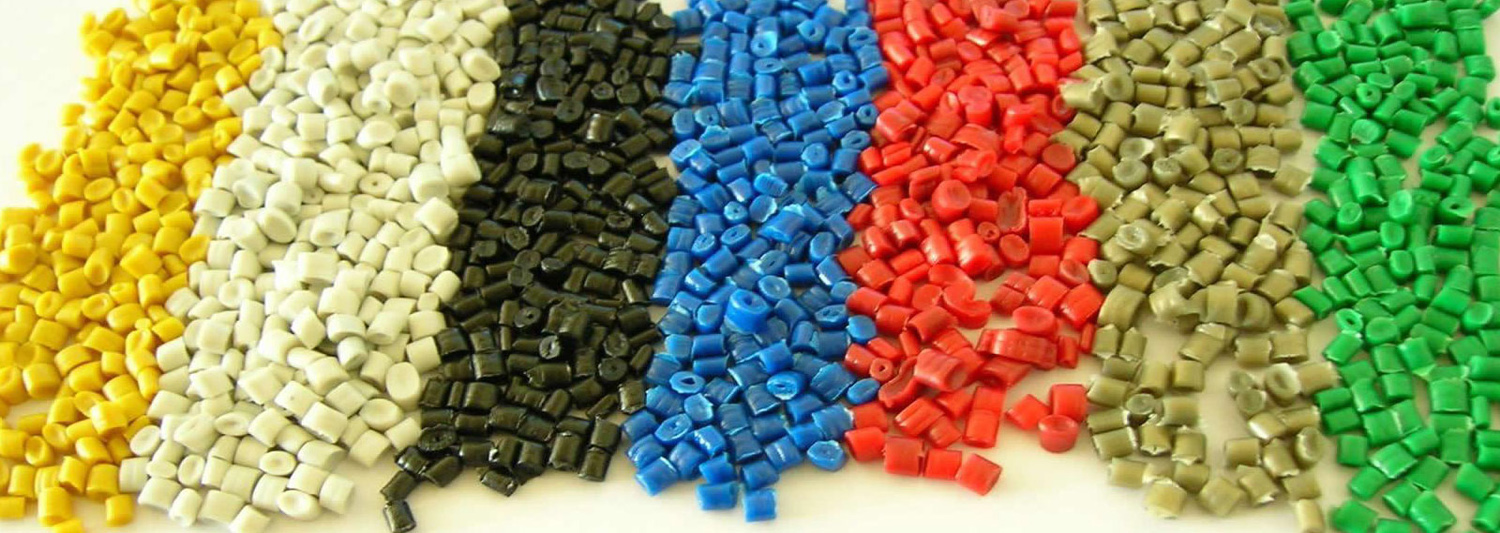
Introduction
Polyphenylene sulfide, commonly known as PPS, is a thermoplastic polymer with excellent chemical resistance and thermal stability. It has gained widespread use in a variety of engineering applications requiring high performance plastics. In this article, we will explore the properties and uses of PPS and discuss why it has become a popular choice for components involved in chemical processing, automotive, and electrical industries.
Chemical Structure and Properties
PPS is a linear polymer made by polycondensation of p-dichlorobenzene and sodium sulfide. This yields a rigid-rod polymer with inter-connected phenyl and sulfide groups in its backbone. The repeating structure gives PPS key strength and stability features. Its chemical structure is highly non-polar which results in strong resistance to solvents, acids and alkalis. It has high melting point of 280°C, allowing it to maintain integrity even at elevated temperatures. PPS also exhibits good dimensional stability, low moisture absorption, fatigue resistance and self-lubrication. These remarkable chemical and thermal stability properties along with durability make PPS suitable for demanding applications.
Applications in Chemical Processing Industries
The excellent chemical resistance of PPS makes it a preferred choice for components in chemical processing industries. PPS pipes, valves and fittings can handle corrosive chemicals like solvents, acids and alkalis without degradation. It is extensively used to transport strong acids like sulfuric and hydrochloric acid in refineries, chemical plants and waste water treatment facilities. PPS filaments are used to make protective fabrics for workers handling hazardous chemicals. Agitator shafts, pump housings and pressure vessels fabricated from PPS can withstand corrosive environments in these industries. Its resistance to hydrolysis also allows use in desalination plants.
Usage in Automotive Components
In automotive sector, PPS is gaining prominence for under-the-hood applications due to its heat resistance. PPS manifolds are manufactured for exhaust systems as they can withstand high continuous operating temperatures. Its low moisture absorption property ensures dimensional stability of manifolds during welding. PPS is the material of choice for engine covers and valve covers due to its durability even under extreme heat cycles. Switch brackets, ignition coils, fuel injectors and fuel system components often use PPS for its performance in variable temperatures inside the engine bay.
Electrical and Electronic Applications
PPS in Electrical Equipment
PPS is an ideal insulating material for use in electrical equipment owing to its excellent dielectric strength, arc resistance and self-extinguishing properties. It does not promote electric tracking or support combustion. PPS insulation helps improve safety of electrical equipment. PPS tapes, sleeving and wire enamels are employed as insulation materials in motors, generators, switchgears and transformers. Its good mechanical properties also make PPS suitable for terminal blocks, bushings and connectors in these systems.
PPS in Electronics
In electronics industry, PPS resin is injection molded to manufacture electrical connectors, sockets, relays and switches due to its resilience and electrical isolation. PPS cast resin sheets are used to laminate printed circuit boards for their durability and heat resistance. Miniature PPS parts play a crucial role in electrical components of medical devices, instrumentation and appliances. PPS filaments provide reinforcement in composites for housings of consumer electronics. Its ability to withstand radiation sterilization processes has increased adoption of PPS in electronics assemblies for medical equipment.
Conclusion
In summary, Polyphenylene Sulfide (PPS) exhibits a unique balance of properties that make it suitable for high-performance applications across diverse engineering sectors. Its excellent chemical and thermal resistance combined with mechanical strength enables replacement of metals with lower-cost PPS parts and components. Continuous research in PPS resin chemistry is expanding potential of this thermoplastic in more industries. Going forward, PPS will likely emerge as an engineering plastic of choice for high-end applications in harsh operating conditions across automotive, industrial and electronics domains.
Get more insights, On Polyphenylene Sulfide (PPS)