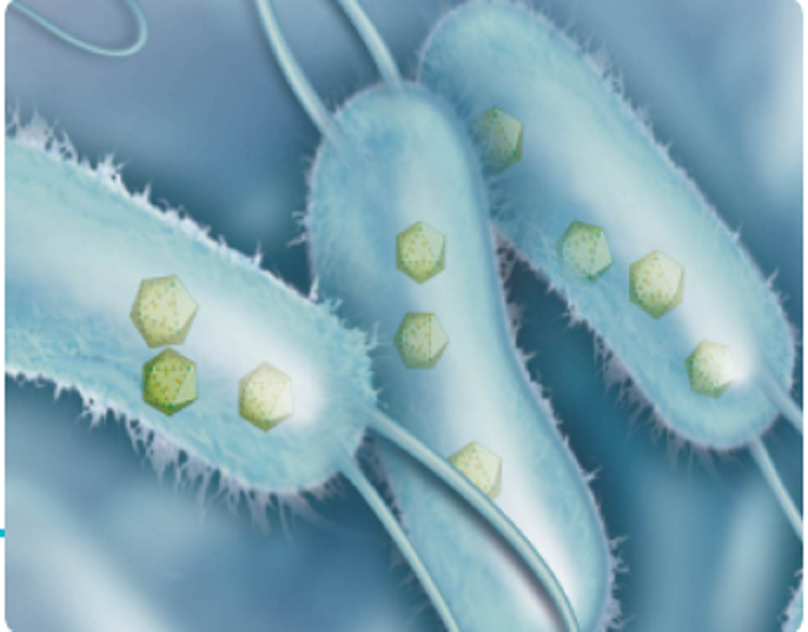
Pharmaceutical quality affects millions of households and individuals. Therefore the Food and Drug Administration (FDA) carried out the Current Good Manufacturing Practice (cGMP) regulations to assure the safety of human pharmaceuticals. Recently, the FDA conducted plentiful regulatory actions against drug manufacturers who fail to comply with the cGMPs, which largely aroused public concerns about quality control in pharmaceutical production.
As the revolutionary live biotherapeutic products (LBPs) gradually grow to be a hot spot in novel drug discovery, its manufacturing process is supposed to abide by the cGMP standards as well. Many LBP manufacturers such as Creative Biolabs (a leading biotechnology company) utilize facilities designed and operated according to the FDA standards. Besides, every stage of LBP manufacturing, from microbial fermentation to formulation, also follows the cGMPs to assure product quality. In the rest part of the passage, we would like to probe into the LBP cGMP manufacturing at Creative Biolabs, hopefully, which could enlighten your LBP development.
Microbial Fermentation
In comparison with conventional drug modalities, cGMP manufacture of engineered bacterial therapeutics encounters more obstacles due to the complexity of live bacteria. Therefore, how to design robust fermentation and downstream processes to produce individual commercial probiotic strains becomes a puzzle for technicians to crack. Creative Biolabs applied automated parallel bioreactor systems to accurately measure and control pH, dissolved oxygen, and temperature. Meanwhile, this system can automatically add nutrients and chemical inducers during the microbial fermentation. Owing to the totally instrumented microbial fermentation suite, batch-to-batch differences and contamination are avoidable.
Microbial Stabilization
There may be some impurities or other safety issues generated from the production process to the storage and delivery stage. Hence, a stability test proves to be essential to verify the expiration date of LBPs and their efficacy by exposing them to various conditions with changes in temperature, humidity, and UV light. Beyond that, Creative Biolabs would perform formulation and drying to make sure the products can maintain their properties and keep consistency when being transported to downstream manufacturers.
Microbial Formulation
Microbial formulation is necessarily a guarantee of quality, usability, competitiveness, and certainly compliance with cGMP guidelines. Currently, two formulation methods, known as lyophilization and microencapsulation, are in vogue among biotech companies. Freeze-drying (lyophilization) can preserve the viability and properties of LBPs to the maximum extent. The core elements for qualified lyophilization include first-class freeze dryers, optimized freeze-drying procedures, high-quality cryoprotectants, and proper storage conditions. Meanwhile, the microencapsulation technique is applied to encapsulate materials of various forms for the purpose of increasing their stability and life while it also controls their release within adequate time and space.
cGMP is such a demanding series of regulations that explicitly guide biotech companies through the complicated drug discovery process to ultimate fulfilments. As is demonstrated in the overall scope of operations at Creative Biolabs, LBP cGMP manufacturing can be eventually accomplished so long as the manufacturers act up to the detailed exacting requirements at each stage.