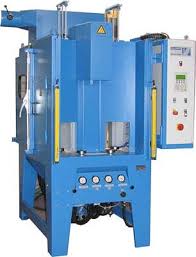
There is a convenient way to differentiate most Sandblast Abrasives normally used for blast cleaning. From one outlook, there are ecological abrasives that should be greater in expenses and utilization in inside production line environments. Then again, there are throw away abrasives that will be, in generals, affordable, engineered minerals and utilized in outside environments.
When it is the matter of creating a choice between abrasives then there are some crucial factors to keep in mind before settling down on a particular decision.
Factors to consider for abrasives selection
Hardness
One technique for differentiating whether abrasives are prominent for a specific cleaning process is to take a gander at their relative hardness according to the Mohs’ scale for non-metallic abrasives and Rockwell scale for metallic abrasives. The greater size of the rigidity go for the metallic abrasives mirrors the method that they can be heat treated in the stir of casting to modify their stiffness.
Specific Gravity
Another method that has to count for making a choice is particular gravity. Cleaning effectively based on the energy affected by the abrasives to the surface of the substrate. This is the reason because of the physical law of kinetic energy: E= ½ mv2. In this formula, v stands for velocity of the molecule, E derives energy and M is the mass of the rough molecule that is related to its specific gravity. Abrasives with the highest particular gravity achieve the quickest and productive cleaning.
Something can be made about velocity, the other things in the equation and the nozzle pressure that decides the velocity of the abrasives. Some of the abrasives will break an impact at the nozzle pressures above 100psi(7 bar) that usually generates a velocity of 450 mph1 (reliant on the measure of the nozzle and so on). At that point when abrasive breaks down, energy transmission is reduced. Pressures above 100 psi don’t add execution of the grating. The standard benefit of high pressures is the speed with such blasting should be possible.
Particle Size
One more crucial variable in abrasive selection is the size of the particle. The most efficient abrasive will be the best abrasive that will oust the covering and provide the required profile. If the abrasive is fine or excessively coarse, its ability is limited.
If possible, despite whether the abrasive is non-metallic or metallic, a blend of particle sizes provides the best performance and the good surface wrap up. Most recyclable abrasives are offered in a narrow range since the reusing technique will create the working blend. The purchaser should pick up the size range that won’t just abandon the covering at first by also has a decent size to add into a recycled blend to keep its efficiency. More abrasives that are used just once should be sold in working mixes.
Metallic or non- metallic?
Having that imagination about hardness, abrasive particle size as well as particular gravity, the following factor choice is either to use a non-metallic or metallic abrasive. Basically, the equipment should be purchased from the best Blasting Machine Manufacturer Malaysia.