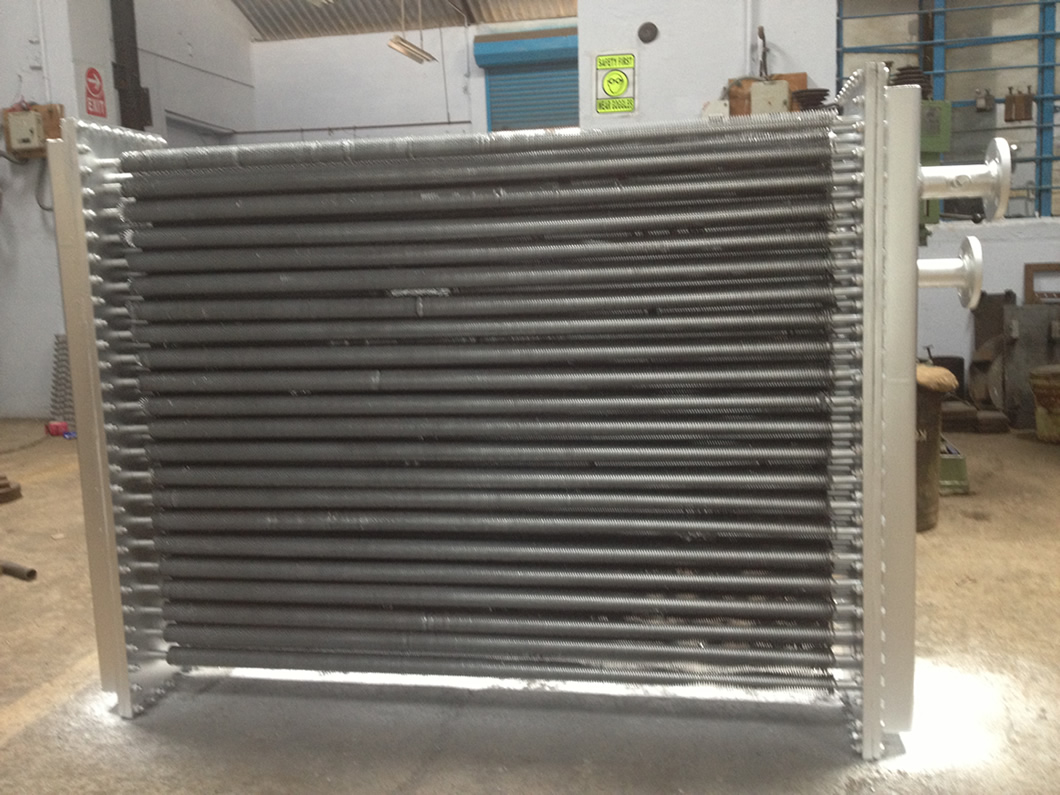
In today's industrial and commercial sectors, efficient heat transfer is pivotal for maximizing energy utilization, reducing operational costs, and minimizing environmental impact. Among the various heat exchanger technologies, plate fin heat exchangers have emerged as a robust and highly effective solution for a wide range of applications. This blog delves into the world of plate fin heat exchangers, exploring their design, advantages, and the crucial role they play in enhancing thermal performance across diverse industries.
Understanding Plate Fin Heat Exchangers
Plate fin heat exchangers, also known as compact heat exchangers, are designed to facilitate efficient heat transfer between two fluids while occupying minimal space. Their compact and intricate construction consists of a series of thin, parallel plates interspersed with corrugated fin surfaces. This unique design maximizes the surface area available for heat transfer, enabling high thermal effectiveness within a compact footprint.
The plate fin heat exchanger's core components include a parting sheet, fin layers, and side bars. The parting sheet separates the hot and cold fluid streams, while the fin layers provide extended surface area for enhanced heat transfer. The side bars serve as structural support and facilitate fluid distribution and collection.
Advantages of Plate Fin Heat Exchangers
- High Thermal Efficiency: Plate fin heat exchangers excel in their ability to transfer heat efficiently due to their large surface area-to-volume ratio. This design characteristic enables them to achieve high thermal effectiveness, making them ideal for applications where space constraints or weight limitations are critical factors.
- Compact Design: The compact nature of plate fin heat exchangers allows for significant space savings, making them a preferred choice in industries where floor space is at a premium, such as automotive, aerospace, and power generation.
- Versatility: These heat exchangers can be designed to handle a wide range of fluids, including gases, liquids, and two-phase mixtures, making them versatile across diverse applications.
- Low Fluid Resistance: The corrugated fin design minimizes fluid resistance, resulting in lower pressure drops and reduced energy consumption for fluid circulation.
- Durability and Corrosion Resistance: Plate fin heat exchangers can be constructed from various materials, including aluminum, stainless steel, and specialized alloys, ensuring durability and resistance to corrosion in demanding environments.
Applications and Industries
Plate fin heat exchangers find widespread applications across numerous industries due to their exceptional thermal performance and compact design. Some of the key industries that benefit from this technology include:
- Automotive and Aerospace: Plate fin heat exchangers are extensively used in automotive and aerospace applications for cooling systems, air conditioning units, and engine heat exchangers, where weight and space constraints are critical.
- HVAC and Refrigeration: These heat exchangers are essential components in heating, ventilation, air conditioning, and refrigeration systems, contributing to energy efficiency and indoor air quality.
- Power Generation: In power plants, plate fin heat exchangers play a vital role in recovering waste heat, improving overall plant efficiency, and reducing environmental impact.
- Chemical and Petrochemical: The chemical and petrochemical industries rely on plate fin heat exchangers for processes involving heat transfer, such as distillation, separation, and reactor cooling.
- Cryogenic and Natural Gas Processing: Plate fin heat exchangers are well-suited for cryogenic applications and natural gas processing, where efficient heat transfer at low temperatures is crucial.
Maintenance and Longevity
Like any critical component, plate fin heat exchangers require proper maintenance to ensure optimal performance and longevity. Regular inspections, cleaning, and coil replacements are essential to prevent fouling, scale buildup, and corrosion, which can degrade thermal efficiency and potentially lead to system failures.
Professional heat exchanger services play a vital role in maintaining these crucial components. Experienced technicians can perform thorough inspections, cleanings, and repairs or replacements as needed, ensuring that the heat exchanger continues to operate at peak performance while minimizing the risk of potential hazards.
Conclusion
In the quest for energy efficiency and thermal optimization, plate fin heat exchanger have emerged as a game-changing technology. Their compact design, high thermal effectiveness, and versatility make them invaluable assets across a wide range of industries. By leveraging the benefits of plate fin heat exchangers and partnering with professional heat exchanger services, businesses can unlock new levels of operational efficiency, cost savings, and environmental sustainability. Investing in this cutting-edge technology is a strategic move towards a more energy-conscious and sustainable future.