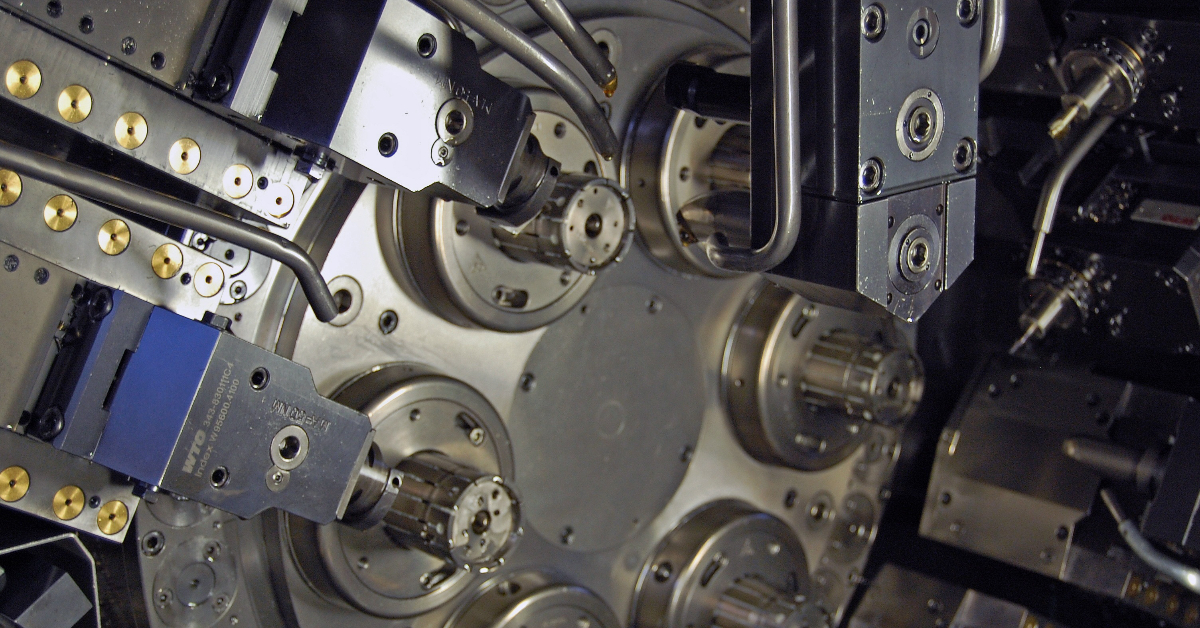
Aluminum is a versatile and widely used metal in manufacturing, particularly in custom machining parts. With desirable properties such as a high strength-to-weight ratio, corrosion resistance, and excellent machinability, aluminum alloys have become a popular material choice for various applications, including aerospace, automotive, and medical industries.
However, choosing the suitable aluminum alloy for custom machining parts can take time and effort due to the many options available.
Factors such as strength, durability, and cost must be considered to ensure that the selected alloy meets the project's specific needs.
In this article, we will explore the key considerations when selecting the appropriate aluminum alloy for custom machining parts and the benefits and drawbacks of various alloys commonly used in the industry.
Understanding Aluminum Alloys
Aluminum alloys are formed by mixing aluminum with other elements such as copper, zinc, magnesium, and silicon to create a material with desired properties. The process of mixing the different elements is known as alloying. Aluminum alloys have many benefits compared to pure aluminum, including increased strength, better corrosion resistance, and improved machinability.
The most common aluminum alloys used in custom machining parts manufacturing include are:
- 6061 Aluminum Alloy
- 7075 Aluminum Alloy
- 2024 Aluminum Alloy
- 6063 Aluminum Alloy
We’ll discuss them later in the article (while covering aluminum alloys for custom machining parts)
Factors to Consider When Choosing an Aluminum Alloy for Custom Machining Parts
When choosing the suitable aluminum alloy for custom machining parts, several factors must be considered to ensure that the selected alloy meets the application's specific requirements. The following are some of the critical factors to keep in mind:
Mechanical properties: The mechanical properties required for the specific application of the part, such as tensile strength, yield strength, and elongation, should be considered when selecting an aluminum alloy. The selected alloy must have sufficient strength to withstand the loads and stresses to which it will be subjected.
Corrosion resistance and durability: The part's corrosion resistance and durability requirements must also be considered when selecting an aluminum alloy. For example, if the part is exposed to harsh environments, such as marine or outdoor applications, an alloy with high corrosion resistance, such as 5083 or 6061, should be used.
Machinability: The machinability of the alloy is also an essential factor to consider, as it will affect the ease and speed of the machining process. Aluminum alloys with excellent machinabilities, such as 6061 and 2024, are preferred for custom machining parts manufacturing.
Availability and cost: The alloy's availability and cost should also be considered. The selected alloy must be readily available and affordable to ensure the project remains within budget and timeline.
Other factors to consider when selecting an aluminum alloy for custom machining parts include the alloy's welding and finishing properties and its ability to withstand high temperatures. Ultimately, the selected alloy should meet the application's specific requirements while being cost-effective and easily machinable.
Common Aluminum Alloys for Custom Machining Parts
There are several aluminum alloys commonly used in custom machining parts manufacturing. Here are some of the most widely used alloys and their properties:
6061 Aluminum Alloy: This is a popular alloy due to its high strength-to-weight ratio, excellent machinability, and corrosion resistance. It is commonly used in the aerospace, automotive, and consumer goods industries. It is also easily welded and easily anodized to provide a protective surface finish.
7075 Aluminum Alloy: This high-strength alloy is commonly used in high-stress applications, such as aerospace and defense. It has excellent machinability and corrosion resistance, making it ideal for manufacturing custom machining parts that require high strength and durability. However, it is difficult to weld and is more expensive than other aluminum alloys.
2024 Aluminum Alloy: This high-strength alloy is commonly used in aerospace and aircraft manufacturing due to its excellent fatigue resistance and good machinability. It is also used in high-performance bicycle frames and other consumer goods. It is easily welded but has poor corrosion resistance and is susceptible to stress corrosion cracking.
5083 Aluminum Alloy: This marine-grade alloy is commonly used in shipbuilding due to its excellent corrosion resistance and high strength. It is also used in structural components for bridges and other infrastructure projects. It is weldable but has poor machinability compared to other aluminum alloys.
6063 Aluminum Alloy: This alloy is commonly used in construction due to its excellent extrudability and weldability. It is used in window frames, curtain walls, and other architectural applications. It has good corrosion resistance but is less potent than other aluminum alloys.
Selecting the appropriate aluminum alloy for custom machining parts is critical to ensure that the final product meets the application's requirements. The most commonly used aluminum alloys include 6061, 7075, 2024, 5083, and 6063, each with unique properties and benefits suitable for specific applications.
Matching the Aluminum Alloy to the Application
To match the properties of the aluminum alloy to the specific application, it is essential to understand the requirements and demands of the application. As discussed earlier, factors such as mechanical properties, corrosion resistance, machinability, availability, and cost must be considered when selecting an aluminum alloy.
The following are some real-life examples of selecting the appropriate aluminum alloy for custom machining parts:
Aerospace Industry: The aerospace industry demands high-performance, durable parts that withstand extreme conditions. 7075 aluminum alloy is commonly used in this industry due to its high strength-to-weight ratio and excellent fatigue resistance. For example, 7075 aluminum alloy is used in aircraft landing gears, wing spars, and other structural components.
Marine Industry: The marine industry requires parts that can withstand harsh environments, such as saltwater corrosion. 5083 aluminum alloy is prevalent in this industry due to its excellent corrosion resistance and high strength. For example, 5083 aluminum alloy is used in boat hulls, propellers, and other marine components.
Automotive Industry: The automotive industry demands lightweight parts that withstand high stress and loads. 6061 aluminum alloy is commonly used in this industry due to its high strength-to-weight ratio and excellent machinability. For example, 6061 aluminum alloy is used in suspension components, engine blocks, and other automotive parts.
Consumer Goods Industry: The consumer goods industry demands aesthetically pleasing, durable, and lightweight parts. 2024 aluminum alloy is commonly used in this industry due to its excellent fatigue resistance and good machinability. For example, 2024 aluminum alloy is used in bicycle frames, sporting equipment, and other consumer goods.
Conclusion
In conclusion, choosing a suitable aluminum alloy is critical in custom machining parts manufacturing. Aluminum alloys offer unique properties that make them suitable for specific applications, such as high strength, corrosion resistance, and machinability.
Understanding the properties of different aluminum alloys and matching them to the application's requirements is essential to ensure the final product's quality and performance.
Factors such as mechanical properties, corrosion resistance, machinability, availability, and cost must be considered when selecting the appropriate alloy. Real-life examples show that the appropriate aluminum alloy can meet the unique requirements of each industry, providing lightweight, durable, and high-performance parts.
By selecting the suitable aluminum alloy for custom machining parts, manufacturers can create parts that meet the specific needs of their clients while ensuring a high-quality and cost-effective final product.