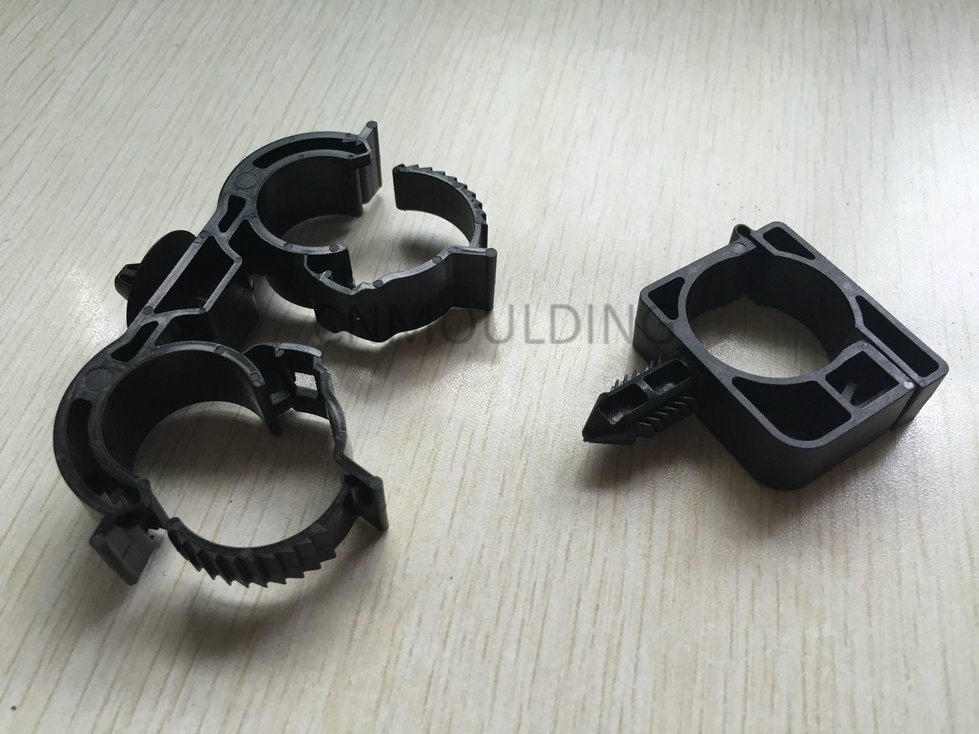
Design considerations for plastic injection molding
Plastic injection molding is a widely used manufacturing process for producing a variety of plastic products. It involves injecting molten plastic into a mold cavity, allowing it to cool and solidify, and then ejecting the finished product. The design of the injection mold is a crucial factor that can significantly impact the quality and consistency of the final product. In this article, we will explore some important design considerations for plastic injection molding.
Mould effects on injection molding
Before diving into the design considerations, let's first understand the effects of the mold on the injection molding process and the final product's quality and consistency.
Part shrinkage
One of the common effects of the mold on injection molding is part shrinkage. The design and construction of the mold can influence the part's shrinkage during the cooling process. If the mold is not properly designed or constructed, it can lead to dimensional inaccuracies and warping in the final product. It is crucial to consider factors such as cooling channels and venting systems to control part shrinkage and ensure dimensional accuracy.
Surface finish
The mold's surface finish plays a significant role in the final product's surface finish. A smooth and polished mold surface can result in a high-quality surface finish for the product. On the other hand, a rough or poorly finished mold surface can lead to imperfections, defects, and an unsatisfactory appearance for the product. The choice of mold material and the application of proper surface treatments are essential to achieve the desired surface finish.
Gate location
The location of the gate, which is the entry point for the molten plastic into the mold cavity, can impact the flow of the plastic material. The gate location should be strategically positioned to ensure uniform filling of the mold cavity and to avoid the formation of air traps or flow marks. Improper gate location can result in weak spots, reduced strength, and decreased durability of the final product.
Material flow
The design of the mold can significantly affect the flow of the molten plastic material. The flow of plastic material within the mold determines the formation of the final product and can result in various defects if not carefully considered. Issues such as voids, sink marks, and weld lines can arise from improper material flow. Proper venting, gate design, and channeling systems should be incorporated into the mold design to ensure optimal material flow and minimize defects.
Cycle time
The design of the mold can also impact the injection molding cycle time. Cycle time refers to the time required for each injection molding cycle, including the injection, cooling, and ejection phases. Longer cycle times can reduce production efficiency and increase costs. Therefore, mold design should aim to optimize the cooling system, minimize the cooling time, and ensure efficient ejection of the finished product to achieve shorter cycle times.
Considering all these effects of the mold on injection molding, it becomes clear that the design and construction of the mold are critical to achieving consistent and high-quality production. Any issues with the mold can result in defects and deviations in the final product, impacting its performance, appearance, and marketability.
Design tips for injection molding
Now that we understand the importance of mold design in injection molding, let's explore some design tips that can help ensure optimal results.
Collaboration between designers and mold manufacturers
Effective collaboration between product designers and mold manufacturers is essential for successful injection molding. Designers should work closely with mold manufacturers to understand the intricacies of the molding process, the limitations of the mold, and the possibilities for optimization. By involving mold manufacturers early in the design process, potential issues can be identified and resolved upfront, resulting in a more efficient and successful production process.
Consider draft angles
Draft angles are essential in injection molding as they facilitate easy release of the finished product from the mold. Designers should incorporate draft angles into the part design to ensure smooth ejection and prevent damage to the mold or the product. The specific draft angle required depends on factors such as material choice, part geometry, and the desired finish. Collaborating with mold manufacturers can help determine the optimal draft angles for a particular design.
Wall thickness consistency
Consistent wall thickness in the part design is crucial for achieving uniform cooling and reducing the risk of defects such as shrinkage, warping, or sink marks. Designers should strive to maintain a consistent wall thickness throughout the part, avoiding abrupt transitions or thick sections. By ensuring even distribution of plastic material during the molding process, consistent wall thickness promotes product integrity and reduces the likelihood of deformation.
Proper gate selection
The selection of the gate type and location is critical in injection molding. Different gate types, such as edge gates, direct gates, or hot runner systems, offer various advantages and disadvantages. Factors to consider when selecting the gate include material characteristics, part geometry, fill time requirements, and aesthetic considerations. Proper gate selection can help achieve optimal material flow and avoid common molding defects.
Vent placement and design
Venting is crucial for the removal of air and gases during the injection molding process. Insufficient venting can result in air traps, voids, and other defects. Designers should carefully consider the placement and design of vents to ensure proper air evacuation and prevent part defects. Collaborating with mold manufacturers to determine the optimal venting requirements can help achieve high-quality and defect-free parts.
Careful selection of mold materials
The choice of mold materials is vital for achieving consistent and high-quality injection molding. Factors such as mold durability, heat transfer properties, surface finish, and mold life should be considered when selecting the mold material. Collaboration between designers and mold manufacturers can help determine the most suitable material for a specific application, taking into account factors such as cost, production volume, and part complexity.
By considering these design tips and collaborating closely with mold manufacturers, designers can ensure that the injection molding process is efficient, cost-effective, and produces high-quality products. Attention to detail in the mold design, proper material selection, and adherence to best practices in injection molding can result in superior products that meet customer expectations and achieve success in the market.