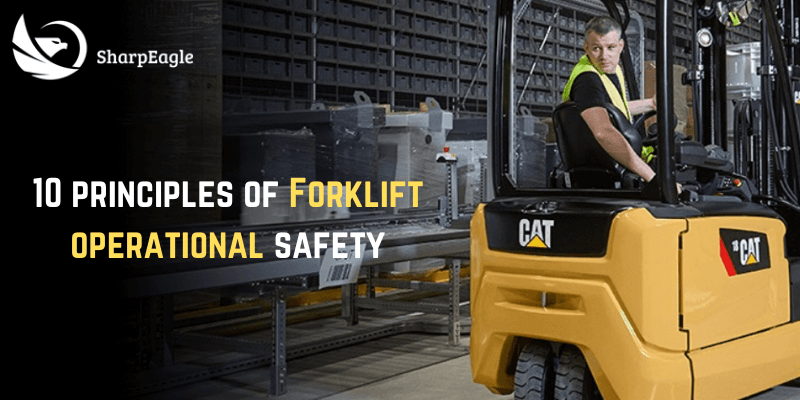
In warehouses, building sites, and other industrial settings, forklifts are a need. However, there are a lot of hazards associated with their functioning. Forklift accidents cause a great deal of injuries and fatalities every year, which emphasises the necessity of strict safety regulations.
At SharpEagle we’re dedicated to minimising the risk of accidents in your facility. And, the goal of this article is to provide supervisors and operators with the knowledge they need to effectively manage risks by exploring the fundamentals of forklift safety.
➢ Principal Causes of Accidents by Forklifts come under three categories
The primary causes of accidents, which generally fall into three categories - mechanical design, work environment, and user error - must be addressed when talking about the principles of forklift safety. Through comprehension of these classifications, establishments can formulate all-encompassing safety guidelines that alleviate hazards and improve the general security of forklift functions.
a) Mechanical Design
A forklift's ability to operate safely is largely dependent on its mechanical design. Malfunctions that could result in accidents can be caused by design defects or mechanical problems. Ensuring that every forklift is designed with safety in mind is crucial. This includes attributes like rapid and easy-to-use control systems, warning systems that notify operators of any problems, and dependable brakes.
To enhance the safety and efficiency of forklift operations, SharpEagle offers a range of products that align with the crucial elements of forklift design and maintenance. SharpEagle products are meticulously designed to enhance the safety, control, and reliability of forklift operations, adhering to high standards of mechanical design and operator safety.
These guidelines include routine inspections and maintenance, which guarantee the forklift's mechanical integrity. To shield operators from typical dangers like falling objects or tip-overs, safety elements such as load backrests, overhead guards, and seat belts must also be incorporated into the design.
b) Work Environment
A cluttered, poorly lit, or chaotic work environment is a hotbed for accidents. Factors like uneven flooring, narrow aisles, and high-traffic areas require specific forklift types and additional safety measures. The work environment must be regularly assessed to ensure it meets safety standards conducive to forklift operation.
c) User Error
Human error continues to be a highly manageable yet intricate element in the realm of forklift operation safety. Central to the principles of forklift safety is the necessity for in-depth operator training and mandatory certification processes. Operators must possess a thorough understanding of the specific forklift model in use and its operational boundaries, and exhibit adeptness in executing safe handling procedures.
Human tendencies such as overconfidence, distraction, or insufficient situational awareness are often the precursors to operational misjudgments that may culminate in mishaps. As such, it is imperative to have a strong culture that promotes ongoing improvement of safety awareness. Forklift operators must take a proactive approach to their responsibilities and acknowledge constructive criticism of their operational behaviour.
One effective way to reinforce safe operating procedures and provide forklift operators with the skills they need to handle emergencies is through the use of virtual training modules and regular safety drills.
Want to find out more about the reasons accidents happen in warehouses? Read the top 7 causes here!
10 Essential Principles of Forklift Operational Safety
Workers can finish their responsibilities and securely return home to their families when they work in a safe environment. Achieving that goal can be facilitated by being aware of forklift safety regulations. Here are the ten principles of forklift safety -
Forklift Certification is a Must
A certification recognizes the specific skill set needed to operate a forklift. This certification is more than just a piece of formal documentation; it is an indication that the operator has received the required training to follow the safety protocols associated with forklift operation.
Certified operators get training on safe equipment handling, danger recognition, and legal and workplace laws related to forklift operations. Operators are more prone to make mistakes without the necessary accreditation, which increases the risk of catastrophic mishaps, injuries, or property damage.
A wide range of subjects are covered in certification programs, from the fundamentals of using the controls to comprehending the laws of physics involved in lifting and moving loads. These programs also teach operators how to do routine maintenance and identify mechanical issues that need to be fixed right away. The workplace safety culture is strengthened when certification is renewed regularly, ensuring that operators are knowledgeable about the most recent safety regulations and operational procedures.
Proper Attire is a Must
The importance of proper attire in forklift operations cannot be overstated. Safety attire, which includes high-visibility jackets, safety footwear, and hard hats, serves as the first defence systems against workplace hazards. High-visibility jackets ensure that forklift operators stand out against their environment, making them more noticeable to other workers and machine operators. Safety footwear, often with steel toe protection, guards against crush injuries from falling objects or accidents, while hard hats protect against head injuries from low-hanging obstacles or accidental drops.
Moreover, the proper attire includes clothing that is well-fitted to prevent any fabric from getting caught in the machinery. Loose items like scarves, ties, or dangling jewellery can pose a significant risk if they become entangled in moving parts. Gloves with a good grip can help maintain control of the forklift’s steering and control mechanisms, and safety glasses protect the eyes from dust, debris, or any flying particles that could impair the operator's vision and lead to accidents.
Comprehensive Knowledge About the Forklift Class
Forklifts are classified according to their intended use and surroundings. To protect themselves and anyone around them, operators must have a thorough awareness of the forklift class they are operating.
For example, the terms of operation, fuelling requirements, and maintenance differ between internal combustion engine trucks (Class 4 and 5) and electric motor rider trucks (Class 1). For the equipment to be used safely and successfully, operators need to be aware of these distinctions. Operators may comprehend the capabilities and limitations of the equipment with the help of training tailored to the particular class of forklift they are using, which is crucial in preventing mishaps.
This knowledge also includes knowing how different attachments may impact the forklift's functionality. The load centre and capacity of the forklift can be changed via attachments, which can modify the handling characteristics. Operators must be able to modify their driving and load-handling techniques accordingly. Frequent training sessions can support the maintenance of this knowledge and notify operators of any equipment updates or modifications that may have an impact on how the equipment operates.
Daily Inspection of Equipment
Following forklift safety rules is crucial to prevent accidents during operations. Conducting daily inspections is like a protective shield for the industry, guarding against unexpected dangers. Every morning, operators need to carefully check their forklifts. They examine the tires, forks, brakes, steering, control panel, and safety devices to make sure everything is in good shape. It's essential to spot any signs of wear or potential issues and fix them before starting work. This isn't just a routine; it's a commitment to safety, ensuring the forklift is safe and ready for the day's tasks.
Daily safety checks aren't just about avoiding accidents; they're a smart move for the long-term health of the equipment. By identifying and fixing small problems early on, operators can prevent more significant issues from developing over time. Forklifts, the hard workers in heavy lifting, become reliable allies against potential hazards through these regular inspections. This consistent focus on safety becomes an integral part of daily procedures, protecting the efficiency and productivity of the industry.
Here’s more on how you can increase your forklift safety!
Maintain 360-Degree Visibility
It's imperative to keep eye contact with fellow workers and pedestrians. Operators must be able to see in all directions around the forklift, especially when moving loads that can obstruct their view. Operators may have to rely on spotters, cameras, or mirrors to accomplish this to navigate securely. To inform others of its existence, the forklift itself should have operational lights and an audio warning system, particularly in places where there are blind spots or where background noise could mask the sound of the engine.
Here’s some important aspects you need to consider before investing in forklift safety cameras.
Apart from safety equipment, operators must receive training on safe driving techniques that improve visibility. This includes driving at a speed that allows adequate reaction time, using the horn at intersections, and making eye contact with pedestrians or other drivers to ensure their presence is known. Operators should always be vigilant and avoid distractions that could impair their ability to observe their surroundings fully.
A significant percentage of forklift accidents can be prevented with the right safety features. Don't wait, enhance your forklift safety now!
A Floor Marking System Increases Safety
A floor marking system can increase worker safety. One should use yellow for areas prone to falling and stumbling. Red for fire hazards, fire equipment, and emergency switches. One can find signs to keep pedestrians away from the path of forklifts.
The strategic use of floor markings is essential when it comes to forklift operation safety. Forklift operators and pedestrians alike, this system acts as a visual language that conveys vital information. By clearly marking designated lanes for forklift activity, safe zones for foot traffic, and no-go zones for heavy machinery, it divides up distinct locations efficiently. Brightly coloured, colour-coded lines act as a silent sentinel, drawing attention to areas where extra caution is required, like sidewalks and the area around doors.
For floor markings to function as an integral aspect of forklift operational safety, their condition and clarity are paramount. These lines and symbols must stand out, resisting the blur of industrial activity and the dimness of poor lighting. Their upkeep is not a one-time event but a regular mandate, ensuring that they continue to be an ongoing guidance amidst the bustling warehouse activity. By conducting periodic evaluations and upkeep of these visual cues, a business commits to a foundation of safety and aligns with industry regulations, making the complex choreography of operating a forklift safely an attainable reality.
Forklift capacity is an essential factor
To stay safe with forklifts, it's crucial to know how much weight they can handle. Each forklift has a data plate that shows its maximum load capacity. Going beyond this limit is like pushing your strength too far – it can lead to the forklift tipping over or losing its load. The forklift operator, who's like a master of weights, needs to understand the cargo's weight and how it's placed on the forklift.
They should be aware of how the load's centre, height, and arrangement can affect the forklift's balance. Also, any changes to the forklift, like adding new attachments or making modifications, can change how much it can carry. By consistently learning how to manage loads properly, the operator makes sure the forklift stays safe and works smoothly in the busy world of industry.
Forklifts should not carry extra people
One rule we can't break is letting people ride on forklifts. Forklifts are designed for carrying stuff, not passengers. It's not just a suggestion; it's a basic safety rule.
To everyone working in warehouses – forklift operators, supervisors, and everyone involved in keeping things running smoothly – remember that adding an extra person to a forklift is risky. Even a small extra weight can mess up the balance and make the forklift and its riders tumble over during a sudden stop or turn. So, it's important to stick to this rule.
Supervisors and managers, make sure everyone knows about this rule through training and signs. Warehouse staff, be watchful, and don't let a quick ride become a dangerous situation. When dealing with heavy machinery, safety rules are like strong walls protecting us from accidents. Let's follow this rule seriously, as written in the manual, to keep everyone safe in the world of forklift operations.
The stability of the forklift is an important consideration
In the world of moving stuff around, keeping a forklift steady is super important for safety. If you operate forklifts, work in a warehouse, or manage the logistics side of things, think of your forklift's balance like a dancer keeping perfect time in a performance.
The stability triangle of a forklift is like its balance point. It's a special kind of maths that makes sure the weight, lifting, and how long the forklift lasts all stay in harmony. This maths is crucial to prevent accidents like tipping over or spilling loads. As an operator, you need to understand your forklift's personality – when it might tip and how strong it is. Pay attention to the weight you're carrying, how high you're lifting, and what the ground is like under your tires.
For managers and supervisors in charge, make stability a big deal in your meetings and plans. Everyone in the warehouse should be like balance experts, knowing that every load they carry is a promise to gravity. You have the power to turn safety ideas into real actions, making stability a natural part of how things work every day. This way, safety and getting the job done can work together smoothly.
Speed should be within limits
Respecting speed restrictions is a vital component of forklift operational safety in the busy field of material handling. Forklift drivers, warehouse employees, and supervisors all find great resonance in this idea, which serves as a continual reminder that speed and safety don't have to be mutually antagonistic. Understanding the balance between the capabilities of the machine, the type of load, and the surrounding environment is more important while operating a forklift within the specified speed limitations than just following the rules. Going too over the speed limit can have disastrous consequences, like mishaps, broken equipment, and possible worker injury. Consequently, every forklift trip—no matter how short or long—must be made with a careful balance between caution and hurry to guarantee that the speed is always in line with the operational environment.
Emphasising the value of speed control is crucial for anyone who supervises and manages logistics operations. Establishing a culture where efficiency is attained without sacrificing safety is the key. Frequent training sessions, conspicuous speed limit signage, and technology tools such as speed monitoring systems can function as continuous reminders of this concept. Speed control can become instinctive by fostering a culture in which team members take personal responsibility for their other's safety as well as their own. In this sense, regulating speed in the fast-paced world of supply chain management and logistics becomes a team effort, a mutual step toward creating a secure, effective, and peaceful work environment.
Conclusion
Within the intricate tapestry of logistics and warehouse management, the disciplined regulation of forklift speed emerges as a pivotal principle. It serves as a collective commitment, uniting forklift operators, warehouse staff, and management in a shared pursuit of operational excellence and safety. Embracing speed limits is not just about adhering to rules; it’s about nurturing a culture where the well-being of each individual and the integrity of operations are held in the highest regard. By implementing these, you’ll transform your logistics operations into a realm where efficiency, safety, and mindfulness coalesce, ensuring a secure and productive workplace!
SharpEagle Technology strives to make industrial atmospheres safe and secure with our state-of-the-art products and services. By using top-quality safety products, we ensure your site is highly secure and continues to perform tasks with utmost efficiency. Our product range includes Forklift Safety Solutions. We have expanded our horizon to 8 countries including UAE, Saudi Arabia, Oman, Kuwait, Bahrain, Qatar, India, and the UK. Want to safeguard your site from unnecessary hazards? Connect with us to stay clear of such mishaps.
Also Read : Does osha require forklift safety lights?
Forklift safety solutions offered by SharpEagle:
• Forklift Safety Camera System
• Forklift Anti-Collision System
• Forklift Radar Blind Spot Detection System
• Warehouse Traffic Management System
Did you know that effective forklift safety training can reduce accident rates by up to 30%. Prioritize safety with our comprehensive guide on forklift operational safety.
Forklift Operational Safety FAQs
Why is forklift safety training necessary?
Effective forklift training not only minimises workplace accidents and fatalities but also mitigates financial losses due to damaged goods. Untrained forklift operators pose a direct threat to themselves and others in the work area. Ensure safety, reduce risks, and protect both personnel and assets by prioritising comprehensive forklift training programs.
Are there specific guidelines for operating forklifts near pedestrians?
OSHA advises forklift operators to prioritise pedestrian safety by yielding the right of way. Due to the substantial size and power of forklifts, it is crucial for operators to pause, allowing pedestrians to safely clear the area. This precautionary measure ensures a safer work environment and aligns with OSHA's guidelines for responsible forklift operation.
You can call us at +971-45549547 or mail us at [email protected]