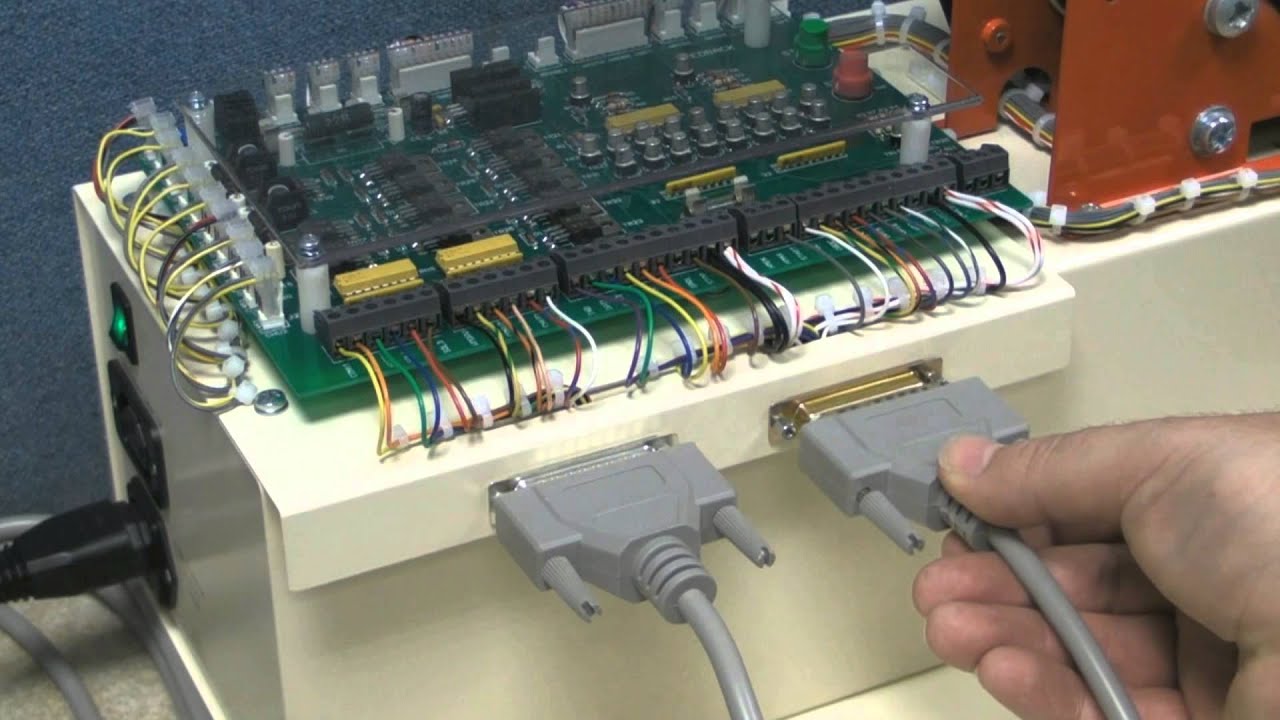
Programmable Logic Controllers, commonly known as PLCs, have revolutionized industrial control and automation. PLCs allow for flexible and customizable control of machinery and processes through computer programming rather than traditional electromechanical relays, switches and timers. This article explores the history, working and applications of PLCs and how it has shaped modern industrial control systems.
History and evolution of PLCs
The first PLC was developed in 1969 by Dick Morley while working for Modicon (now Schneider Electric). It was designed to replace aging electromechanical relay-based controllers which were difficult to program and maintain. Morley's Programmable Logic Controller could be easily programmed to perform a wide range of control operations. This early PLC used relay logic instructions and ladder logic programming to control machines.
Through the 1970s and 1980s, PLC technology advanced rapidly with increased processing power, memory and programming capabilities. Newer PLCs came with user-friendly programming software and more versatile instruction sets allowing complex control programs. They also offered communication capabilities to connect with other devices. By the 1990s, PLCs incorporated features like onboard displays, data storage and modular expandability. Today's PLCs are highly advanced microprocessor-based systems with powerful processors, extensive I/O configurations and open industrial communication protocols. They can integrate with various field devices and industrial networks.
Working principle of PLCs
A basic PLC system consists of a processor module, communication ports, power supply, and input/output modules. The processor module acts as the 'brain' which executes user-programmed software instructions. It scans input modules to monitor the state of field devices like sensors, limit switches, etc. Based on the programmed logic, it energizes or de-energizes appropriate output modules to control actuators like motors, valves, etc.
The user-program is written using ladder logic or other programming languages in a graphical form which resembles a circuit diagram. This program is then converted to machine code and loaded to the processor's memory for execution. During operation, the processor continuously scans the input image, executes the logic and updates the output image - forming the I/O scan loop. PLCs use removable I/O modules to connect with a wide variety of real world devices through standard protocols.
Applications of PLCs
PLCs are now integral to modern automation and control systems. Some common applications include:
- Machine tool control: CNC machine tools, presses, lathes use PLCs for coordinated motion control of multiple axes.
- Assembly lines: PLCs help automate assembly processes with accurate sequencing, tooling and part transfers.
- Packaging machinery: Used in packaging of foods, beverages, pharmaceuticals through labeling, capping, wrapping etc.
- Process control: Critical in process industries like chemical, oil & gas, water treatment etc. for controlling temperature, pressure, flow etc.
- Material handling: Enables sequencing of conveyors, lifts, robots etc. in production plants, warehouses, harbors.
- Manufacturing cells: Helps integrate individual machines into automated work cells for non-stop production.
- Building automation: Manages HVAC, lighting, access control, monitoring in buildings through integrated control.
Advantages of using PLCs
Adaptable to any control application: With programming, a PLC can be configured to control almost any real world process.
Cost savings: PLC systems prove economical compared to hard-wired relay logic over long term. Programming changes don't require rewiring.
Flexibility: Easier to modify existing control logic or add new functions through software without hardware modifications.
Robust performance: Reliable operation for continuous control in harsh industrial environments. Immune to electrical noise.
Local/remote monitoring: Capable of storing data, communicating over fieldbus, sending alerts through HMIs, SCADA etc.
Modular expandability: New I/O modules can be added without changing the control program as application needs change.
Standardization: Open communication protocols ensure interoperability of PLCs from different manufacturers.
Ease of programming: Graphical development environments simplify logic programming for engineers of any skill level.
Impact of PLCs on modern manufacturing
PLCs have transformed industrial control and played a vital role in the evolution of modern automated manufacturing. They allow for consistent and repeatable process control to achieve higher yields, quality and throughputs. PLC-based systems facilitate non-stop flexible production through easy reprogramming as product variants and processes change. The capability to integrate with other industrial devices through open standards has led to fully automated smart factories. PLC technologies enable data collection across systems for predictive maintenance, quality monitoring and Industry 4.0 applications. Their robustness and scalability address automation needs from small to large industrial facilities and sectors. PLC programming education has empowered individuals with new technical skills. Undoubtedly, widespread adoption of PLCs in manufacturing has driven operational excellence and global industrial growth.
Programmable Logic Controllers were an invention ahead of its time and have had far reaching impacts everywhere automation is applied. From their early beginnings as hard-wired logic panels, PLCs now integrate the physical and digital industrial worlds. Continuous technological advances are expanding their applications in newer smart technologies for Industry 4.0 initiatives. Going forward, we can expect PLCs to play a major role in industrial internet of things platforms, predictive maintenance through data analytics and even autonomous systems. Their success truly represents a revolution in control system design enabled by computer programming principles. PLCs will remain at the core of modern industrial processes for a long time, helping drive productivity and efficient operations across worldwide manufacturing.
Get more insights, On Programmable Logic Controller