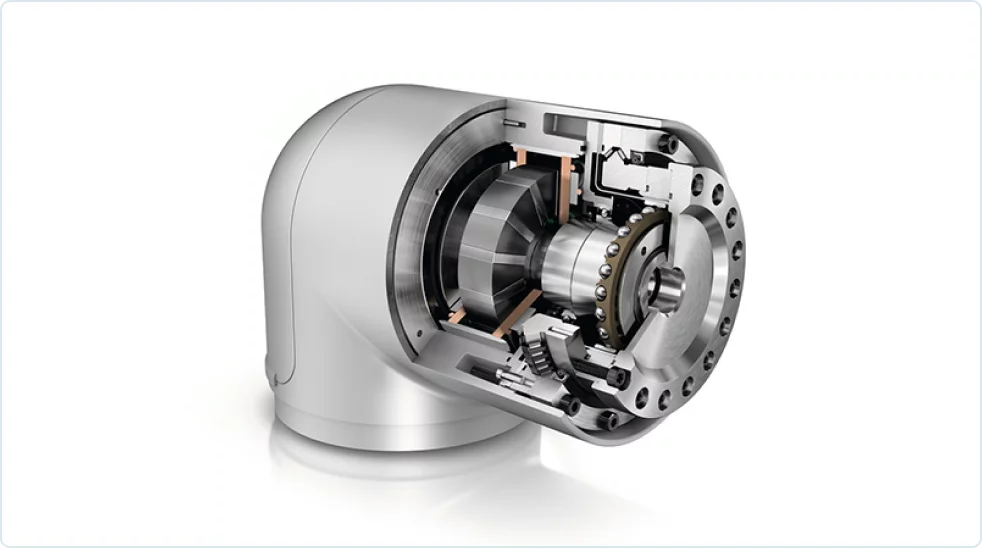
Movements for Robotics involve Linear, joint, and circular motions. Robotic systems are a complex arrangement of moving components all pivoting, moving and turning on bearings. Mechatronic robots that use the linear axis for movement are called Cartesian robots, linear robots, or gantry robots. Gantry robots look similar to gantry cranes but can be designed with customized functionality to perform more than just lifting and moving.
As robots have become a standard for factory production the utility for robotics is endless. Customized grippers and attachment arms all using bearings reveal the powerful adaptation for collaborative robotics. Robot movements need to be smooth, quick, and safe and so the need for precision bearings is a necessity.
Pacific International Bearing Sales Inc is a proven resource for robotic bearings. In this article we give insight on different robot bearing types and robot bearing applications. We offer you the opportunity to buy bearings for prototype robot development by going to www.pibsales.com.
In essence all rolling bearings including Roller and Ball encompassing linear and radial ball, spherical, cylindrical, needle and tapered roller bearings can and are used in robotic applications. By understanding the different bearing types and part numbering systems, engineers and designers can make informed bearing selection decisions.
Bearings used in Robot Joint Movement
Bearings used in robot joint movement must be able to pivot, oscillate and rotate. Robot joint bearings are essential in providing smooth effortless movements and operate in any environment without failure. In general a number of bearing types can be considered for joint movement. Here are just a few suggestions. Spherical Plain bearings offer misalignment features, oscillating and pivoting angles and are often specified for robotic joints. Buy Spherical plain bearings.
Another good bearing to consider for robotic joints are Self aligning ball bearings which offer a self aligning feature sometimes needed for this application. Buy robotic self aligning bearings.
Kaydon Thin Section bearings are often used in joints due to their narrow cross section and low mass and weight. Buy Kaydon Robot thin section bearings.
By no means are these the only bearing types for robotic joints and so you can determine more by understanding the envelope, environmental,and other operating constraints present in your application before rendering a bearing solution. If you need assistance in selecting bearings for your specific robotic arm joint application please contact us at [email protected].
Bearings used in Robot Linear Movement
A Linear bearing solution in robotic applications is one that moves in a straight path from its current position to the next position. As an example Linear bearings are often used in robotic welders where a controlled linear motion is required. Linear movement in robotics are listed in mm/second, whereas joint movements are shown as a % of maximum speed.
Careful selection of Linear bearings is essential to achieve smooth, precise, and efficient linear movement. Linear motion can be accomplished using ball bearings sometimes referred to as ball bushings or linear motion rolling guides. Linear rolling guides range from 1mm to 85mm in rail size. Linear rolling guides may employ rollers or balls as the rolling element. Linear rails with cartridges are available in miniature, cross roller type, U shaped track rail, high rigidity type and various precision versions.
Linear Ball Bearings or Bushings
Linear ball bearings utilize recirculating balls to facilitate low-friction movement along a linear track. They are specified for their smooth operation, high precision, and versatility, making them a popular selection for robotic applications.
- NB SM12GUU widely used linear ball bearing offers a balance of load capacity, precision, and cost-effectiveness. It is available in various configurations, including open, closed, and flanged types.
- INA LME16UU is another popular choice, this bearing provides similar features to the THK LM16UU and is suitable for a wide range of robotic applications.
- SKF LDCR12D ball bushing bearing is designed for higher load capacities and rigidity, making it suitable for demanding robotic applications.
- IKO LMS4 is a miniature linear ball bearing that is ideal for applications where space is limited, such as in small robotic manipulators or grippers.
Benefits for robotic applications
- The rolling motion of the balls minimizes friction, resulting in smooth and efficient movement.
- Precisely manufactured raceways and balls ensure accurate and repeatable linear motion.
- Available in various sizes, configurations, and load capacities to suit diverse robotic needs.
Buy Linear Ball Bushing Bearings.
Linear Rail Guides and Cartridges
Pacific International Bearing Sales inc offers various quality brands like NB, IKO, INA for standard and heavy duty applications. For light, medium and standard duty we offer CPC and BSQ which can be viewed at https://pibsales.com/bearing-manufacturers/bsq-linear/.
INA linear ball bearing and guideway assemblies represent the most extensive and complex group within the range of monorail guidance systems. They are used where linear guidance systems with high load-carrying capacity and rigidity must move heavy loads with high running and positional accuracy as well as low friction. The INA guidance systems are preloaded and are suitable for long, unlimited stroke lengths.
Linear Rail Guides and Cartridges
Depending on the operating conditions, acceleration values up to 150 m/s2 and speeds up to 360 m/minute are possible. A standard INA guidance system comprises at least one carriage with rolling elements, a guideway and one or two-piece plastic or brass closing plugs.
As previously stated, when a linear move is instructed to the robot, it will move in a straight line from its first position to the final position. All the joints will rotate as needed to ensure the total control point stays on path and with a consistent location.
If there is any negative for linear operation is that it is slower than joint moves. When the robot is moving in a straight line some joints need to move more than others in order to keep the robot on that path, therefore overall results are slower.
If your design is strictly for linear moves, the motion will be predictable and may sacrifice cycle speed and efficiency. By carefully evaluating these factors and understanding the specific features and benefits of different linear ball and roller bearing series, you can make informed decisions to ensure smooth, precise, and efficient linear motion in your robotic applications.
Bearings used in Robot ARC (Circular) Joint Movement
In certain robotic applications it is necessary for a consistent circular or arc motion. Pacific International offers standard off the shelf bearing products to accomplish this movement. Contact us to purchase the NB brand Curved Roller Guide at [email protected].
The NB GONIO WAY is a curved crossed roller slide bearing. It is a curved motion bearing utilizing low-friction, non-recirculating precision rollers. It is used when there is a need to change the gradient or obtain an accurate gradient angle without changing the center of rotation in high-precision optical and measurement equipment.
Welding robots use this move frequently as the robot moves around the circle the (TCP) the total control point orientation doesn’t change making for a smooth circle. To make a complete circle four points are needed from the starting of the circle; first midpoint, first endpoint, second midpoint, and back to the start point. In some designs this may be a combination of two separate arcs where the points along the radius must be carefully measured. Others allow this motion to be done with only three points along the radius, much like a 3-point circle in CAD sketches.
You do not need to always make a complete circle, as this move can be used to direct the robot in a radius or arc with a finite endpoint. The placement of these points is important for the accuracy of the path. The midpoint should be roughly halfway from the starting position to the end of the arc, since a point taught too close to one of the endpoints may require the robot to travel outside of its allowable work envelope when the entire arc is extrapolated.
Where linear and rotational joint movements are fundamental to robotics, some robotic applications require robots to move along curved paths. Bearings designed specifically for arc movement facilitate smooth and precise curvilinear motion, enabling robots to perform tasks with greater dexterity and flexibility.
Structure and Advantages of the NB Curved Crossed Roller Guide.
The NB GONIO WAY RVF type consists of curved tracking bases with precisely ground V-grooves and flat installation surfaces, as well as curved roller cages.
The NB GONIO WAY RV type consists of curved rails with precisely machined V-grooves and curved roller cages. Precision rollers are employed as the rolling elements, since the rolling elements do not recirculate, the frictional resistance will not vary significantly, providing curved movement with extremely low frictional resistance.
The NB Curved track bearings may be referred to as arc bearings or curved rail bearings. NB curved track bearings are designed to move along predefined curved tracks or rails. They typically utilize rolling elements, such as balls or rollers, to minimize friction and ensure smooth motion along the curved path.
Applications for NB Curved Cross Roller Guides are robotic painting and welding. Curved track bearings can be used in robots performing painting or welding tasks that require precise movement along curved surfaces.
Custom Bearing Solutions: Tailored Solutions for Complex Arcs
While standard curved track bearings are suitable for many applications, some robotic tasks involve complex arc movements that necessitate custom-designed bearing solutions. These custom bearings are engineered to meet the specific requirements of the application, ensuring optimal performance and longevity.
Examples of custom bearing solutions include:
- Curved roller bearings. These bearings utilize cylindrical or tapered rollers arranged in a curved raceway to accommodate high loads and complex arc movements.
- Spherical roller bearings with customized raceways. These bearings can be designed with raceways that conform to specific arc profiles, providing precise and robust motion.
Custom bearing solutions often involve collaboration between robot designers and bearing Distributors like Pacific International Bearing to develop bearings that meet the unique demands of the application. Part number designations for custom bearings are typically specific to the manufacturer and project.
Contact PIB Sales now and let us help you achieve the best possible results for your robotic applications.