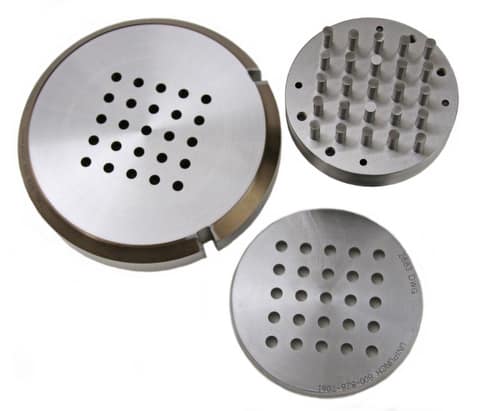
Cluster tooling can be used to save money on sheet metal work by reducing CNC punching time for many holes. The tool can include a large number of separate punches, allowing for the punching of thousands of holes each minute. When perforated features like ventilation regions, speaker grilles, LED panels, or light fittings are being manufactured, these CNC tools can be especially useful.
Cluster tooling is becoming more ubiquitous in semiconductor fabrication, and they're important parts of fab automation. Greater levels of automation are required as chips get more complicated in order to reduce costs, enhance productivity, and improve process dependability and product quality.
When retooling a punch, you can choose between a solid or removable tip, which allows you to replace the entire punch and only the tip. If oil canning is an issue, a back-bending die feature can help reduce distortion. In this article, we discuss the different application of cluster tooling and its design.
Design
A number of process/cleaning/cooling rooms, two chambers for loading and unloading, and a central robot for transferring wafers between chambers are all included in all semiconductor cluster tools. Integrated processing, reduced particulates, increased wafer to wafer uniformity, precise control over each wafer, good small batch economics, and the flexibility to grow easily are all advantages of clustered architecture.
These three component groups are for reference only and may differ from one another. Loading and unloading chambers, for example, are often load locks, which are similar to airlocks in that they are environmentally isolated wafer handlers. There could be as few as two or as many as eight or more process chambers, as well as one or more robots, depending on the system's intended application.
The image of a vapor deposition system at right shows a basic cluster tool design. This image divides each component into three categories: handling, deposition, and processing. Cluster tooling provides a number of special improvements to chip manufacture by grouping many operations around a single automated handler:
• Short cycle durations
• Rapid process development
• Increased yield efficiency
• Reduced contamination risk
Applications of Cluster Tooling
- Cluster tools are capable of punching many holes in a single stroke. Depending on the purpose and requirements, they are made individually on demand with interchangeable punch inserts or from a single piece.
- In perforation applications, the cluster tooling allows you to make the most holes with the fewest strikes while reducing sheet distortion. It's perfect for applications that require punching many holes in a pattern with tight center-to-center tolerances. The innovative design of the Cluster Tool aids in the management of perforation difficulties such as quick tool wear, hole distortion, and sheet strain.
- Cluster tools' maximum outer circular dimension of 72 mm and the machine's punching force are the sole factors restricting productivity. During serial manufacturing of perforated sheets employing cluster tools in continuous operation, the machine and tool are subjected to exceptionally high demands. Cluster punches come in a variety of hole sizes, shapes, and patterns, ranging from 2 to 120 holes per punch.
- Only use cluster tools in continuous operation at up to two-thirds of the maximum punching force, with tool shape adjusted as needed. These activities alleviate the machine and significantly extend the tool's service life. Cluster tools can be utilized without restriction in short-term operations.
Cluster Tool Technology
The cluster tool system enables the automatic transfer of a substrate between process chambers in order to deposit several layers utilizing various techniques. The device may also process numerous substrates in parallel to boost throughput and productivity. A load lock chamber for loading substrates, a transfer chamber, and numerous process chambers that can perform one or more processes are typical configurations.
The substrates are moved between chambers using a robotic arm in a vacuum to avoid exposure to air and thereby oxidation and contamination. With cluster tooling for integrated flattening and the associated machine function, you may smooth out unevenness in the sheet during the punching process. Produce flat perforated sheets without the use of additional post-processing steps.
Cluster tooling is designed and manufactured by Corporation to fulfil your process and throughput needs. A central control and safety system connects all of the chambers. The unique real-time instrument control, data logging, and process editing software suite, is used to program recipes and automate system control.
Cluster Tooling for Implementing Equipment Applications
- Cluster tooling design has proved the ability to develop processes and equipment to meet more complex device requirements. Process modules for new applications can be designed and then deployed on an existing platform for a fraction of the cost of developing a completely new tool.
- Platform improvements required for new process applications can be quickly transferred to existing process applications and platform improvements required for new process applications can be quickly transferred to existing process applications, generally without any application-specific re-design.
- Application synergy is encouraged by clustering; for example, several features developed for a new Metal Etch Strip application were simply moved to other processes on the cluster, allowing several processes to benefit from development work done on a single process.
- This inherent flexibility enables the equipment manufacturer to create a tool that can adapt to changing customer demands; a tool with a longer life cycle, which can save the semiconductor manufacturer money on capital equipment.
- Finally, the short-term scheduling model can provide easily and well controlled cluster tools for the shop floor management and control. The results strongly support the viability of the proposed model from various perspectives.
Conclusions
Cluster tooling can be used for multiple holes to reduce CNC punching time and save money on repeated batches of sheet metal work. Cluster tools are not only numerous in the fab, but also treated as an important process tools. They increase the difficulties in the shop floor management and control because of their complex structure.
A short-term scheduling model for cluster tools to arrange a better schedule under the goals and constraints is proposed at the heart of this study. Generally, quality and speed of the scheduling are the necessary characteristics for an on-site short term scheduling model.