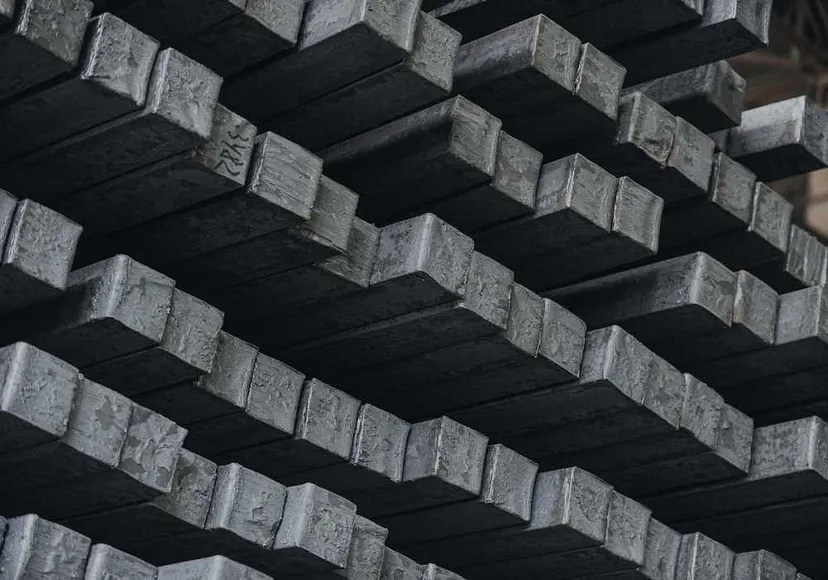
Sponge Iron Production Process
Sponge iron, also known as direct reduced iron (DRI), is a high-quality metallic product that is obtained by the reduction of iron ore in the form of lumps or pellets. The production process of sponge iron involves the use of non-coking coal and iron ore fines which are fed into a rotary kiln.
The rotary kiln is the primary equipment used for the production of sponge iron. It consists of a cylindrical shell lined with refractory material and a rotating tube with a diameter ranging from 3 to 6 meters. The coal and iron ore fines are mixed together and heated in the presence of a reducing agent, such as natural gas or coal gas.
As the mixture of coal and iron ore fines travels through the rotary kiln, it undergoes several chemical reactions. The reduction of iron ore takes place at temperatures between 800 and 1050 degrees Celsius, leading to the formation of sponge iron with a high metallization degree. The process also generates a considerable amount of waste, known as char, which can be used for various purposes.
After the sponge iron is produced, it is cooled and separated from the char using a magnetic separator. The separated sponge iron is then screened and packaged for further use in various industries.
Types of Sponge Iron
There are two main types of sponge iron based on the production process:
- Coal-based sponge iron: This type of sponge iron is produced using non-coking coal as a reducing agent. It is widely used in the steel industry as a substitute for scrap metal in electric arc furnaces. Coal-based sponge iron has a high carbon content, which helps in improving the efficiency and productivity of steelmaking processes.
- Gas-based sponge iron: Gas-based sponge iron is produced using natural gas or coal gas as a reducing agent. It is primarily used in the production of steel through the direct reduction process. Gas-based sponge iron has a lower carbon content compared to coal-based sponge iron, making it suitable for industries that require lower carbon emissions.
Applications of Direct Reduced Iron
Direct reduced iron, or sponge iron, finds applications in various industries due to its excellent metallurgical properties and cost-effectiveness. Here are some of the main applications of sponge iron:
1. Steel Industry
The steel industry is one of the largest consumers of sponge iron. Sponge iron is used as a feedstock in electric arc furnaces for the production of high-quality steel. It serves as a substitute for scrap metal and helps in reducing the overall production cost. The use of sponge iron in steelmaking also improves the quality and consistency of the final steel product.
2. Foundries
Foundries use sponge iron as a raw material for the production of cast iron and ductile iron. Sponge iron is added to the charge mix along with scrap metal, pig iron, and other alloys to enhance the metallurgical properties of the castings. The use of sponge iron in foundries ensures better control over the chemical composition and microstructure of the castings, resulting in improved casting quality.
3. Cement Industry
The cement industry also utilizes sponge iron as a substitute for coal. Sponge iron has a high calorific value and can be used as a fuel in kilns for the production of cement clinker. The use of sponge iron in cement manufacturing helps in reducing the reliance on fossil fuels and contributes to lower carbon emissions.
4. Chemical Industry
The chemical industry employs sponge iron as a reducing agent in various chemical reactions. It is used in the production of chemicals such as ammonia, methanol, and hydrogen. Sponge iron's high metallization degree and reactivity make it an ideal choice for chemical processes that require the reduction of metal oxides.
5. Powder Metallurgy
Sponge iron is widely used in the powder metallurgy industry for the production of powdered metal components. It is compacted and sintered to form metal powders that can be further processed into complex shapes. Powder metallurgy products made from sponge iron exhibit high strength, density, and dimensional accuracy.
These are just a few examples of the applications of sponge iron in various industries. Its versatility, coupled with its cost-effectiveness, makes it a highly sought-after material in the industrial sector.
As a leading Sponge Iron Manufacturer in India, Nakoda TMT Group is committed to producing high-quality sponge iron that meets the specific requirements of different industries. With state-of-the-art production facilities and a dedicated team of professionals, Nakoda TMT Group ensures consistent quality and reliable supply of sponge iron.
Whether you are in the steel industry, foundry sector, cement industry, chemical industry, or powder metallurgy field, Nakoda TMT Group is your trusted partner for all your sponge iron requirements.