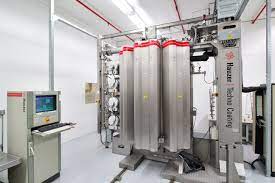
Physical Vapor Deposition: The Advanced Thin Film Deposition Technique
Introduction to PVD
Physical Vapor Deposition (PVD) is an advanced thin film deposition technique that is used to deposit thin films with a thickness ranging from a few nanometers to several micrometers. In PVD, the material to be deposited is initially heated to a gaseous form and then allowed to react or condense on the substrate or object that needs to be coated. The key processes involved in PVD include evaporation, sputtering, and cathodic arc deposition.
PVD vs CVD
PVD is different from Chemical Vapor Deposition (CVD) in the sense that in CVD, the deposition of thin films involves both chemical and physical reactions between the gaseous reactants whereas in PVD only physical processes like evaporation or sputtering are involved. CVD usually allows forming compound thin films by the reaction of two or more gases on a heated substrate. In contrast, PVD deposits thin film by directly transferring material from a solid target to the substrate.
Applications of PVD
PVD finds a wide range of applications due to its ability to deposit thin, hard, corrosion-resistant coatings with excellent adhesion to the substrate. Some common applications of PVD coating include:
- Cutting tools: PVD is used to deposit wear-resistant coatings like titanium nitride, chromium nitride on cutting tools to improve performance.
- Medical implants: PVD coatings of titanium, titanium nitride, etc. improves biocompatibility and corrosion resistance of implants.
- Data storage: Films like titanium, aluminium, niobium are used in magnetic hard disks for better interface properties.
- Decorative coatings: PVD process can deposit thin films of various colors on objects to make them look shiny and aesthetically appealing.
- Solar panels: Anti-reflective coatings of silicon oxide, titanium dioxide improve light absorption in panels.
- Consumer goods: PVD coatings provide scratch resistance and durability to products like watches, jewelry, eyeglasses.
Working Principle of Physical Vapor Deposition
The basic working principle involved in PVD includes the following steps:
- Feedstock Material: The pure material that needs to be deposited in thin film form is taken as the feedstock. It is usually in the form of a solid metal target.
- Vacuum Chamber: The substrate on which the coating is to be deposited and the target material are placed inside a vacuum chamber which is then evacuated to produce a high or ultra-high vacuum.
- Target Sputtering/Evaporation: The target material is either physically sputtered/ejected by bombardment of energized gas ions or evaporated by heating it to a very high temperature depending on the PVD technique used.
- Film Deposition: The ejected atoms from the target travel through the vacuum and deposit as a thin film on all surfaces including the desired substrate, present in the path of the vapor flux.
- Film Growth: With continuous bombardment/ejection of atoms from the target, the deposited film starts growing uniformly on the substrate forming a thin even coating of thickness up to a few microns.
- Process Variables: Variables like vacuum level, substrate temperature, discharge power/voltage determine properties of the growing film. Process is usually computer controlled.
Main PVD Techniques
Some major PVD techniques that are used for thin film deposition include:
- Sputter Deposition: One of the most widely used methods which involves sputtering/ejection of target material atoms by bombarding it with energized gas ions inside a vacuum chamber. Can be used to deposit conductive as well as nonconductive films.
- Evaporation Deposition: Involves heating the source material in vacuum either by electron beam, resistance or inductive heating so that it undergoes thermal evaporation/sublimation and gets deposited on nearby surfaces. Commonly used for depositing metals.
- Cathodic Arc Deposition: High power electrical arc discharge vaporizes small amounts of target material which is then deposited. Offers higher deposition rates for producing thick coatings but involves macro-particle issues.
- Pulsed Laser Deposition: A high power laser beam is used to vaporize material from a solid target which then deposits as a thin film. Used for producing complex oxide, superconducting thin films with stoichiometry matching with the target.
Advantages and Limitations
PVD offers several advantages over traditional metal coating techniques like plating due to its ability to precisely engineer thin films down to the nanometer level. However, it also has certain limitations some of which are:
Advantages:
- Uniform and very thin coatings
- Excellent adhesion to the substrate
- Precise control over film properties and composition
- Environment-friendly and suitable for reactive metals
- Applicable for both conductive and non-conductive materials
Limitations:
- Initial setup and equipment costs are higher
- Throughput is comparatively less for large volume applications
- Often requires post-deposition annealing/processing for many materials
- Film properties dependent on process parameters
- Industry 4.0 and automation scope remains to be fully realized
In conclusion, Physical Vapor Deposition has emerged as an advanced thin film deposition technique for high-performance, functional and decorative coatings which is gaining widespread applications across industries owing to its ability to engineer material properties with precision at the micro and nanometer levels. Further developments in PVD technology and integration with Industry 4.0 are expected to enhance its utilization potential for newer applications.