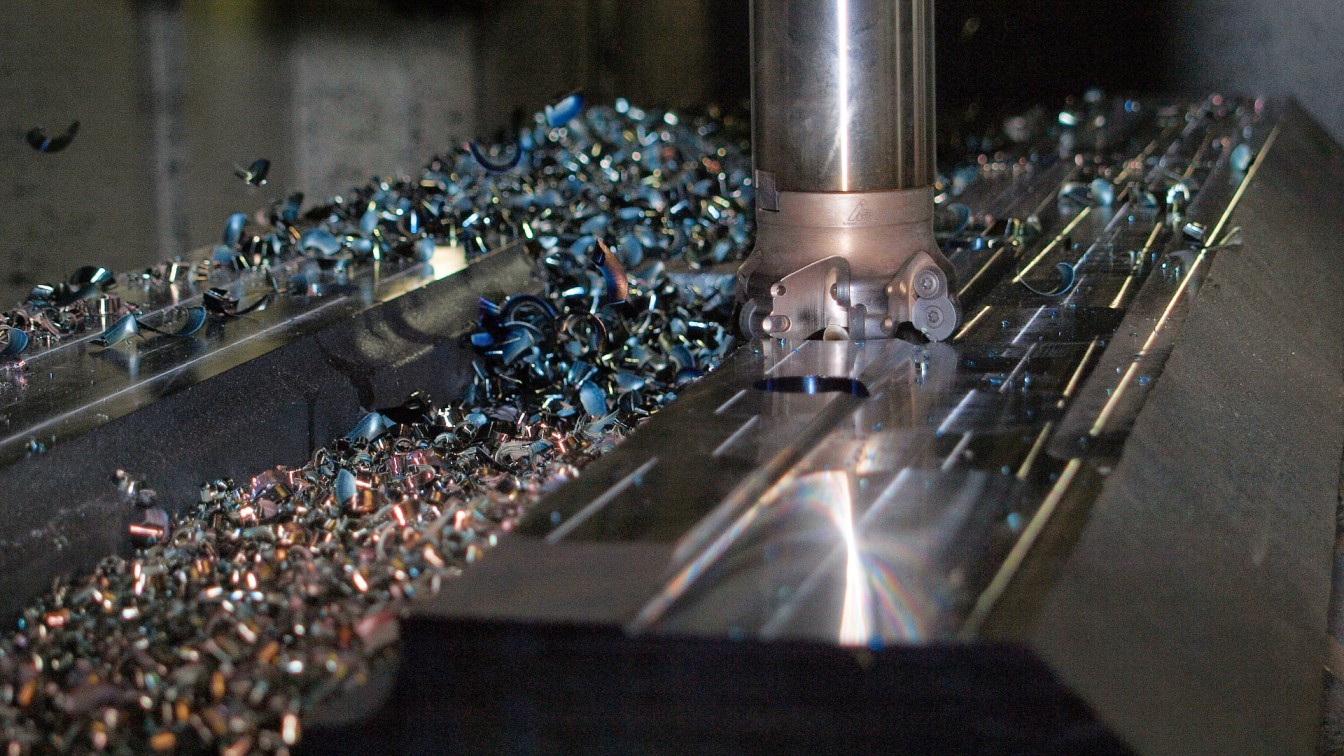
CNC custom machining has revolutionized prototyping and small-scale production, offering a host of advantages for businesses in these stages of product development. With its precise computer-controlled machinery and flexibility in creating intricate parts, CNC custom machining has transformed product development.
This blog explores the benefits of CNC custom machining, including streamlined design iterations, exceptional precision, flexibility in materials and geometries, cost-effectiveness, scalability, quality control, and real-world success stories.
Let’s lookout at the advantages of CNC custom machining for prototyping and small-scale production.
Streamlined Design Iterations
CNC custom machining facilitates rapid prototyping, converting digital designs into physical prototypes efficiently. The CNC machine executes precise machining operations based on the CAD model, resulting in accurate and high-quality prototypes. This expedites the prototyping process, enabling faster design iterations compared to traditional methods.
Design modifications can be swiftly implemented through reprogramming the CNC machine, leading to a shortened product development timeline. The accelerated iteration cycle reduces the time required to refine and perfect the design, resulting in a quicker time-to-market. This competitive advantage allows businesses to introduce their products faster.
Efficient design refinements achieved through CNC custom machining contribute to cost savings. Early identification and rectification of design flaws or improvements during prototyping prevent costly mistakes during large-scale production. CNC custom machining optimizes the design for functionality, manufacturability, and cost-effectiveness, resulting in significant savings in material costs, production time, and resources.
Precision and Accuracy
CNC custom machining facilitates rapid prototyping, converting digital designs into physical prototypes efficiently. The CNC machine executes precise machining operations based on the CAD model, resulting in accurate and high-quality prototypes. This expedites the prototyping process, enabling faster design iterations compared to traditional methods.
Design modifications can be swiftly implemented through reprogramming the CNC machine, leading to a shortened product development timeline. The accelerated iteration cycle reduces the time required to refine and perfect the design, resulting in a quicker time-to-market. This competitive advantage allows businesses to introduce their products faster.
Efficient design refinements achieved through CNC custom machining contribute to cost savings. Early identification and rectification of design flaws or improvements during prototyping prevent costly mistakes during large-scale production. CNC custom machining optimizes the design for functionality, manufacturability, and cost-effectiveness, resulting in significant savings in material costs, production time, and resources.
Flexibility in Materials and Geometries
CNC custom machining offers versatility in material selection, accommodating various options for different applications. It can work with metals like aluminum, steel, brass, and titanium, as well as plastics, composites, and certain types of wood. This wide material compatibility allows businesses to choose the most suitable material based on desired properties such as strength, durability, heat resistance, or electrical conductivity. CNC custom machining ensures precise machining of the chosen material into the desired shape and dimensions.
The precision of CNC custom machining enables the production of complex geometries and intricate designs that may be challenging with traditional methods. The CNC machine accurately follows intricate paths and contours defined by the CAD model, allowing for the creation of complex shapes, curves, undercuts, and fine details. This capability opens up opportunities for innovative and visually appealing designs. CNC custom machining is particularly well-suited for producing prototypes and small-scale production runs of parts with intricate or organic geometries, providing businesses with the freedom to explore unique and creative designs.
CNC custom machining facilitates the exploration of material and design options during prototyping and small-scale production. The wide range of materials that CNC machines can work with allows businesses to test and evaluate different material choices to determine the optimal one for their product's performance and aesthetics. Additionally, CNC custom machining enables easy iteration and refinement of designs, empowering businesses to explore different design concepts and assess their feasibility before committing to larger production volumes. This iterative process aids in design optimization, issue identification, and overall improvement of product quality.
Cost-Effectiveness
CNC custom machining offers cost advantages by eliminating the need for expensive tooling and molds typically required in traditional manufacturing. Custom CNC parts can be directly fabricated from the digital design, avoiding the upfront costs and lead time associated with tooling production. This saves businesses a significant amount of money, especially during the prototyping stage where multiple iterations and design changes occur.
In small-scale production runs, CNC custom machining reduces setup time and labor costs. Once programmed, the CNC machine can automatically carry out machining operations without manual intervention or extensive setup processes. This minimizes production time and labor, resulting in cost savings. Continuous operation of CNC machines optimizes labor resources and enhances productivity.
Efficient material utilization is another benefit of CNC custom machining, leading to reduced waste and cost savings. The precision and accuracy of CNC machines allow for optimal nesting and positioning of parts within the raw material, minimizing material waste. This is particularly advantageous when working with expensive materials or producing parts with complex geometries that would generate significant waste using traditional manufacturing methods. By maximizing material utilization, CNC custom machining helps businesses save on material costs and minimize their environmental impact.
Scalability and Production Efficiency
CNC custom machining enables a seamless transition from prototyping to small-scale production. The same digital design used for prototyping can be directly utilized for production, ensuring consistency and eliminating the need for redesigning or retooling. By replicating the machining process, CNC machines can produce larger quantities of parts without disruptions or delays, streamlining the production process and saving time and effort.
Scaling up production with CNC custom machining is efficient and cost-effective. Once set up and programmed, CNC machines can consistently produce parts with high quality and precision. As demand increases, businesses can adjust production volume by running the CNC machine for longer periods or employing multiple machines simultaneously. This scalability allows for efficient production ramp-up without the need for significant retooling or setting up new production processes, resulting in cost savings.
CNC custom machining enhances production efficiency through automation and optimized workflows. CNC machines operate with a high degree of automation, minimizing the need for manual intervention and reducing the potential for human errors. Once programmed, the CNC machine can run unattended, optimizing the utilization of labor resources. Integration of software tools further enhances efficiency by optimizing machining paths, reducing material waste, and improving production speed. These automated processes and optimized workflows streamline production, improve efficiency, and maximize output while minimizing costs.
Quality Control and Consistency
CNC custom machining achieves high precision and quality by maintaining tight tolerances. CNC machines follow programmed instructions with exceptional accuracy, resulting in consistent dimensions and specifications. This precision ensures that parts meet strict quality standards and customer requirements. Quality assurance processes, such as post-machining inspections and measurements, are often included in CNC custom machining to ensure the produced parts meet desired specifications.
Consistency is a key feature of CNC custom machining, providing uniform output across multiple prototypes and small-scale production batches. Once set up and programmed, CNC machines can reproduce identical parts with consistent accuracy and quality. This consistency is valuable for businesses requiring multiple prototypes or small-scale production runs manufactured with the same precision. Consistent output ensures that each part meets the desired specifications, maintains product integrity, and facilitates smooth assembly and functionality.
CNC custom machining enables businesses to achieve compliance with industry standards and specifications. CNC machines accurately produce parts according to specific design requirements, ensuring manufactured components meet necessary standards and specifications. This is particularly crucial in industries with stringent regulatory requirements, such as aerospace, medical devices, or automotive. By utilizing CNC custom machining, businesses can achieve the required levels of quality and compliance, ensuring their products meet industry standards.
Industrial Applications of CNC Custom Machining
CNC custom machining is widely used across various industries due to its versatility and precision. Some notable industrial applications for CNC custom machining include:
Aerospace and Aviation: CNC custom machining is employed in manufacturing critical components for the aerospace industry, such as turbine blades, engine parts, brackets, and structural components. The high precision and accuracy of CNC machining ensure compliance with stringent aerospace standards, contributing to the safety and reliability of aircraft.
Automotive: CNC custom machining finds extensive use in the automotive industry for producing engine components, transmission parts, chassis components, and intricate interior and exterior components. CNC machining enables the production of complex geometries and high-precision parts required for automotive systems.
Medical and Healthcare: CNC custom machining plays a vital role in the medical and healthcare sector, where precision and quality are crucial. It is utilized for manufacturing surgical instruments, prosthetics, orthopedic implants, dental components, and medical device parts. CNC machining ensures the necessary accuracy, surface finish, and biocompatibility required in medical applications.
Defense and Military: CNC custom machining is integral to the defense and military sector for the production of specialized components, weapon systems, armored vehicle parts, and aircraft components. The high precision and consistency of CNC machining contribute to the reliability and performance of defense equipment.
Conclusion
In conclusion, CNC custom machining offers a range of advantages for prototyping and small-scale production. It enables rapid prototyping, faster design iterations, and cost savings through efficient design refinements.
The technology ensures high precision, consistency, and minimizes errors and material waste. CNC custom machining provides flexibility in materials and geometries, allowing for exploration of various options.
It is a cost-effective solution, eliminating the need for costly tooling and molds, reducing setup time and labor costs, and promoting efficient material utilization. Additionally, CNC custom machining enables scalability and production efficiency through automation and optimized workflows.
It ensures quality control and compliance with industry standards. By leveraging CNC custom machining with the help of a custom machine shop, businesses can optimize their product development journey and achieve success in prototyping and small-scale production.