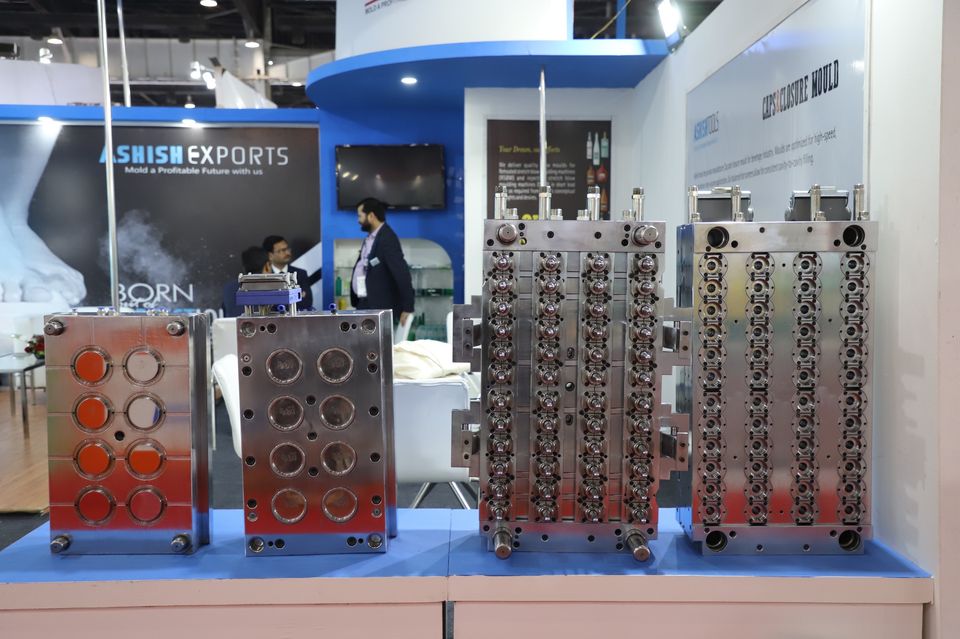
Pet Preform Mould Manufacturer And Supplier in India
Manufacturing pet preform moulds requires a combination of technical expertise, precision, and attention to detail. There are several different techniques involved in the mould manufacturing process that contribute to the quality and efficiency of the final product. One of the most important techniques in pet preform mould manufacturing is the design phase.
This involves creating a 3D model of the desired shape and dimensions of the preform. The design must take into account factors such as the material being used, the intended use of the bottle, and any specific requirements or constraints. Once the design is finalized, the next step is to create the mould itself. This can be done using a variety of methods, including CNC machining, electrical discharge machining (EDM), and 3D printing. Each method has its advantages and limitations, and the choice will depend on factors such as the complexity of the design and the desired level of precision. After the mould is created, it undergoes a series of finishing processes to ensure a smooth surface and accurate dimensions. This may involve polishing, grinding, and heat treatment. The mould is then ready for use in the pet preform manufacturing process.
Pet preform production
Pet preforms are the initial form of plastic bottles, and they are produced using injection moulding technology. The pet preform manufacturing process involves several steps, each of which is crucial for producing high-quality preforms. The first step in pet preform production is the preparation of the raw material. PET resin, which is a type of polyester, is typically used in the production of preforms. The resin is heated and melted, and then it is injected into the mould cavity under high pressure.
The temperature and pressure must be carefully controlled to ensure that the preforms are formed correctly and without any defects. Once the preforms are injected into the mould cavity, they undergo a cooling process to solidify and take the shape of the mould. This is typically done using a cooling system that circulates chilled water or air around the mould. The cooling time can vary depending on factors such as the design of the preform and the ambient temperature. After the preforms have cooled and solidified, they are ejected from the mould cavity and undergo a trimming process to remove any excess material. The preforms are then ready to be sent to the bottle manufacturing facility, where they will be heated again and blown into their final shape.
Pet preform moulds
Pet preform moulds are crucial components in the pet preform manufacturing process. The quality and precision of these moulds directly impact the efficiency and consistency of the bottle manufacturing process. Here are some best practices to consider when it comes to pet preform mould manufacturing:
1. Material selection: The choice of material for the mould is important, as it needs to be able to withstand the high pressures and temperatures involved in the injection moulding process. Steel alloys, such as stainless steel or tool steel, are commonly used for pet preform moulds due to their durability and heat resistance.
2. Precision engineering: Pet preform mould need to be manufactured with high accuracy and precision to ensure that the preforms are formed correctly and without defects. Advanced machining techniques, such as CNC machining and EDM, can help achieve the required level of precision.
3. Surface finish: The surface finish of the mould cavity is critical for producing smooth and defect-free preforms. Polishing and other finishing processes are used to achieve the necessary surface finish, which can help reduce friction during the injection moulding process and improve the overall quality of the preforms.
4. Cooling system design: The design of the cooling system in the mould is important for efficient cooling and solidification of the preforms. Properly designed cooling channels can help reduce cycle times and improve productivity.
5. Maintenance and repair: Regular maintenance and repair of the pet preform moulds are essential to ensure their longevity and performance.
This includes cleaning, lubrication, and inspection of the moulds to identify any wear or damage that may affect their performance. In conclusion, pet preform mould manufacturing plays a crucial role in the production of high-quality plastic bottles. By following best practices in mould manufacturing techniques, pet preform production, and pet preform mould design, manufacturers can ensure the efficiency and consistency of the bottle manufacturing process.