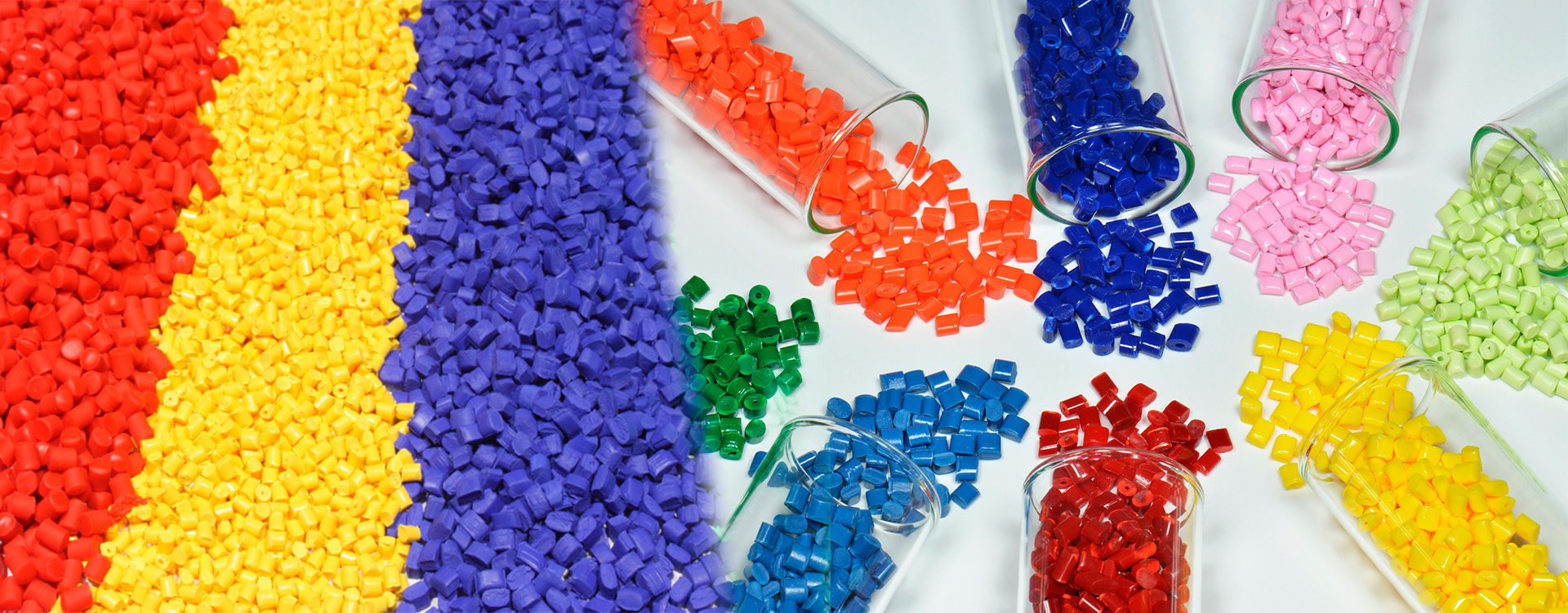
Thermosetting plastics are an important class of plastics that are irreversibly cured by the application of heat or other means of polymerization. Once molded or fully cured, they retain their shape even when reheated. Due to their heat resistance and durability properties, thermosetting plastics find applications across various industries. Let us explore the key aspects of thermosetting plastics in detail.
What are Thermosetting Plastics?
Thermosetting plastics are a type of plastic that undergoes a chemical change during the manufacturing process that alters their molecular structure in an irreversible reaction of cross-linking. In contrast to thermoplastics which soften with heating, thermosetting plastics harden with heat and cannot be remelted or remolded once cured.
The curing process commonly involves heating the material above its curing temperature in the presence of a curing agent like heat or EM radiation that drives the chemical reaction between the substrate and curing agent. The cross-linking permanently alters the molecular structure, rendering the material infusible and insoluble.
Common Types of Thermosetting Plastics
Some of the commonly used thermosetting plastics include:
- Polyester: Reinforced with fiberglass, it is mostly used for surfaces that require strength and durability like boat hulls, car bodies, etc.
- Epoxies: Used for adhesives, wind turbine blades, circuit boards due to their excellent adhesion and chemical resistance.
- Phenolics: Used in electrical switches and plugs, laminates due to heat resistance and strength.
- Melamine: Used in high-pressure laminates, tabletops, and countertops due to heat stability and aesthetic appeal.
- Polyurethanes: Used in adhesives, footwear, and construction applications due to flexibility and toughness.
- Silicones: Used for high-temperature seals and insulation due to heat stability up to 500°F.
- Unsaturated Polyesters: Used in fiberglass applications due to ease of reinforced with fiberglass.
Raw Materials and Manufacturing Process
The common raw materials used include thermosetting resins like unsaturated polyesters, epoxy, and phenol-formaldehyde. Reinforcements like carbon or glass fibers are also added to enhance strength and stiffness properties as per requirement.
The basic manufacturing process involves mixing the resin with curing agents, reinforcements, fillers, and additives. This mixture is then molded using compression, injection, or transfer molding under heat and pressure to initiate the crosslinking reaction. Additional post-curing may also be done to achieve full cure. Once hardened, the parts attain their final shape, properties and application.
Key Properties and Applications
Thermosetting Plastics have some distinct advantages that have increased their applications across myriad industries:
- Heat and Chemical Resistance: They can withstand high temperatures, solvents, and corrosive chemicals better than most thermoplastics.
- Dimensional Stability: Cured thermosets retain their dimensions and will not warp or change shape with variations in temperature.
- Durability: Their cross-linked structure makes them durable and damage-resistant for long-term usage under demanding conditions.
- Electrical Insulation: Phenolics and melamines provide self-extinguishing properties making them preferred for electrical equipment and appliances.
- Adhesion: Epoxies are commonly used as structural and high-performance adhesives due to superior adhesion properties.
Thanks to the above properties, thermosetting plastics find extensive uses in automotive, aerospace, marine, construction, electrical appliances, wind energy, consumer goods industries and more. Epoxy composites are used to manufacture aircraft bodies and wind turbine rotor blades. Fibre-reinforced polyesters are used to build boats, baths and storage tanks. Laminates are used for furniture, countertops and wall panelling. Unsaturated polyesters are used as matrices in fiberglass.
Environmental and Economic Considerations
While thermosetting plastics are advantageous in many applications, their production does involve some environmental and economic concerns:
- Non-Recyclable: Unlike thermoplastics, thermosets cannot be remolded or recycled due to the permanent cure. This reduces their sustainability.
- High Energy Input: The curing process requires high temperature and energy inputs that increase emissions and operational costs.
- Toxic Additives: Some formulations employ toxic additives like solvents, hardeners, coloring agents during processing. Proper handling is needed.
- Lifecycle Costs: Though durable, thermosets have higher upfront production costs and require replacement rather than repair at the end of service life.
Manufacturerers are addressing these by developing bio-based thermosets from renewable resources, promoting waste reduction through better production planning, and exploring recycling methods like feedstock recycling to produce lower-value products. Standardization of designs also eases disassembly and future recycling processes. Ongoing research continues to optimize the balance between performance and sustainability of thermosetting plastics.
Thermosetting plastics are a class of engineered materials that provide immense benefits of durability, dimensional stability and strength to critical applications. Though not readily recyclable, continual progress helps minimize their environmental footprint. With advances, thermosets will sustain their crucial role across industries for years to come.
Get more insights on Thermosetting Plastics