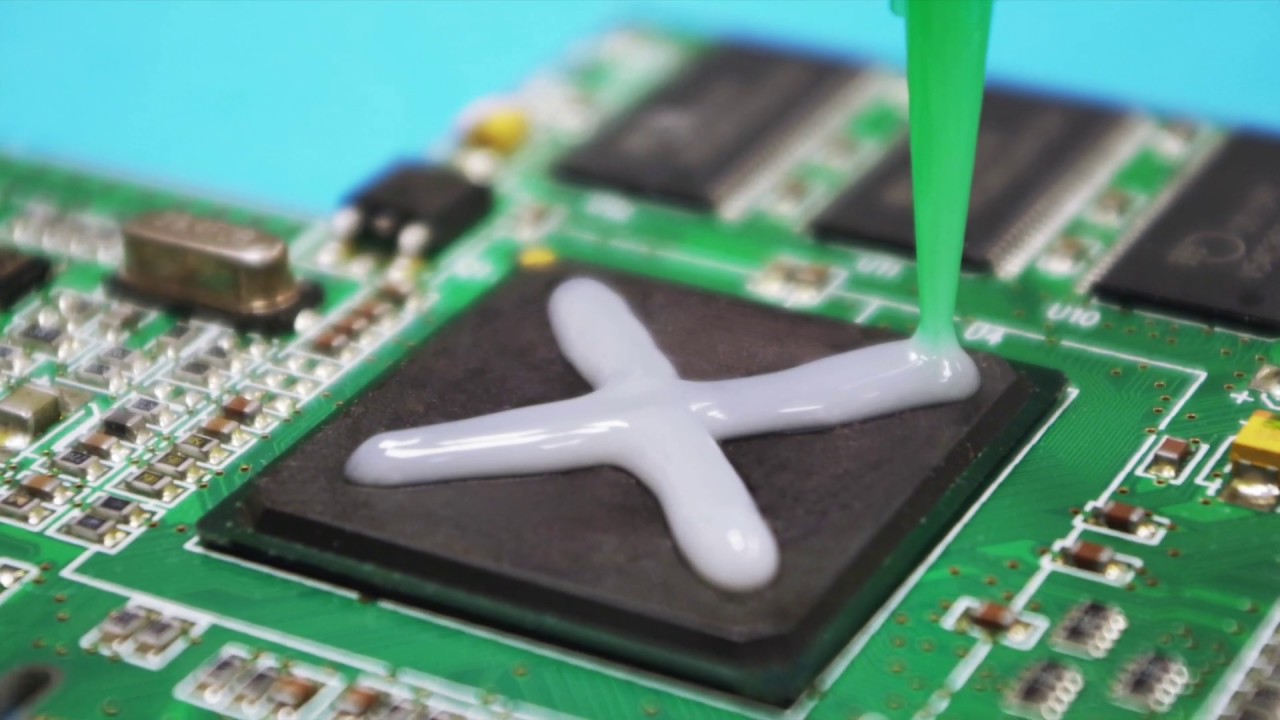
Introduction to Electrically Conductive Adhesives
Electrically conductive adhesives are adhesives that conduct electricity and are used to bond electrical and electronic components together. They help join connections through conductive particles that are dispersed in an organic adhesive matrix. These adhesives provide electrical conductivity between bonded parts while also offering mechanical adhesion or "stickiness".
Mechanism and Types of Electrically Conductive Adhesives
Electrically conductive adhesives derive their conductivity from the inclusion of conductive fillers within the adhesive matrix. The three main types of fillers used are silver, copper and carbon. Silver-filled adhesives are the most commonly used due to silver having the highest electrical and thermal conductivity of these materials. The silver fillers within the adhesive help form a conductive path for electricity to flow between connections.
Some key types of electrically conductive adhesives include:
- Anisotropic Conductive Adhesives (ACA): Contain conductive particles in a non-conductive adhesive binder. Particles only conduct crosswise to create Z-axis conductivity important for applications like IC bonding.
- Isotropic Conductive Adhesives (ICA): Have conductive fillers evenly dispersed to provide conductivity in all directions, ideal for simpler connections not relying on Z-axis conductivity.
- Thermally Conductive Adhesives: Used to dissipate heat with additives like silica, boron nitride or alumina to conduct heat away from components.
- Electrically Insulating Adhesives: Non-conductive adhesives used for structural applications requiring electrical isolation between parts.
Applications of Electrically Conductive Adhesives
The main uses of electrically conductive adhesives are in electronics assembly where they are being increasingly used instead of traditional soldering methods. Some key applications include:
- Integrated Circuit (IC) Bonding: ACAs are widely used to attach die to substrates or packages in IC manufacturing due to their Z-axis conductivity. This removes the need for gold wire bonding.
- Automotive Electronics: CONNECTING touchscreens, sensors, lighting and other components in increasingly electrified vehicles.
- Mobile Device Assembly: ICAs and ACAs are commonly used to assemble displays, cameras, batteries and other parts in smartphones, tablets and wearables.
- 5G and Telecommunications: Electrical Conductive Adhesive play a role in assembling the complex multilayer printed circuit boards used for 5G networking hardware.
- Avionics and Aerospace: Harsh environment applications require highly reliable adhesion for instruments, controls and other aircraft/spacecraft electronics.
Advantages Over Soldering
The use of electrically conductive adhesives provides several advantages over traditional soldering methods:
- No High Temperatures: Soldering uses temperatures over 200°C whereas adhesives cure at lower temperatures, reducing thermal stress on components.
- Lighter and Thinner Connections: Adhesive joints produce less bulk than solder so assemblies can be slimmed down. This is important for mobile/space applications.
- Improved Reliability: Adhesive joints exhibit greater resistance to vibration and thermal cycling stresses thanks to compliant bonding and reduced mechanical stresses at the interface.
- New Design Opportunities: Adhesive connections allow for novel three dimensional assemblies which would be difficult or impossible with soldering.
Growth and Future Trends
The market for electrically conductive adhesives has grown steadily as their use expands in electronics manufacturing. The overall conductive adhesives market size was valued at around $5.6 billion USD in 2021 according to Allied Market Research and is projected to reach over $9 billion by 2030 with a 6.4% CAGR.
Looking ahead, some key factors influencing future market growth include:
- Miniaturisation of devices driving need for thinner adhesive interconnections.
- Expanding use in automotive/ EV electronics, 5G hardware and augmented/virtual reality devices.
- Developing adhesive technologies supporting advanced applications like temperature sensing or flexible/stretchable circuits.
- Testing of adhesives in harsh aerospace/defense applications and growing space economy.
- Improving conductive particle loading/stability and gap-filling properties of adhesives.
In summary, electrically conductive adhesives are poised to play an increasingly important role in modern electronics manufacturing thanks to their versatility, reliability advantages over soldering, and enabling of novel designs. Their use will continue expanding across industries as technologies become ever more interconnected.
Get more insights on This Topic- Electrically Conductive Adhesives