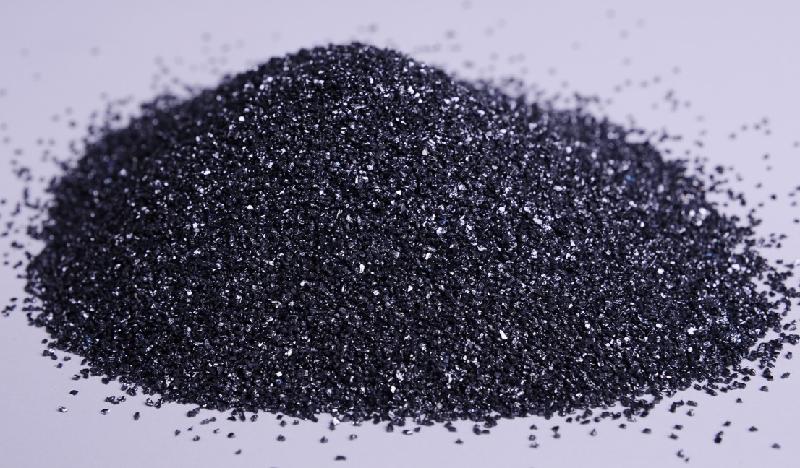
Chemical vapor deposition (CVD) silicon carbide is emerging as a revolutionary material for developing next-generation power devices. Silicon carbide has a wide bandgap which allows it to operate at higher temperatures, voltages, and frequencies than conventional silicon. This makes it ideal for applications where silicon falls short like fast charging electric vehicles, solar inverters, and 5G telecom infrastructure.
CVD silicon carbide wafers: Enabling key power applications
The ability to manufacture large diameter CVD silicon carbide wafers has opened up new vistas for power semiconductor devices. Researchers can now grow high-quality SiC crystals that are over 6-inches in diameter through an optimized CVD process. Compared to earlier 3-inch wafers, 6-inch wafers allow fabricating more power chips in a single substrate run which significantly reduces manufacturing costs. This has enabled the commercialization of 1200V and 1500V SiC MOSFETs and diodes targeted for electric vehicle drivetrains, solar micro-inverters, and fast battery charging systems. Going forward, even larger 8-inch wafers are being developed to meet the surging demand from EV and renewable energy sectors.
Superior material properties of CVD silicon carbide
At the material level, silicon carbide possesses exceptional dielectric, thermal, and carrier transport properties that silicon cannot match. Its wide ~3eV bandgap results in a breakdown electric field that is ten times greater than silicon. This allows SiC devices to operate at higher voltages with lower losses. CVD SiC also has a thermal conductivity rating two times more than silicon for effectively dissipating heat. Its high saturated electron drift velocity of 2x107 cm/s results in lower conduction losses and enables fast switching. These inherent properties of SiC have paved the way for developing more compact and efficient power conversion systems.
Advent of 1200V and 1500V SiC MOSFETs
Riding on the progress in CVD Silicon Carbide wafer fabrication, SiC MOSFETs with blocking voltages of 1200V and 1500V have recently been introduced by Wolfspeed, Rohm, STMicroelectronics and others. Compared to existing silicon IGBTs and MOSFETs, these 1200V and 1500V SiC MOSFETs provide up to 30% higher efficiencies at much smaller package sizes. Automotive manufacturers like Tesla, GM and Rivian are actively evaluating SiC MOSFET based electric vehicle drivetrains claiming to increase vehicle ranges by up to 5%. Another key application is three-phase solar micro-inverters where SiC MOSFETs help achieve Euro efficiency levels with compact form factors. This has greatly expanded the appeal of solar energy for both residential and commercial sectors.
Cost reduction enabling wider adoption
While SiC devices still command a higher price tag than comparable silicon parts, economies of scale from growing larger wafers and ramping up fab utilization is driving down costs. Mass production of 6-inch and 8-inch wafers is bringing down the substrate costs substantially. Device makers are also optimizing fabrication processes to increase yields. All these factors are making SiC devices increasingly competitive for mainstream industrial and automotive applications. By 2027, estimates project the EV drivetrain alone will require over 200 million SiC power modules annually. With established players like Infineon, ST, ON Semi and startup Achronix betting big on SiC, costs are projected to reduce by over 50% in the next 5 years. This will open up a plethora of new opportunities for silicon carbide in sectors like data centers, renewable energy, and rail transportation.
R&D advances expanding SiC capabilities
While significant progress has been made in commercializing 1200V-1500V SiC power devices, continuous R&D efforts aim to further enhance SiC technology. Researchers are developing new heterointerface passivation techniques for achieving lower Ron in thin wafer SiC MOSFETs. Novel doping and implantation schemes are being evaluated for improving carrier lifetimes. New device structures like trench MOSFETs and merged PiN-Schottky diodes promise even better conduction and switching performance. Epitaxial growth innovations may enable fabricating homojunction diodes and transistors for even higher voltage and current handling capability. Looking ahead, wide bandgap combinations of SiC and GaN are also being actively explored to realize next-generation hybrid devices for multilevel inverters above 10kV. Overall, silicon carbide is evolving as a truly disruptive material spearheading the new age of power electronics.
CVD silicon carbide has emerged as a revolutionary wide bandgap semiconductor material over the past decade due its unmatched capabilities for high power, high temperature and fast switching applications. Manufacturing breakthroughs in growing large diameter SiC wafers have enabled commercializing the first 1200V and 1500V power devices targeting automotive and solar energy sectors. Continuous technology advances in epitaxial growth, device fabrication and novel structures are further enhancing the performance limits of SiC. With the auto and renewable energy boom driving huge volume demand, silicon carbide is increasingly gaining traction as a mainstream technology for building more efficient electric grids and vehicles of the future. Though still more expensive than silicon initially, the rapid scaling of SiC is making it ever more competitive while opening new application frontiers. CVD silicon carbide seems poised to transform the energy landscape in the coming decade.
Explore Our More On CVD Silicon Carbide