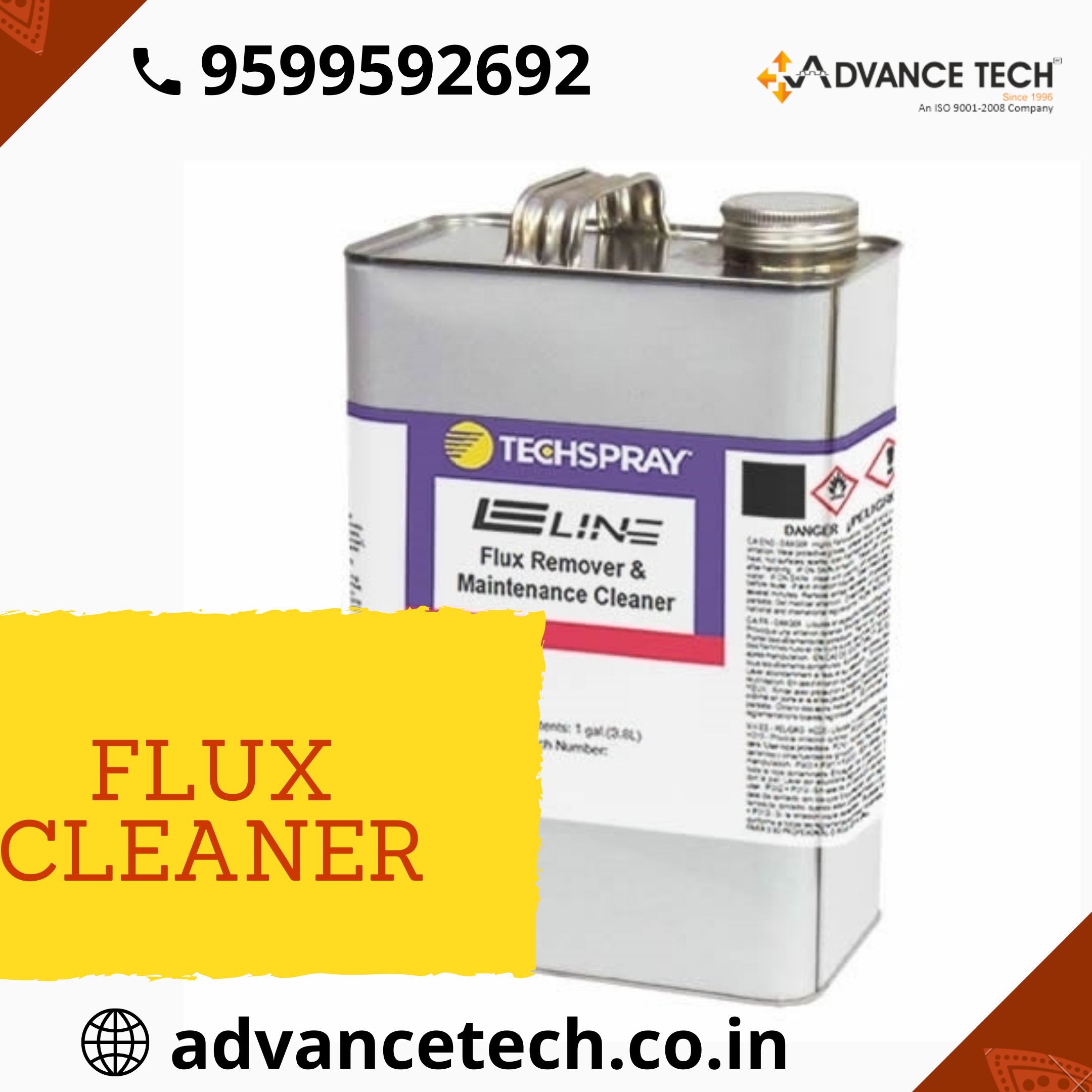
Flux Cleaner is now one of the most prominent fluxes to clean up in electronics production. Most manufacturers have actually designed as well as called in their production line to run no tidy paste. And, they only clean up the boards they want to clean, not always the boards they possibly need to cleanse. Additionally, the change residues left behind by no-clean pastes are more difficult to remove from PCBs than other fluxes. Since they are created not to be cleaned, the deposits from no clean products can be left on the board in undesirable areas with damaging results on the PCB. That develops a cleaning difficulty if you require to clean off a deposit that was not developed to be removed.
Flux Cleaner on the board relies on the quantity of solids in the product, the type of gelling representatives, and various activators in the flux. The changes in the majority of today's no clean pastes have up to 60 percent solids. The lower the total solids, the fewer deposits on the board. No cleans up, in theory, contain reduced complete solids so as not to require removal/cleaning. Complying with the reflow procedure, the change leaves a percentage of deposit around the various solder joints.
There are several factors to remove no clean change residues from PCBs. Historically, Flux Cleaner were developed as tacky materials which naturally covered and also stayed with all surfaces. The residue would gradually accumulate on the examination pins. Makers started cleaning no clean changes when troubles arise within-circuit screening. The current modern technologies of no cleans are boosted and also no longer tacky, yet still can interfere with signal transmission in a lot of instances.
Additionally, no clean changes can hinder correct adhesion of conformal layers. Flux Cleaner deposits can take in wetness in process. In any kind of further healing procedures, the launch of any type of moisture can trigger the finish to be divided from the board and an incomplete conformal bond can happen. This can allow corrosive materials, carbon dirt build-up, or wetness to permeate under the assembly as well as create rust, signal transmission problems, as well as component failure.