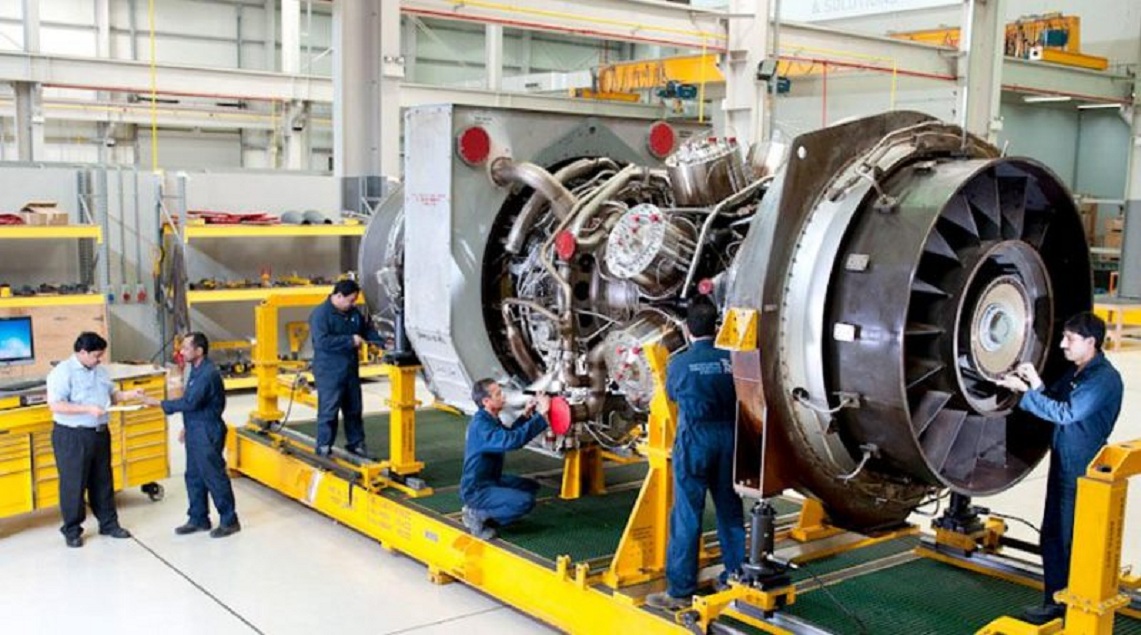
The power sector across the globe has been increasingly adopting gas turbines for power generation in recent years. Gas turbines offer several advantages like flexibility of fuels, high power density and relatively lower capital costs. However, with growing dependency on gas turbines, maintenance, repair and overhaul of these assets has become equally important for reliable power supply.
Rise of gas turbines in power generation
Gas turbines have seen widespread use in the power sector due to various factors. One of the primary reasons is the flexibility offered in terms of fuel options. Besides natural gas, gas turbines can also run on alternative fuels like diesel, heavier distillates and even syngas from biomass. This fuel flexibility enables reliable power supply even during gas shortages or disruptions in supply.
Gas turbines also offer relatively high power density compared to other conventional power generation technologies. This allows packaging multiple gas turbines in small footprint which is advantageous especially for distributed and captive power projects. The capital costs of setting up gas turbine based power plants are also lower compared to other high capacity power plants.
As per industry estimates, currently over 30% of total global power generation comes from gas turbines. In developing economies, the share of gas turbines is even higher owing to increasing energy demand and low capital requirements. Major economies like USA, China, Japan, India and Middle Eastern nations have seen rapid adoption of gas turbines for flexible, distributed and peak power supplies.
The importance of MRO
With rising gas turbine installations, their maintenance has become equally crucial for stable power generation. Regular maintenance, repair and overhauls help ensure long, reliable and efficient operation of gas turbines over 20-30 years of lifetime. Any neglect of MRO can cause unplanned downtimes, reduced efficiency and higher operating costs.
Original equipment manufacturers (OEMs) play a leading role in providing comprehensive MRO services to gas turbine owners and operators. Advanced condition monitoring, inspections, component repairs and replacement forms the core of MRO activities. OEM service centers are equipped with latest diagnostics tools, spare parts warehouse and skilled workforce to handle even complex repair and retrofit needs.
For old gas turbine models nearing the end of their technical life, extensive repairs and component life extensions become necessary. This is where OEMs expertise and global service network helps in extracting maximum value from ageing turbine assets before final decommissioning. Life extension upgrades via control system retrofits or customized inspections and maintenance plans are common MRO interventions.
Ensuring accessibility
As gas turbines are installed across utility plants, industrial facilities and remote locations, accessibility of MRO services has become equally critical. Being centrally located, OEM service networks can provide timely support through their regional delivery centers positioned worldwide.
Customers also need comprehensive long-term service agreements (LTSAs) with flexible maintenance schedules suitable for their plant operations. Such agreements involve preventive and reliability-centered maintenance planning along with inventory management of critical spare parts. OEMs have been enhancing their digital capabilities to enable remote condition monitoring, advisory and support for widely distributed gas turbine installations.
Cost optimization
With energy costs constantly rising, operators are seeking ways to optimize the expenses associated with gas turbine MRO. Here OEMs play a key role through value-added services like performance upgrades, life extensions and customized asset management programs. Reliability improvement measures pursued through data-driven predictive maintenance help reduce unexpected breakdowns and losses.
Similarly, digital fleet monitoring and spare parts management solutions assist in bringing operational efficiencies. Cost-plus and outcome-based long term service contracts transfer performance risks to OEMs while ensuring budget predictability for customers. Overall, adherence to prescribed OEM maintenance is found to maximize asset availability with least life cycle costs.
The way ahead
As gas turbine capacity addition gains further momentum globally, their efficient maintenance will be paramount. Independent service providers are also emerging but OEMs continue holding an edge given their extensive field experience and technical know-how. Considering the criticality of power supply, strict adherence to standardized OEM processes, quality parts and specialized workforce will be essential for reliable asset management.
Focus on digitization, advanced diagnostics, improved spares support and service delivery models are pathways for OEMs to amplify customer values. Outcome-based contracting will be a future trend. For asset owners, long term partnerships with OEMs ensure maximizing ROI from gas turbine investments over their design lives in a sustainable manner. Gas turbine MRO will remain a crucial cog in the expanding power industry landscape worldwide.
For more Insights, Read –
https://www.newswirestats.com/gas-turbine-mro-size-and-share-analysis/