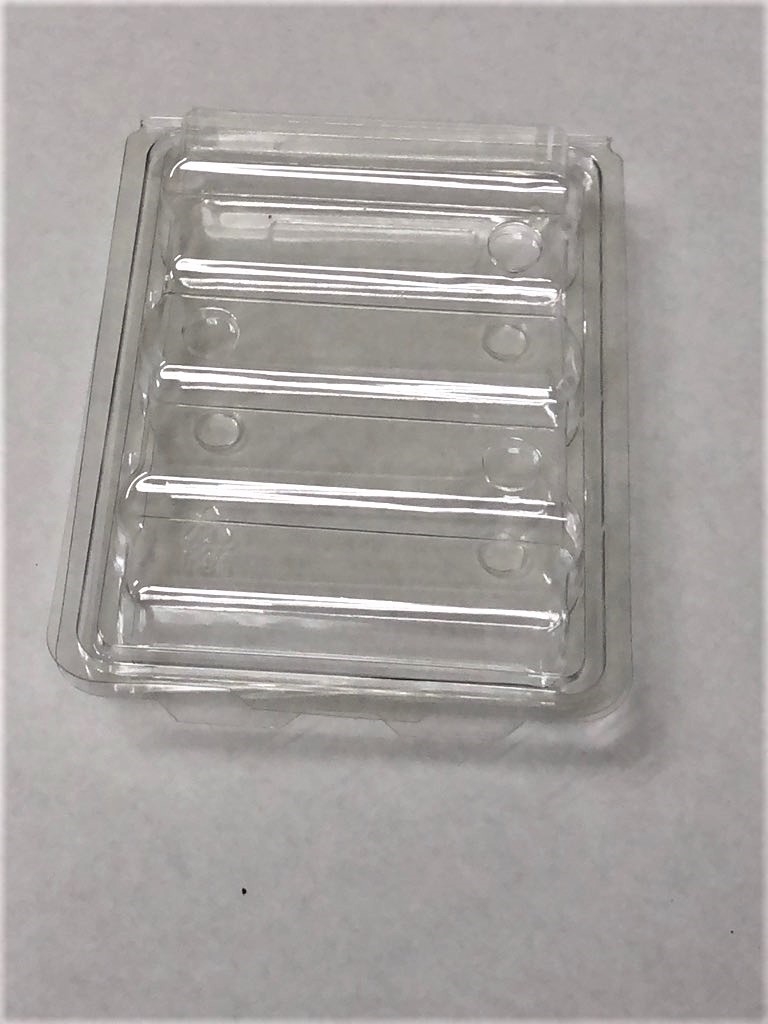
History and Evolution of Blister Packaging
Blister packaging was first developed in the 1920s to safely package small medical items like tablets and capsules that were prone to damage. The earliest forms used stiff paper or cardstock to form the backing component and a layer of clear cellophane or PVC film heat-sealed to the paper to form raised cavities or "blisters" holding the product. Through the 1940s and 50s, new thermoforming techniques were developed using plastic sheets like PVC, polyvinylidene chloride (PVDC) and polypropylene to improve strength and functionality. Today, modern blister packaging utilizes a wide variety of plastic films and foil/film laminates tailored for specific product and market needs.
Benefits for Product Protection and Supply Chain Efficiency
One of the key advantages of blister packs is their high level of product protection. The formed plastic cavity firmly holds each item in place, preventing damage from crushing or other impacts compared to loose or bagged packaging. Moisture, gas and light barriers provide further defenses against tampering or product deterioration over long shelf lives. For supply chains, blisters allow efficient unit-level packaging on high-speed automated machinery. The hard plastic shell also facilitates logistics like stacking, improved space utilization in trucks/containers and durable barcoding/labeling vs. soft packaging.
Design Customization for Any Product Type
Blister Packaging today can be tailored for an incredibly wide range of product types from small tablets and capsules to potentially larger medical devices, electronic components, jewelry, hardware parts and more. Package design is highly customizable with cavity sizes, shapes, numbers per package, additional features like pealable lidding or printed folding instructions. Multi-layer plastic construction allows inclusion of printed folding instructions or desiccant packets inside. Specialty design capabilities include child-resistant for OTC drugs, tamper evidence seals and customformed cavities molded precisely to a product's dimensions for tight fitting protection.
Ensuring Product Integrity and Brand Trust
With products that consumers ingest or use on/in their bodies, maintaining integrity of the product free from tampering becomes critical. For the pharmaceutical industry in particular, well-designed child-resistant blister packs offer peace of mind that the product remains sealed until use. For retail, tamper evident seals let customers inspect the package is intact before opening, building confidence in brand and retailer. The clear materials of modern thermoformed blisters also allow full visibility of contents inside, a benefit for brands wanting to highlight their products on shelf. Combined, these factors help brands establish trust that their products remain effective and safe from the factory to the consumer's hands.
Regulatory Compliance Standards are Critical
As populations age and medical consumerism rises globally, regulatory standards for pharmaceutical and supplement packaging continue becoming more stringent. Key worldwide compliance certifications blister manufacturers adhere to include ISO 15378 for primary packaging materials, ISTA 7D distribution simulation testing, child-resistant certifications like 16 CFR §1700 in the U.S. Specialized designs may require additional certification like those developed by the U.S. Poison Prevention Packaging Act or approvals from individual countries' health ministries and drug authorities. Full traceability is also mandatory, requiring sophisticated production management systems. Strict compliance with global standards earns blister packs continued approval for protecting consumers and the brands that service them.
Environmentally-Conscious Sustainable Options
As environmental concerns rise across industries and sectors, many blister packaging suppliers now offer sustainable options. Material variants include fully recyclable PVC and polypropylene versions, bioplastics produced from renewable plant starches or sugars, and FSC-certified paperboard substrates. Lighter-weight designs improve transport fuel efficiency and downgauged films minimize plastic usage. Post-consumer recycled content, compostable formats, and end-of-life take back programs further solutions to reduce waste. Sustainable options allow responsible brands to meet consumer demand for packages respecting the planet, an important factor as regulatory restricted plastic lists expand. Overall, the versatile thermoform blister packaging format delivers superior product protection with viable sustainable options for the future.
Get More Insights on Blister Packaging