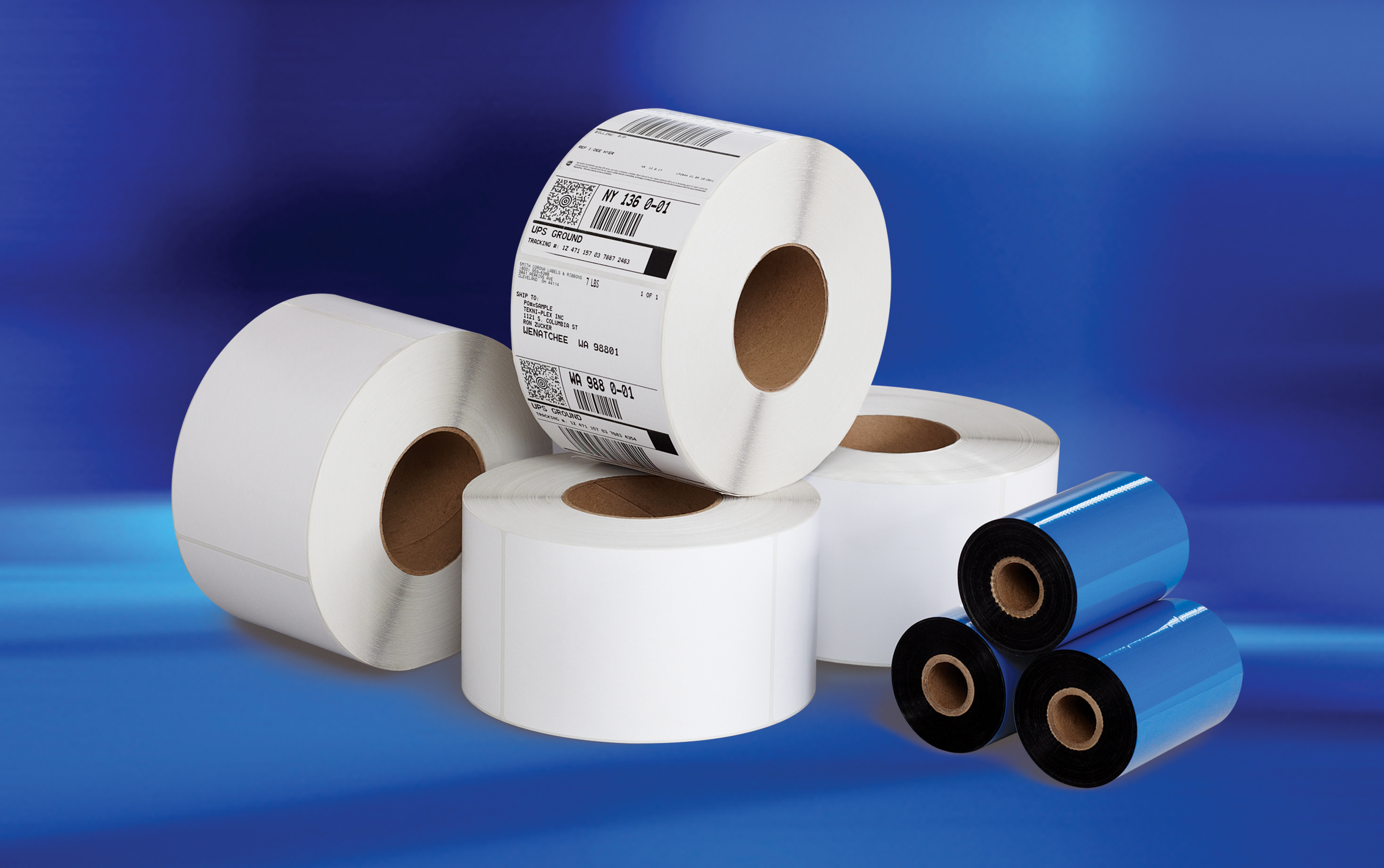
Introduction
Pressure labels play a vital role in safeguarding products that need to be transported, stored or distributed under pressure. Whether it's a gas cylinder, food can or beverage bottle, pressure labels serve as visual indicators to alert consumers and operators about pressure levels inside containers. In this article, we will explore the different types of pressure labels, their functioning, regulations and importance in ensuring safety.
Types of Pressure Labels
Pressure labels come in various designs based on the application and pressure levels they are meant to indicate. Some common types include:
- Seal Type Labels: These come with an adhesive backing and seal the surface of containers. The seal breaks on exposure to excessive pressure, providing a visual indication. These are used for lower pressure ranges.
- Snap Type Labels: Similar to seal labels but have an integrated snap mechanism that breaks loose if pressure rises above normal levels. Commonly used for gas cylinders and storage tanks.
- Frangible Disk Labels: Contain a thin metal or plastic disk that bursts when pressure crosses safety thresholds. The disk breaking is clearly visible. Used for high pressure applications like propane cylinders.
- Peel Type Labels: Have a laminated construction with an upper peelable layer. Internal gas pressure causes the layer to peel off partially or fully. Used in food and beverage packaging.
Functioning and Role in Safety
Pressure labels function as the first line of defense to alert users about abnormal pressure conditions that could lead to hazards if not addressed promptly. Their visual cues are extremely useful in:
- Detecting pressure leaks or drops in closed container systems like gas pipelines.
- Indicating over-pressurization risk due to excessive heat exposure during storage or transportation.
- Warning users not to use containers that show signs of label damage due to previous pressure deviations.
- Affixing critical pressure specifications directly on products so operators are aware of normal and safety thresholds.
By drawing attention to even small pressure variations non-intrusively, labels help avoid dangerous situations from developing into accidents. They play a proactive safety role.
Regulations for Different Industries
Regulatory standards make Pressure labels mandatory for numerous industry categories to ensure consumer and worker safety. Some key mandates include:
- Gas Cylinders: The NPGA and DOT dictate label requirements like pressure ratings, hazard warnings for flammable contents, and tampering evidence.
- Food Packaging: FDA standards under CFR Title 21 require flexible pressure release labels for canned goods above 5PSI. Specific designs are approved.
- Beverage Bottles: Labels must indicate designed storage and transportation pressure limits according to ASTM and ISO norms.
- Industrial Tanks: OSHA, EPA and NFPA codes have stringent guidelines for pressure vessels and piping systems to prevent explosions.
Compliance with applicable regulations is essential as non-conforming or missing labels can lead to penalties, recalls or denial of product certifications.
Advancements and Future Scope
Modern pressure sensitive adhesives, film substrates and digital printing have enabled new evolutions in label design and construction. Some examples include:
- Customizable multi-color graphics and information panels for specific equipment.
- Tamper-evident and tamper-proof variants integrated with security features.
- Smart labels powered by printed electronics with pressure sensors, temperature gauges and connectivity ports.
- Self-adhesive radio-frequency identification tags for real-time inventory and performance monitoring.
As Internet of Things finds wider adoption, pressure labels are paving the way for digitization across supply chains from remote sensor data collection. Their usage scopes will further expand into newer verticals like healthcare, aerospace and even infrastructure monitoring over the coming decade.
Conclusion
In summary, pressure labels have emerged as a critical component of any product or system involving pressurized storage and distribution. By detecting small variations non-intrusively and promptly communicating hazards through visual alerts, they play a key preventive role in ensuring safety. With ongoing innovations, labels will continue enhancing transparency, compliance and operational efficiencies globally across industries in pressure-reliant areas. Adherence to relevant regulations remains imperative.
Get more insights, On Pressure Labels