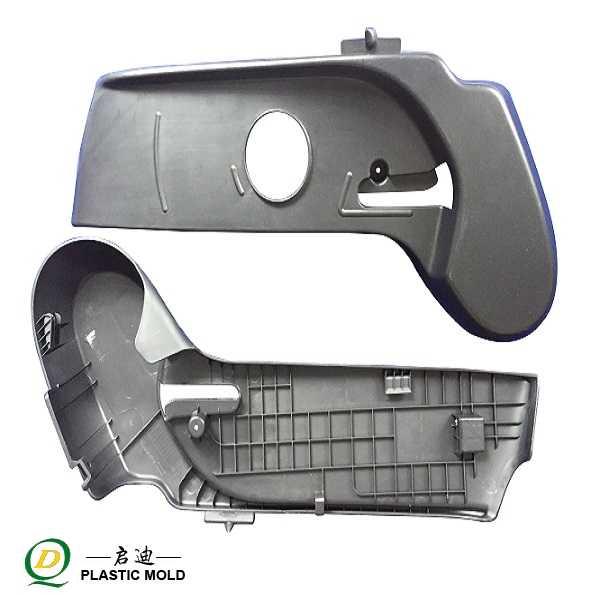
ABS plastic, quick for Acrylonitrile Butadiene Styrene, is a versatile and broadly used thermoplastic respected for its strength, sturdiness, and affordability. It finds usage in different industries, forming it via Molding ABS Plastic, especially injection molding. This article explores the making process of ABS plastic molds and the critical components of molding this well known substance.
Why select ABS plastic molds?
● Strength and Durability: ABS gives impressive impact resistance and might withstand wear and tear, making it ideal for parts needing mechanical strength.
● Cost effectiveness: Unlike other engineering plastics, ABS is distinctly less priced, making it a cost aware desire for many applications.
● Lightweight: ABS is lighter than metals, delivering weight reduction blessings in applications wherein weight management is vital.
Know how the molding ABS plastic process.
ABS plastic molding commonly makes use of the injection molding approach.
Step 1: Design the mold
Using computer-aided design (CAD) software, make the shape. The mold tells the exact dimensions and frame of the planned ABS plastic component. Steel and aluminum are two materials with which you can develop the mold; your choice will depend on things like multifaceted nature and expected fabricating volume.
Step 2: Material selection
Select the suitable ABS plastic material by considering features like color, strength, heat resistance, and any application-specific specifications.
Step 3: Preparation
Make sure the mold's surface is clean and ready to go, free of any dirt or impurities that can interfere with the ABS Plastic Molding process.
Step 4: Heating the ABS
Since ABS plastic is a thermoplastic, heat may cause it to melt and form. The extruder can load ABS pellets, which are heated and melted to the proper temperature for molding.
Step 5: Injection molding
Apply intense pressure as you inject the molten ABS plastic into the prepared mold cavity. The plastic is guaranteed to flow into every area of the mold and take on the shape that it is for.
Step 6: Cooling
As the ABS plastic within hardens, let the mold cool. The size and thickness of the molded item affect the cooling time.
Step 7: Ejection
Expel the component from the mold once the ABS plastic has cooled and set. Ejector pins can accomplish this automatically or manually.
Step 8: Trimming and finishing
Trim any extra material or flaws from the molded item after ejection. You can use cutting, sanding, or machining methods to get the right finish.
Step 9: Inspection of the quality
Look for flaws or departures from the required tolerances and molded item quality standards. This stage ensures that the components fulfill the requirements.
Step 10: Repetition
Use the same mold through-out the whole molding process if you require several duplicates of the same part.
Step 11: Distribution and packaging
Package the ABS plastic moldings for distribution or additional assembly once they surpass quality management inspections.
Step 12: Upkeep
Manage and cleanse the mold regularly to ensure consistency, and superior results with time. Maintaining uniformity in the product and extending the mold's life depends heavily on mold care.
Producing firms like YUYAO QIDI PLASTIC MOLD FACTORY may use ABS plastic molds to make high quality, reasonably priced parts for various applications by knowing the features of ABS plastic and the subtleties of the Molding ABS Plastic process.
Abs Plastic Molds, Abs Plastic Molding, Abs Plastic Injection Molding, Molding Abs Plastic, Abs Molding.