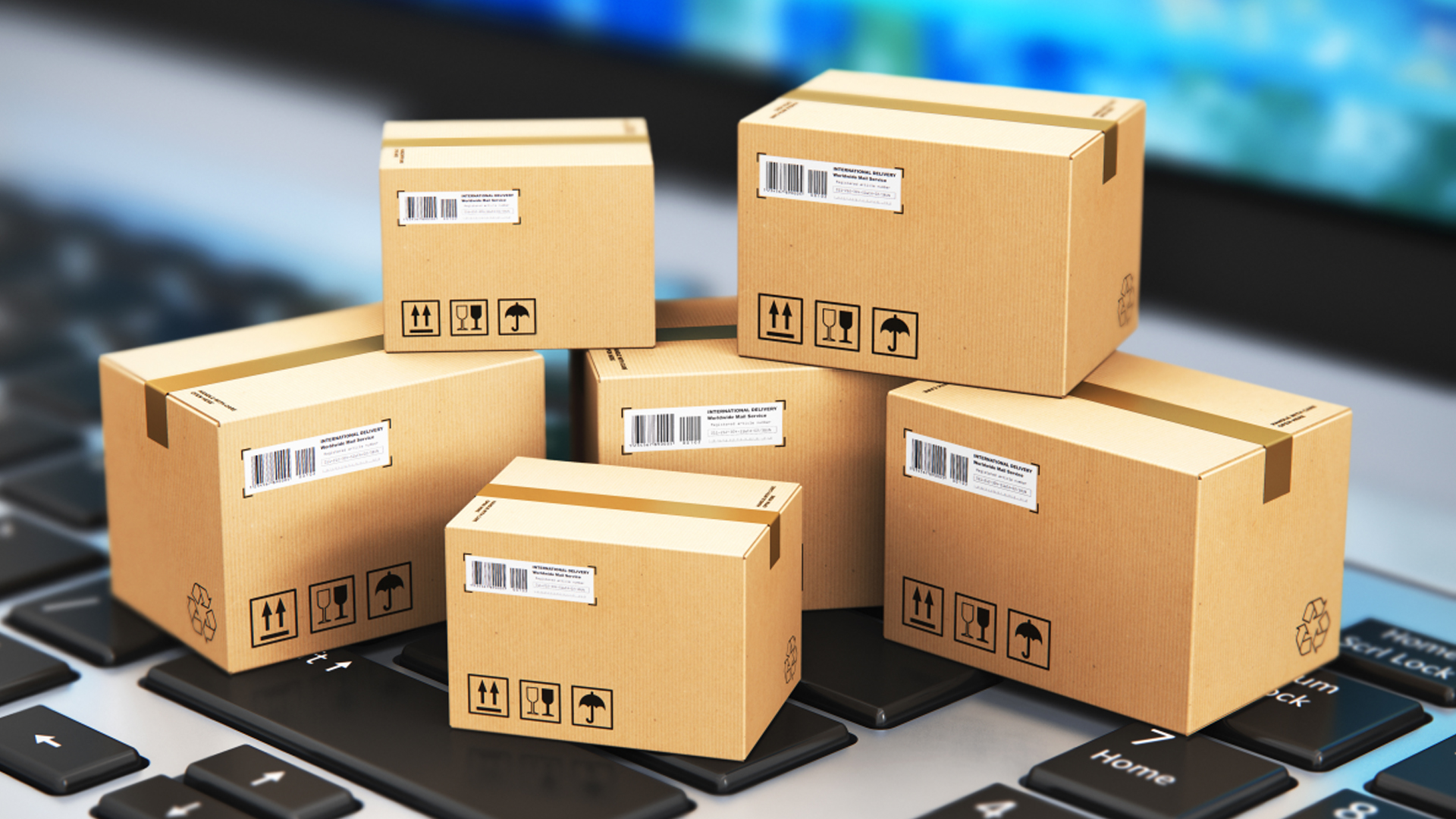
Packaging plays a vital role in protecting products from damage during transportation and storage. It is the first impression for customers and aims to attract them towards purchasing the product. However, for packaging to fulfill its functions effectively, it needs to undergo rigorous testing at various stages of development and production.
Importance of Packaging Testing
Thorough packaging testing helps verify if the packaging can withstand the rigors of distribution and use as intended. It evaluates the packaging's ability to prevent damage, contamination, and product deterioration under simulated transportation and storage conditions. This is crucial to maintain the safety, quality, and integrity of packaged goods. Some key reasons why packaging testing is important are:
- Ensuring Regulatory Compliance: Packaging Testing Market needs to comply with various industry and global regulatory standards pertaining to materials, safety, reuse, and disposal. Testing verifies compliance to regulations.
- Preventing Product Wastage: Damaged or contaminated products cannot be sold and lead to wastage. Testing packaging withstands distribution abuse prevents such loss.
- Maintaining Brand Reputation: Packaging failure can damage brand reputation if products are delivered damaged or expire prematurely. Thorough testing helps uphold brand reputation.
- Reducing Risk of Product Recall: Failed packaging can result in product recalls costing companies significantly. Rigorous testing eliminates such risks and associated financial losses.
- Enhancing Customer Satisfaction: Customers expect durable and protective packaging that keeps products fresh till last use. Testing packaging for strength and barrier properties enhances customer satisfaction.
Types of Packaging Tests
Depending on the packaging material, product type, and distribution conditions, various tests are conducted at different stages:
Design Validation Testing
This tests early packaging prototypes to validate the design can meet requirements before design freeze and tooling. Tests include closure/opening tests, drop tests, vibration/shock tests etc.
Material Testing
Raw material properties are tested to verify specifications. Tests include thickness measurement, seal strength, barrier properties, tensile strength etc.
Process Validation Testing
This validates packaging processes like filling, sealing, printing meet specifications. May include lab and production line trials.
Shipping/Distribution Testing
Simulates real distribution abuses as per packaging standards like ISTA, ASTM. Tests include vibration, temperature cycling, compression, drop tests etc.
Accelerated Aging Testing
Uses extreme temperature, humidity to artificially age packaging and check compliance of shelf life under real storage conditions.
Extractable and Leachable Testing
Detects substances extracted from packaging into product which may affect safety, legality or functionality over storage period.
Usability/Consumer Testing
Evaluate packaging for ease of use, disposal compliance from consumer point of view with surveys, focus groups.
Retail/Display Testing
Simulates retail shelf conditions like compression, impact, vibration to check durability during distribution to retail shelves.
Drop Testing for Rigid Containers
One of the most important distribution simulation tests, it evaluates containers' ability to withstand free fall impacts without failure or product damage. Various drop heights and angles are applied to mimic falls during handling and transportation from bottom, edges, corners or faces. Containers undergo multiple cycles of drops to verify consistent performance. Accelerometers record forces on container for analysis.
Real-Time Aging and Distribution Simulation
Climatic chambers like Boxes developed by companies precisely simulate real-world conditions packages undergo for distribution and storage. Parameters like humidity, temperature, vibration dynamics, drop heights can be programmed according to ISTA or ASTM protocols for complete distribution simulation testing. This efficiently replicates timeline of complete distribution cycle in a fraction of actual time, putting less time constraints on product development.
Thorough packaging testing helps ensure products reach the marketplace safely by validating packaging can withstand production, distribution, and storage. It plays a pivotal stealth role in protecting brand reputation and minimizing risks of product damage, expiration and recalls. With rigorous testing complementing design and material validation, companies can deliver consistent quality and foster customer loyalty through robust packaging performance. Testing thus remains integral to the packaging development process in maintaining product quality and safety for end users.
Get more insights on Packaging Testing Market