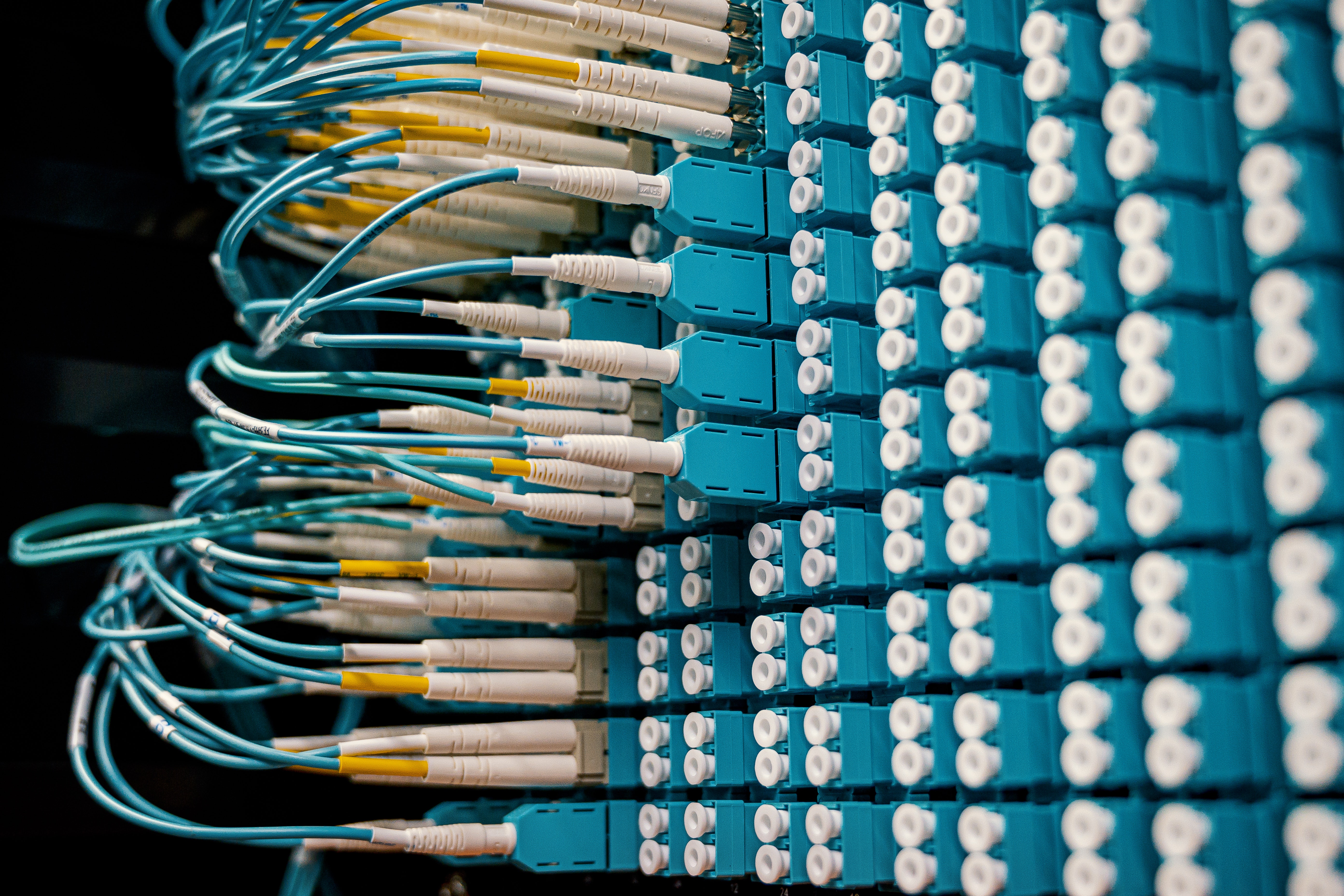
One of the challenges for a testing engineer when developing a sophisticated test system is that the testing equipment may need to measure several points via the mechanical interconnect. Here we take a look at different types of automated test fixtures in Tampa and their components.
Types Of Test Fixtures
There are three basic approaches to holding the printed circuit board (PCB) against the test probe: mechanical, pneumatic and vacuum.
In the mechanical approach, linkages, levers and mechanical cams are used to hold the probe plate and the product PCB together. A wide variety of arrangements can be used, differing in cost and complexity. Complex systems work by ensuring that the probe plate and the product are parallel during the operation. Simpler systems can also be found. They involve a pressure plate hinging over the PCB.
Pneumatic systems use pneumatics to press the area between the probe plate and the product together. The pneumatics may be placed on the top, bottom or both sides of the fixture.
The vacuum system works with the help of a sealed cavity between the product and the probe plate. They are pulled together when a vacuum is applied to the cavity.
Methods Of Establishing Contact
- Long Wire Fixtures
Long wire fixtures are an economical approach for testing PCBs with low probe count or prototypes that are subject to change because they avoid nonrecurring costs.
- Short Wire Fixtures
Although short wire fixture design is more difficult to change due to its wire density, it is useful because it offers better signal fidelity than the long wire counterpart.
- Wireless Fixtures
Wireless fixtures are considered more reliable than their wired counterparts because with them PCB designers can control the manner in which each trace is routed on the bottom side of the T-board and isolate undesirable signals. Other pros of wireless fixtures include:
- reduced debug time
- improved signal fidelity
- increased capability to test low voltage and multi-logic modules
- decreased signal crosstalk.
Types Of Probe Tips Based On Surface
- Leads
Serrateds are considered the most stable on long leads. Cups are used for extremely long leads but need more maintenance. Crowns can be standard (with valleys cutting straight across the point) or self-cleaning (valleys sloping down and out). Standard crowns are considered the more stable ones. Point styles with few tips or sharp internal geometry are best for short leads that are contaminated. Triad is one such point style. Tips with closely spaced cutting edges are required to trap smaller leads.
- Terminals and Posts
Serrated and flats are stable on this kind of contact but can do very little to penetrate contaminations. Self-cleaning crowns need little maintenance than cups when used in upward-pointing orientation but could glace off. Slotted cups are best for this orientation. Traditional cups are best used in horizontal or downward directions to avoid collecting dust and contamination.
- Pads
Chisels and sphericals are recommended for minimal markings on gold-plated pads. For clean flat solder pads, reduced crowns and triads are great because they distribute the force over a greater area and reduce the chances of marking the pad but they need frequent maintenance. To increase tip contact pressure for reliable testing of heavily oxidized or flux-coated solder pads, spear, sharp chisel, sharp needle or razor should be used.
- Holes or Vias
A chisel or star is the best when you need to contact open holes. When flux is present in open holes, chisel triads should be used. If you want the rim of the holes to remain free of marks, then use spears. The highest penetrating pressure is ensured through blades and razors because in them, contact is made on just two sharp cutting edges.
- Solder Beads/Bumps/Domes
When minimal witness marks are desired, flats are the best because they are the least aggressive. Micro-serrateds are more durable and ideal for points with light flux residues. Flat stars are great for boards that see high cycle counts. When sharp edges are needed and no-clean flux processes are involved, use a center point star.
These are some things to keep in mind when choosing a test fixture for a PCB, whether the PCB will be used in a security camera or a machine for crimping wires in Tampa.