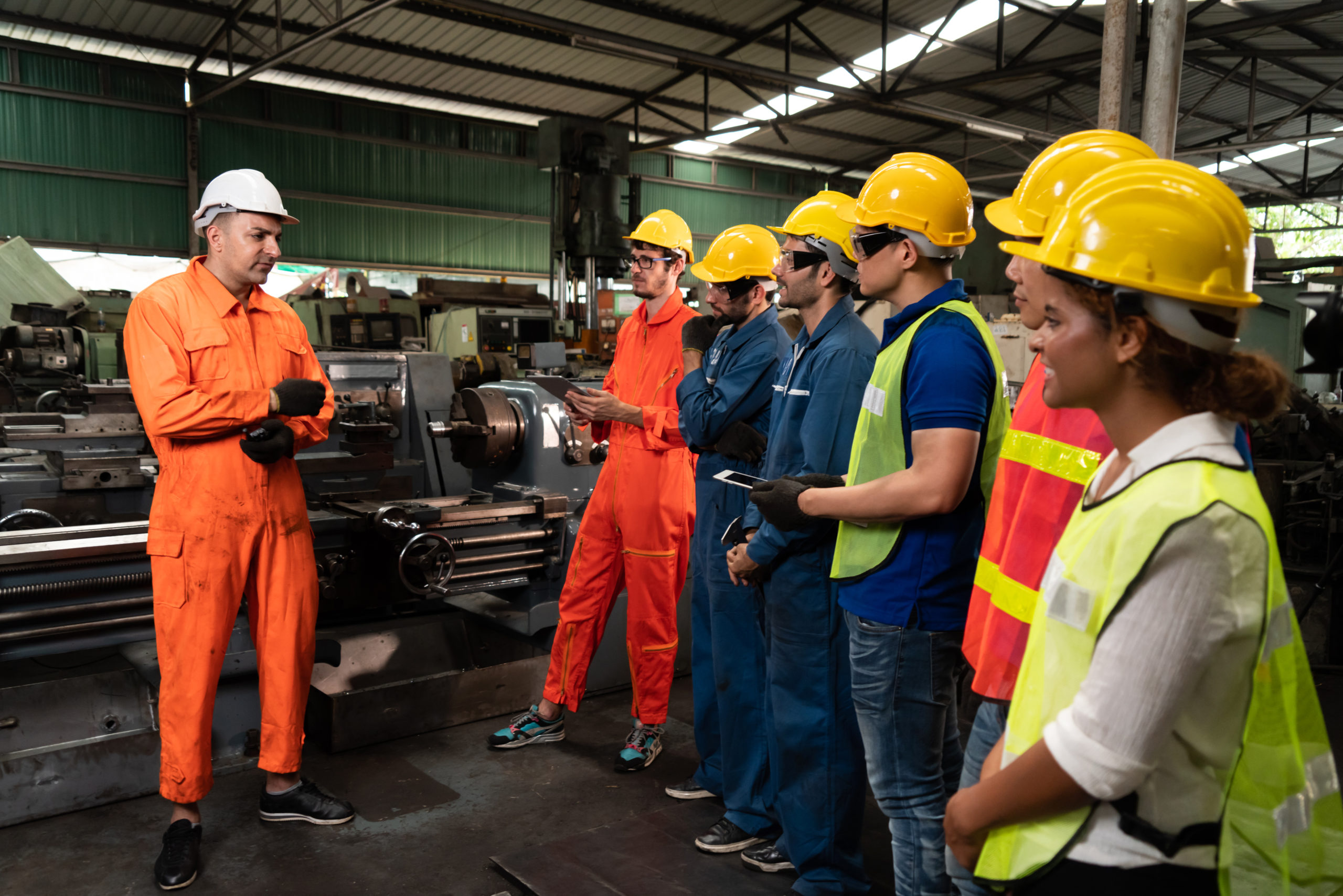
Injuries at work totalled more than 4.6 million in 2019, yet they may have prevented them. Every employee's mental toolbox should include these seven safety tools. Employees can prevent work-related injuries and deaths for themselves and others by following these safety rules every day.
Maintain a clean work environment.
Proper housekeeping can go a long way toward reducing injuries. Keeping work areas clean can avoid slips, trips, falls, lacerations, sprains, strains, and other injuries. Employees should always check their work area before starting or leaving their shift to ensure it is clean and ready for them or the following employee to begin work safety training.
Make use of the appropriate tool for the job.
It is significant! Using the wrong tool for the operation can damage the tool, even if there are no injuries. Avoid the first impulse to use whatever tool is available to complete a work task.
Always put on the appropriate PPE for the job.
Every year, many industrial injuries are caused by improper PPE or lack thereof. Personal protective equipment, or PPE, is the final line of defence when shielding workers from workplace dangers. The injury will be more severe if you come into touch with a hazard while not wearing the proper PPE than if you were. Although wearing a hard helmet may bother or even be uncomfortable, it protects the head from falling items that can cause deadly or severe head injuries. Always be aware of the PPE needed for the task, how to wear it properly, and where to store it after use. Always ensure PPE is in excellent condition before using it, and notify a supervisor if it isn't.
Never perform maintenance on live equipment.
Electrical, mechanical, hydraulic, pneumatic, chemical, thermal, and other energy sources in machines and equipment can be hazardous to workers. Workers risk suffering significant injuries or being hurt by an unexpected start or release of stored energy when doing repairs and maintenance on machinery and equipment. Understanding and adhering to proper lockout/tag-out endure critically. Lockout refers to installing a lock on a device that prevents energy release. Tagout refers to attaching a tag to a switch or shut-off device to warn users not to start the equipment. Always follow the proper lockout/tag-out procedures before servicing or repairing equipment.
Ascertain that chemicals are properly labelled and stored.
Every year, OSHA issues citations for hazard communication. Keeping chemical storage records helps prevent employees from inadvertently causing a chemical hazard. Injuries or property loss can result from improper labelling and storage! Heat, fumes, gases, and vapours are produced when incompatible chemicals are stored together. All employees should know SDS, where they can be found, and how to use them properly.
Alert other staff members to safety risks.
Safety risks are unsafe working circumstances that might result in illness, injury, or death. This group comprises hazards for biology, physicality, ergonomics, chemicals, or work organisation. Never presume that a coworker knows the risks involved in a task or situation. Employees must take the necessary time to notify others when work schedules or circumstances change. It includes anything that could lead to falls, tripping, or slides, exposed moving machinery parts, electrical hazards, and cramped areas.
When necessary, halt work to address hazards.
Employees should always take breaks to address hazards and ensure that the task is safe to continue. Take the time to involve other personnel, such as a supervisor, or get the right tool for the job. Failure to stop working and address workplace hazards can result in serious fatalities.
.