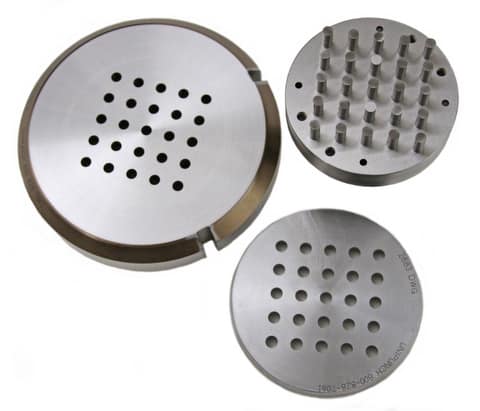
The Cluster tool processing provides semiconductor manufacturers with answers to some of the most pressing issues in complicated device production, namely, obtaining high device yields at a low cost.
Clustered architecture offers features such as integrated processing, reduced particulates, improved wafer to wafer consistency, and precise control over each wafer, good small batch economics, and the flexibility to expand easily. Let’s discuss about cluster tooling in detail.
Cluster Tooling Technology
The cluster tooling system automates the transport of a substrate between process chambers so that several layers may be deposited using diverse procedures. To increase throughput and productivity, the device may process many substrates in simultaneously. Typical setups include a load lock chamber for loading substrates, a transfer chamber, and several process chambers that can execute one or more operations.
To prevent exposure to air and thereby oxidation and contamination, the substrates are transported between chambers using a robotic arm in a vacuum. The cluster tooling is designed and manufactured by CVD Equipment Corporation to fulfil your process and throughput needs. A central control and safety system connects all the chambers.
Advantages of cluster tooling for implementing equipment applications
- The ability to evolve processes and equipment to satisfy more challenging device requirements has been demonstrated by cluster tooling architecture. Process modules may be created for new applications and then put on an existing platform for a fraction of the expense of creating a whole new tool.
- Platform improvements necessary for new process applications may be readily transferred to old process applications, generally without any application-specific re-design, and platform improvements required for new process applications can be quickly transferred to existing process applications.
- Clustering encourages application synergy; for example, numerous features developed for a new Metal Etch Strip application were simply ported to other processes on the cluster, allowing several processes to benefit from development work done on a single process.
- This intrinsic flexibility allows the equipment maker to produce a tool that can evolve to suit the changing demands of the user; a tool with a longer life cycle, which can save the semiconductor manufacturer money on capital equipment.
Benefits of Cluster tooling for integrated flattening
You may smooth out unevenness in the sheet during the punching process with the cluster tooling for integrated flattening and the associated machine function. Produce perforated sheets that are flat without the need for post-processing. The feature improves the component quality significantly, especially for workpieces with a high degree of punching.
Optimal part quality
Without post-processing, cluster tooling ensures distortion-free work-pieces.
Considerable time savings
Due to the fact that punching and flattening are done in the same process, it is significantly quicker.
Flattening formed sheet parts
The cluster tooling may flatten work-pieces with shaped portions as well.
Individual flattening
With cluster tooling, the degree of flattening may be modified individually at the machine.
Conclusion
Cluster tooling come in a variety of hole sizes, shapes, and patterns, ranging from 2 to 120 holes per punch. When retooling a punch, you may choose between a solid or removable tip, which allows you to replace the entire punch and only the tip.