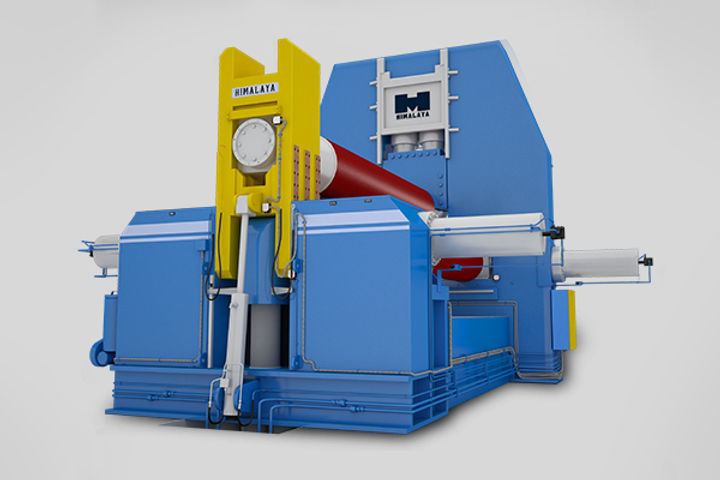
In the world of metal manufacturing, achieving precision and perfection in bending plates is an art form. Plate bending machines are the unsung heroes behind the flawless curves and shapes that define modern engineering marvels. Among the industry leaders in this domain is Himalaya Machinery, a renowned heavy engineering company based in India. Let's delve into the fascinating world of plate bending machines, exploring their types, applications, and how they elevate the craft of metal fabrication.
Understanding Plate Bending Machines
Plate bending machines, also known as roll benders or rolling machines, are pivotal in shaping metal plates with precision. These machines use force to bend metal sheets into desired curves or shapes. The ability to handle various thicknesses and materials makes them indispensable in industries like construction, shipbuilding, and aerospace.
Types of Plate Bending Machines
There are several types of plate bending machines, each catering to specific needs:
1. 3 Roll Bending Machines
These machines have three rolls—one at the top and two at the bottom—that perform the bending process. They are ideal for bending thinner sheets.
2. 4 Roller Bending Machines
Four roller bending machines, like those offered by Himalaya Machinery, a renowned heavy engineering company provide unparalleled precision. With two rolls positioned above and two below, these machines can handle thicker materials efficiently.
3. Hydraulic Plate Bending Machines
Utilizing hydraulic systems for power, these machines offer robust bending capabilities. They excel in applications requiring consistent and accurate bends.
The Mechanics Behind Hydraulic Plate Benders
Hydraulic plate bending machines leverage hydraulic cylinders to exert force on the rolls, ensuring smooth and controlled bending. The hydraulic system allows for precise adjustments, critical for achieving uniform bends across the length of a metal plate.
Advantages of 4 Roller Bending Machines
4 roll bending machines stand out for their versatility and efficiency:
- Improved Precision: The four-roll design minimizes material slippage, ensuring precise bending.
- Reduced Need for Pre-Bending: These machines often eliminate the need for pre-bending, saving time and material.
- Increased Throughput: They can handle larger volumes of work with consistent quality.
Applications in Metal Fabrication
Plate bending machines find extensive use in various industries:
- Architectural Metalwork: Creating curved metal structures like staircases and domes.
- Automotive Industry: Forming components for vehicles.
- Pressure Vessels: Rolling sheets for manufacturing pressure vessels and tanks.
- Heavy Equipment: Bending plates for machinery and equipment parts.
Choosing the Right Plate Bending Machine
Selecting the ideal plate bending machine depends on factors such as material thickness, bend radius, and production volume. Considerations like automation features and budget should also be factored in for long-term efficiency and ROI.
Operating a Plate Bending Machine
Operating a plate bending machine requires proper training and adherence to safety protocols. Operators must understand the machine's controls, loading procedures, and maintenance routines to ensure safe and efficient operation.
Maintenance Tips for Longevity
To maximize the lifespan of plate bending machines:
- Regular Lubrication: Keep moving parts well-lubricated to prevent wear and tear.
- Routine Inspections: Check for loose components and signs of damage regularly.
- Operator Training: Educate operators on best practices for machine usage and maintenance.
Innovations in Plate Bending Technology
Advancements in plate bending technology continue to revolutionize metal fabrication. From automated controls to predictive maintenance features, these innovations enhance efficiency and precision in bending operations.
Plate Bending Machines: Future Trends
The future of plate bending machines is poised for exciting developments:
- Smart Manufacturing Integration: IoT-enabled machines for real-time monitoring and data analytics.
- Material Flexibility: Machines capable of bending a wider range of materials.
- Green Technologies: Energy-efficient designs for sustainable manufacturing practices.
Conclusion
Plate bending machines are indispensable tools in modern metal fabrication, offering unparalleled precision and efficiency. Whether shaping sheets for architectural marvels or heavy equipment, these machines continue to push the boundaries of what's possible in metalworking.
FAQs (Frequently Asked Questions)
FAQ: How to Determine the Best Bending Machine?
To choose the right bending machine, assess your material requirements, production volume, and desired precision. Consult industry experts for tailored recommendations.
FAQ: What Safety Measures are Essential?
Safety is paramount when operating plate bending machines. Ensure operators wear appropriate PPE, conduct regular maintenance, and provide comprehensive training.
FAQ: Can Plate Bending Machines Handle Thick Materials?
Yes, hydraulic plate bending machines and 4 roll bending machines excel in handling thick materials, offering precise bends without compromising quality.
FAQ: Do Plate Bending Machines Require Skilled Operators?
Yes, operating plate bending machines requires trained operators familiar with machine controls, safety procedures, and maintenance routines.
FAQ: How Often Should a Machine be Serviced?
Routine servicing should be conducted according to manufacturer guidelines. Generally, a schedule of quarterly inspections with major maintenance annually is recommended.