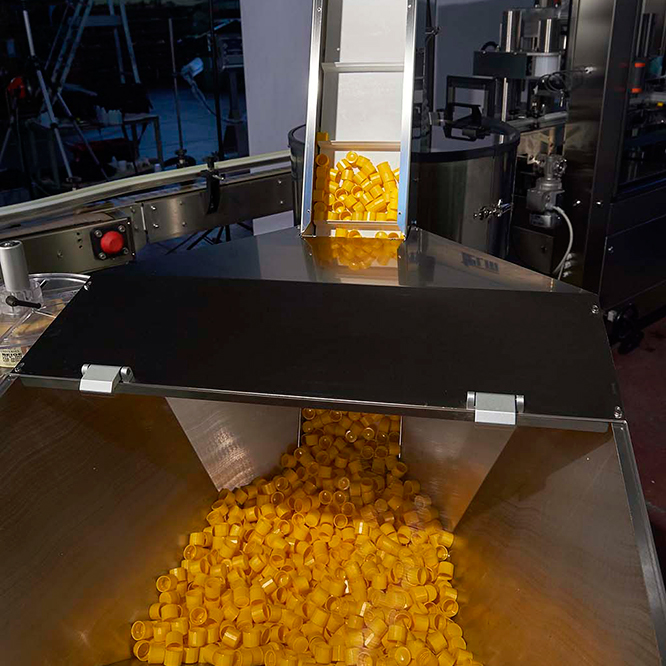
Manufacturers and dealers who are new to the world of packaging and automation often find themselves confused while looking for the best liquid filling machines available. While there are different types of equipment being used such as liquid volumetric dosers, liquid filling machines and more, simply choosing any won’t do. There are many factors that have to be taken under consideration by manufacturers such as overflow, gravity, pistons and pumps. That being said, here are some of the biggest factors for choosing a liquid filling machine.
1. Unique characteristics of products
Manufacturers must consider any unique product characteristics that they want to produce, as it has a direct bearing on which liquid filler suits most. For instance, some products can change viscosity as the temperature changes. There are some products which might contain particulates such as liquid soaps or salad dressing. In such cases, a piston filling machine might be more suitable to move chunks through the product pathway.
2. Type of container
In some instances, more than one machine may work well for a product. However, considering the bottle or container to be used is an important step. For instance, a client using a clear glass container may want to take advantage of the level filler, which provides an attractive presentation when displayed on shelves in a shop or supermarket. The size f the containers, either large or small can influence the machine or the nozzles that should be used.
3. Degree of automation
When using automatic liquid filling machines, it's important for the manufacturers to specify how many bottles they need to produce in a day, week or year. This information makes it easier to calculate the speed or capacity per minute/hour of the machine. The number of bottles per minute required to reach the desired production levels will also help manufacturers decide whether a manual, semi-automatic or fully automated packaging system is suited for the particular production process.
4. Level of integration
The new liquid filling machine should have the capabilities to integrate with existing manufacturing equipment or even future additions. This is crucial to prevent a situation where a manufacturer might get stuck with an obsolete machine. While semi-automatic and manual filling machines aren’t always easy to integrate, most automated liquid filling machines are designed to integrate seamlessly.
5. Level of accuracy
To ensure accuracy, the best solution is to use an automated filling machine. They come equipped with PLC that can control filling parameters which ensure consistent product flow and precise filling. It also prevents the overflowing of products which not only saves money but reduces time and expenses spent on cleaning.
Conclusion
Various types of liquid filling machines can ensure each bottle and container is filled with the same amount of product with minimal to no error. They help in distributing and packaging every product based on volume, weight, level or any other input measurements required. To ensure a quality work process, manufacturers should always acquire their liquid filling machines from certified and licensed companies only.