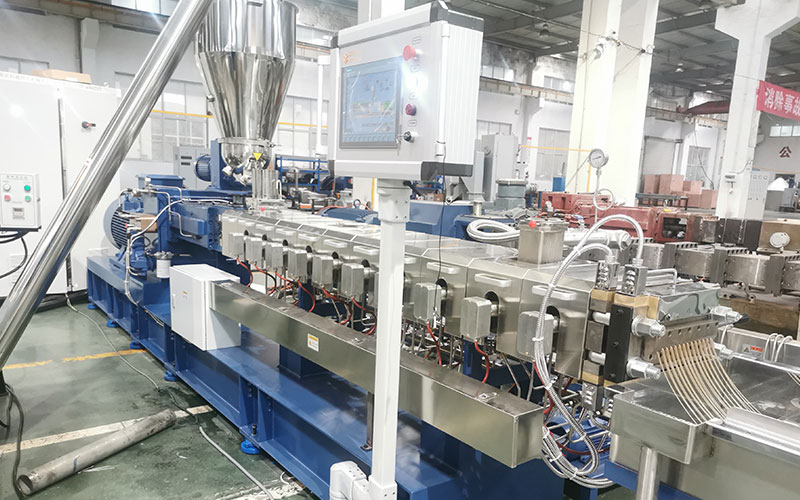
Why Twin Screw Extruder Needs to be Cleaned?
Product Quality: Contaminants, residues, or impurities can negatively impact the quality of the extruded product. Cleanliness ensures that the final output meets the desired specifications, preventing defects and maintaining consistency.
Equipment Performance: Residual materials left in the extruder can accumulate and affect the performance of the screws and barrels. This can lead to uneven mixing, poor melt quality, and fluctuations in the extrusion process, ultimately impacting the efficiency of the equipment.
Maintenance and Longevity: Regular cleaning helps prevent wear and tear on the components of the extruder. Accumulated residues can degrade the screws and barrels over time, reducing their lifespan and necessitating more frequent maintenance or even premature replacement.
Process Stability: Clean twin-screw extruders contribute to process stability. Consistent and predictable performance is essential in extrusion processes, and maintaining cleanliness helps achieve and sustain the desired operating conditions.
Contamination Prevention: Cross-contamination between different materials or batches is a concern in extrusion processes. Thorough cleaning between runs helps prevent contamination, ensuring that the extruder produces the intended product without unintended variations.
Energy Efficiency: Clean extruder components facilitate better heat transfer and reduce friction during the extrusion process. This can contribute to energy efficiency, as a clean system requires less energy to achieve and maintain the desired temperature and processing conditions.
Regulatory Compliance: In industries where strict quality and safety standards are enforced, maintaining cleanliness is often a regulatory requirement. Adhering to these standards is essential for compliance and ensures that the final product meets industry-specific criteria.
In summary, cleaning is integral to the efficient and effective operation of twin-screw extruders. It directly impacts product quality, equipment performance, maintenance requirements, process stability, contamination prevention, energy efficiency, and regulatory compliance. Regular cleaning practices are therefore essential for achieving optimal results in extrusion processes.
7 Ways To Clean Twin Screw Extruder
The methods for cleaning twin-screw extruders can vary depending on the type of extruder and the materials being processed, but here are some common methods:
Mechanical Cleaning:
Manual Scrubbing: Physical removal of residues by manually scrubbing the screws, barrels, and other components with brushes, scrapers, or other tools.
Air Blowing: Using compressed air to blow away loose particles and residues from the extruder components.
Chemical Cleaning:
Solvent Cleaning: Using appropriate solvents to dissolve and remove polymer residues. The choice of solvent depends on the type of polymer being processed.
Cleaning Compounds: Specialized cleaning compounds or pellets designed to purge and clean the extruder by melting and flushing out contaminants. These are often chosen based on the specific polymer being used.
Heat Soaking:
Running Clean Polymer: Running a clean polymer through the extruder at elevated temperatures to melt and flush out residual materials. This is effective for purging and cleaning but may not be suitable for all polymers.
Combination Methods:
Mechanical and Chemical Combined: A combination of manual scrubbing and the use of cleaning compounds or solvents for a more thorough cleaning process.
Two-Step Purging: Using a purging compound first to remove contaminants, followed by a polymer flush for final cleaning.
Cryogenic Cleaning:
Dry Ice Blasting: Using dry ice pellets to blast away contaminants. This method is non-abrasive and leaves no residue, making it suitable for certain applications.
Ultrasonic Cleaning:
Ultrasonic Baths: Immersing extruder components in a cleaning solution and subjecting them to ultrasonic vibrations. This helps dislodge and remove contaminants from hard-to-reach areas.
Regular Maintenance Practices:
Scheduled Shutdowns: Planning regular shutdowns for comprehensive cleaning and maintenance to prevent the buildup of contaminants over time.
Preventive Maintenance: Implementing preventive maintenance measures to reduce the frequency and intensity of cleaning requirements.