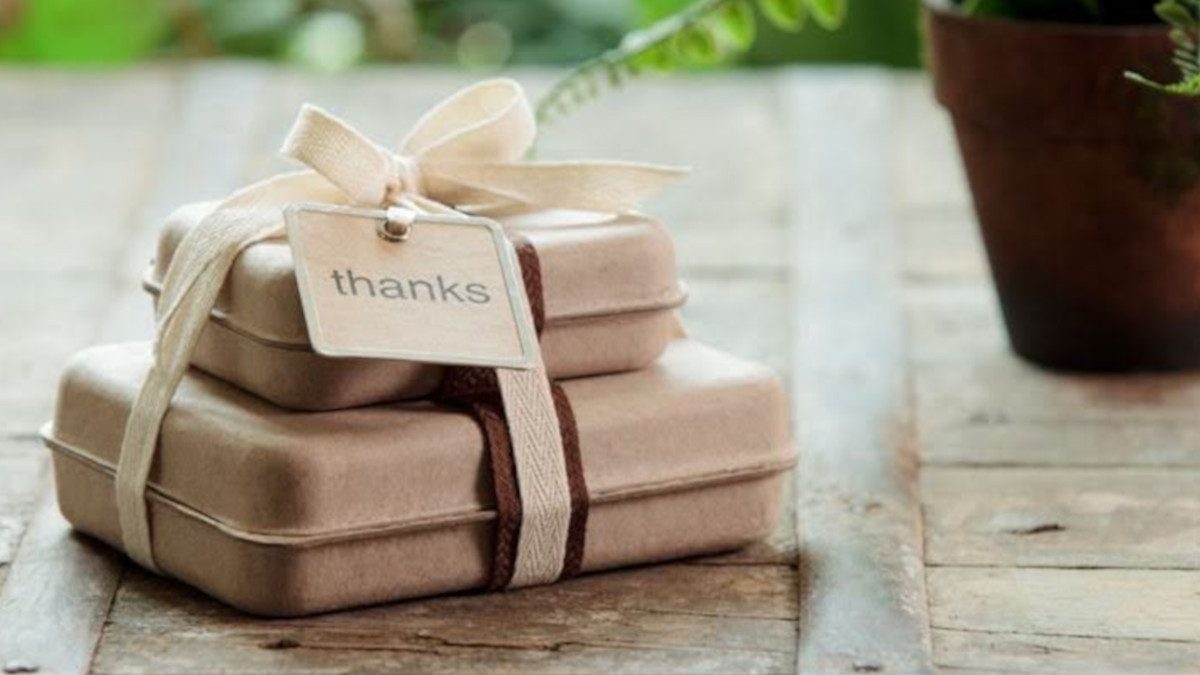
Introduction to Molded Fiber Pulp
Molded fiber pulp, also known as molded pulp or molded fiber, is a packaging material made from recycled newspaper, corrugated boxes and other paper scrap using a molding process. In the molding process, the recycled paper fibers are combined with water and formed into dense blocks using molds and dies in hydraulic presses. The molded pulp blocks can then be cut or stamped into various shapes used for protective packaging.
History and Manufacturing Process of Molded Fiber Pulp
Molded fiber pulp has been around since the late 19th century but gained more popularity in the mid-20th century. Its manufacturing process starts with collecting newspaper, cardboard and other waste paper that is cleaned, sorted, shredded and turned into pulp. Water is added to this pulp which is then laid into molds and pressed at high pressure to remove water, compress the fibers and set the shape. Excess pulp is trimmed off and the molded form is dried using hot air ovens. Modern molded fiber manufacturers use automated molding machines that can produce many identical pulp packages in quick succession.
Applications and Usage across Industries
Due to its sustainability, rigidity and cost-effectiveness, Molded Fiber Pulp Packaging finds usage across several industries for protective and retail packaging applications. Some common uses include:
Consumer Goods Packaging
Molded fiber is widely used for protective packaging of consumer goods like electronics, appliances, furniture, jars and glass containers. Its cushioning properties prevent damage to goods during transportation or storage. Reusable molded trays are also used for retail display of consumer products.
Food Packaging
Food packaging applications include protective food trays, containers for takeaway food items like salads, desserts or fast food, berry clamshell containers and molded serving bowls or plates. Its sustainability makes it an eco-friendly choice for restaurants and food service industry.
Automotive and Industrial Parts Packaging
Molded pulp end caps, corner boards and inserts provide custom fits for space-efficient packaging of engine parts, hardware and industrial components during shipping. Its strength handles rough handling during logistics.
Horticultural Packaging
Plants, flowers, pots and gardening accessories are commonly shipped in molded fiber pulp trays, cell packs and fiber pots to prevent damage. Some pulp pots can even be planted along with the contents.
Advantages of Molded Fiber Pulp Packaging
The key advantages that have led to the growth of molded fiber as an eco-friendly packaging option are:
Renewable and Recyclable: Made from recycled pulp, molded fiber is an inherently sustainable material. Used packages can also be recycled.
Rigidity and Strength: When compressed during molding, pulp fibers bind tightly providing sufficient rigidity and compressive strength for protective packaging.
Cushioning: Its resilience acts as vibration dampening cushioning to prevent damage to fragile contents.
Moisture-Resistance: Packages can withstand some absorption and re-release of moisture without losing shape.
Customizability: Molds allow fabrication of custom shapes and sizes as per product and application requirements.
Cost-Effectiveness: With abundant low-cost pulp raw material and high-speed machinery, molded fiber offers competitive pricing over thermoformed plastics.
Printability: Package surfaces can bear graphic customization, product information and branding through printing.
Challenges and Future of Molded Fiber Pulp
Despite its various advantages, certain limitations have slowed wider commercial use of molded fiber. Its hydrophilic nature imparts low moisture barrier compared to plastics and it cannot completely replace plastic or polystyrene alternatives in all applications. However, ongoing innovations aim to address such issues through lignin/wax coatings, lamination or addition of barrier layers. New production technologies also target higher strength, moisture resistance and printability. With environmental sustainability in focus, the future remains bright for molded fiber pulp as a protective packaging medium, especially for moisture-tolerant products. Continuous improvements will expand its uses further across industries.
Get more insights, On Molded Fiber Pulp Packaging