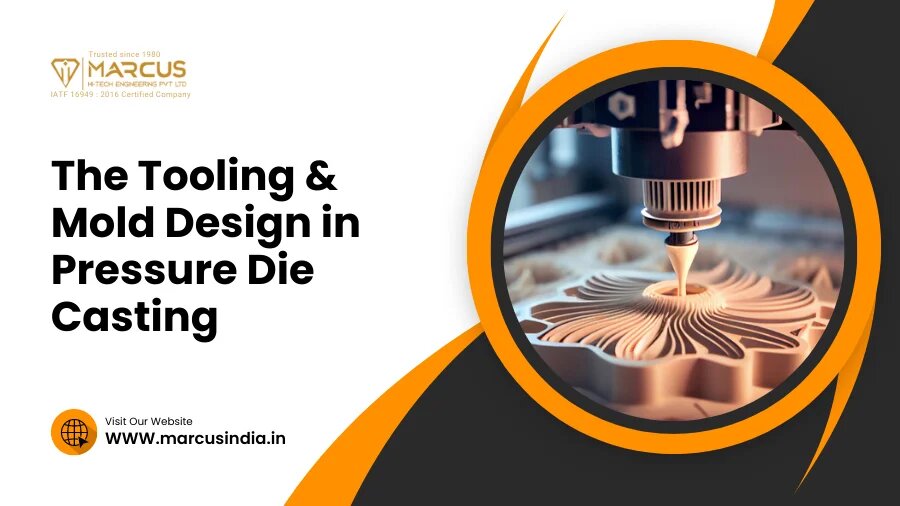
The Importance of Tooling and Mold Design in Pressure Die Casting
Pressure die casting is a highly versatile and efficient manufacturing process used to create complex and precise metal components. While the overall process involves melting and injecting molten metal into a mold, the significance of tooling and mold design cannot be overstated. In this article, we will delve into the pivotal role that tooling and mold design play in the pressure die casting process.
Introduction to Pressure Die Casting
Pressure die casting is a metal casting process in which molten metal is forced into a mold cavity using high pressure. This process is widely used for manufacturing intricate and high-quality components across various industries.
The Role of Tooling in Die Casting
Tooling refers to the molds, dies, and other equipment used in the die casting process. It's the foundation upon which the entire process rests. The design and precision of the tools directly influence the quality and accuracy of the final product.
Mold Design Considerations
Effective mold design is crucial for successful die casting. Factors such as material selection, cooling systems, and parting lines must be meticulously considered to ensure optimal results.
Precision and Complex Shapes
Tooling and mold design enable the production of components with exceptional precision and intricate geometries. This makes pressure die casting an ideal choice for industries that demand complex parts.
Material Flow and Solidification
Proper mold design facilitates the consistent flow of molten metal into the mold cavity and ensures uniform solidification. This minimizes defects and enhances component strength.
Cooling Systems for Optimal Results
Efficient cooling systems incorporated into the mold design help regulate the solidification process. This controls the microstructure of the component and enhances its mechanical properties.
Surface Finish and Component Quality
Well-designed molds contribute to superior surface finishes, reducing the need for additional post-processing. This results in components that meet strict quality standards.
Efficient Production Cycles
Optimized tooling and mold design lead to shorter production cycles. Reduced cycle times mean higher productivity and quicker turnaround for clients.
Cost-Effectiveness and Waste Reduction
Thoughtful mold design reduces material wastage, making the process more cost-effective and environmentally friendly in the long run.
Innovations in Tooling and Mold Design
Advancements in technology have revolutionized tooling and mold design. Computer simulations and precise machining techniques have elevated the quality of die-cast components.
The Expertise of Die Cast Engineers
Experienced engineers play a pivotal role in designing molds that align with the unique requirements of each project. Their expertise ensures the success of the die casting process.
Collaboration between Design and Production
Effective communication between design and production teams is essential. Collaboration ensures that the design intent is accurately translated into the final product.
Common Challenges and Troubleshooting
Mold-related issues can arise during the die casting process. Identifying challenges and implementing solutions promptly is crucial to maintaining production efficiency.
Continuous Improvement Strategies
The world of pressure die casting is ever-evolving. Regularly incorporating lessons learned from each project leads to continuous improvement in tooling and mold design.
Conclusion
In conclusion, tooling and mold design are the cornerstones of successful pressure die casting. From ensuring precision and quality to influencing production cycles and costs, their impact is undeniable. As industries continue to demand high-performing components, the art and science of tooling and mold design will remain at the forefront of innovation.
FAQs (Frequently Asked Questions)
Q1: How does mold design affect component quality?
Mold design significantly impacts component quality by influencing factors such as surface finish and material flow.
Q2: What role do cooling systems play in mold design?
Cooling systems in mold design regulate the solidification process, enhancing the mechanical properties of components.
Q3: How can industries benefit from pressure die casting's efficiency?
Industries can benefit from shorter production cycles and reduced material wastage, leading to cost savings.
Q4: What are some challenges in die casting mold design?
Challenges can include porosity, uneven solidification, and improper venting, among others.
Q5: What is the link between tooling design and environmental sustainability?
Efficient tooling design reduces material wastage, contributing to environmentally friendly manufacturing practices.