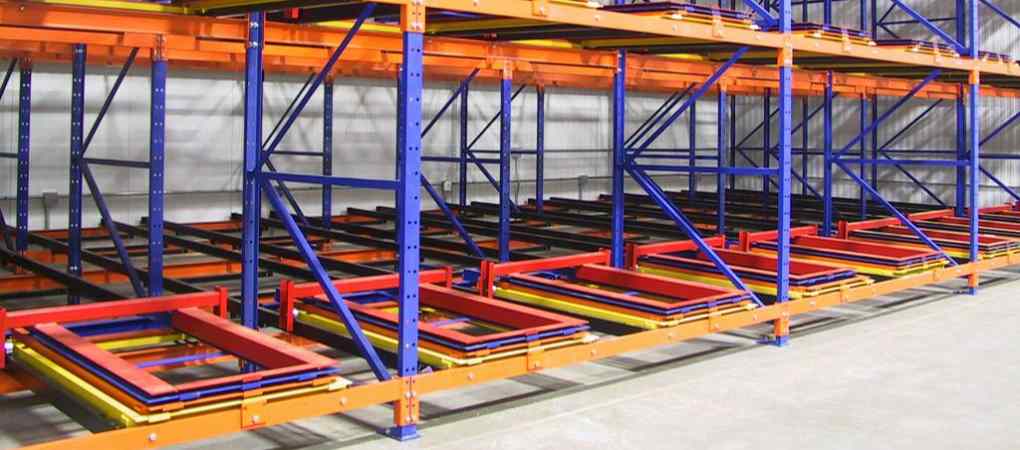
In the fast-paced world of logistics and warehousing, optimizing storage solutions is a key factor in driving productivity. Push back racking has emerged as a revolutionary system, offering a dynamic approach to pallet storage that goes beyond traditional methods. This comprehensive guide delves into the intricacies of pushback, exploring its design, benefits, and implementation to enhance overall warehouse productivity.
Understanding Push Back Racking: The Basics
The push-back rack system is a high-density storage system designed to maximize warehouse space efficiently. Unlike traditional storage methods, the push-back system enables multiple pallets to be stored in a single lane, with each subsequent pallet pushing the previous one back. This Last-In, First-Out (LIFO) system ensures that the last pallet loaded is the first to be retrieved, facilitating easy access to recently stored products.
The Components of Push Back Racking: How It Works
At the heart of the push-back rack are a set of nested carts that operate on inclined rails within each storage lane. Pallets are loaded onto these carts, and as a new pallet is added, it pushes the existing pallets back along the rails. The inclined design allows for automatic positioning of pallets, ensuring that the front pallet is always the last one added, simplifying retrieval.
Advantages of Push-Back Racking: Boosting Efficiency
This racking offers a range of advantages that contribute to enhanced warehouse productivity. The system maximizes vertical space, enables efficient use of cubic footage, and reduces the need for extensive aisles, thereby optimizing the overall layout. This results in increased storage capacity and minimizes unnecessary travel for forklift operators, streamlining both storage and retrieval processes.
High-Density Storage: Making the Most of Vertical Space
One of the primary advantages of a push-back system is its high-density storage capability. By allowing pallets to be stored in multiple positions deep within each lane, the system makes efficient use of vertical space. Warehouses with high ceilings can capitalize on this feature, significantly increasing their storage capacity without expanding their physical footprint.
Dynamic Configuration: Adapting to Inventory Changes
Warehouse needs are dynamic, with inventory volumes and turnover rates constantly changing. Racking systems offer flexibility in storage configurations, allowing warehouses to adapt to these changes easily. As the system operates on a dynamic rail system, it accommodates different pallet sizes and varying SKUs, ensuring optimal use of space regardless of the evolving inventory landscape.
Efficient Loading and Unloading: Streamlining Operations
Pushback streamlines both loading and unloading processes, contributing to overall operational efficiency. Forklift operators can load and unload pallets with ease, as the dynamic nature of the system ensures that each pallet is readily accessible. This efficiency reduces the time spent on these tasks, allowing warehouses to handle more products within the same timeframe.
Reduced Aisle Requirements: Space Optimization
Traditional storage systems require wide aisles for forklift movement, leading to wasted space. Push-back minimizes the need for extensive aisles, optimizing the overall layout of the warehouse. With reduced aisle requirements, more space is allocated to valuable inventory, contributing to space optimization and increased overall efficiency.
Enhanced Order Picking: Improving Fulfillment Speed
Efficient order picking is crucial for timely order fulfillment. The racking system, with its Last-In, First-Out (LIFO) system, enhances order picking by ensuring that the most recently stored products are readily accessible. This reduces the time spent searching for specific items, leading to faster and more efficient order fulfillment.
Minimized Product Damage: Gentle Handling
Push-back minimizes product damage by reducing unnecessary movements. Traditional storage methods often involve rearranging multiple pallets to access the one at the back, increasing the risk of collisions and damage. With push-back racking, pallets are retrieved without disturbing others in the same lane, minimizing the chances of product damage during storage and retrieval.
Safety Standards and Training: Prioritizing Employee Well-being
Safety is paramount in warehouse environments, and these systems contribute to maintaining high safety standards. By reducing the need for extensive aisle travel and minimizing the potential for forklift collisions, these systems create a safer working environment. Employee training programs on the proper use of these rackings further enhance safety and reduce the risk of accidents.
These racks stand as a beacon of innovation in the realm of warehousing, offering a comprehensive solution to drive productivity and efficiency. From high-density storage and dynamic configurations to efficient loading and order picking, the advantages of push-back systems are reshaping the landscape of warehouse management. As businesses strive for advanced storage solutions that not only optimize space but also streamline operations, pushback emerges as a dynamic and forward-thinking choice for those pushing the boundaries of productivity in modern warehouses.