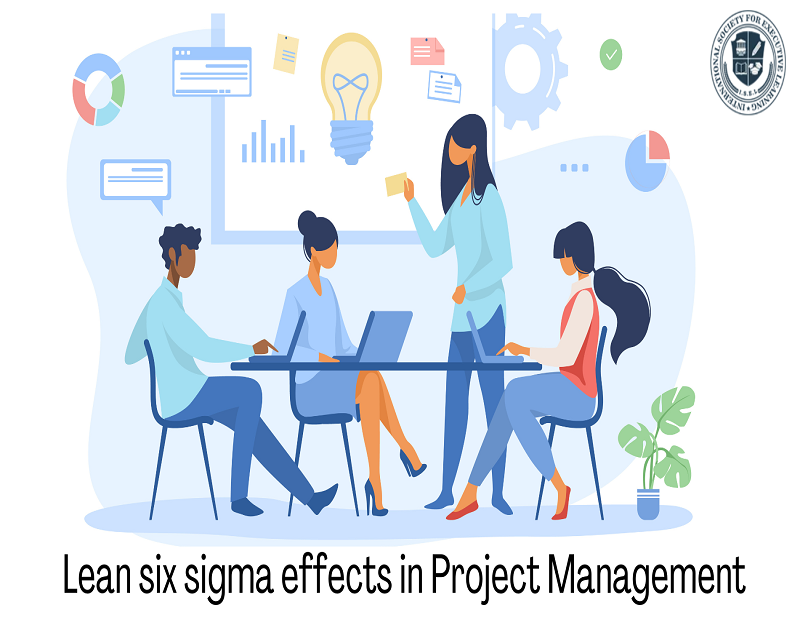

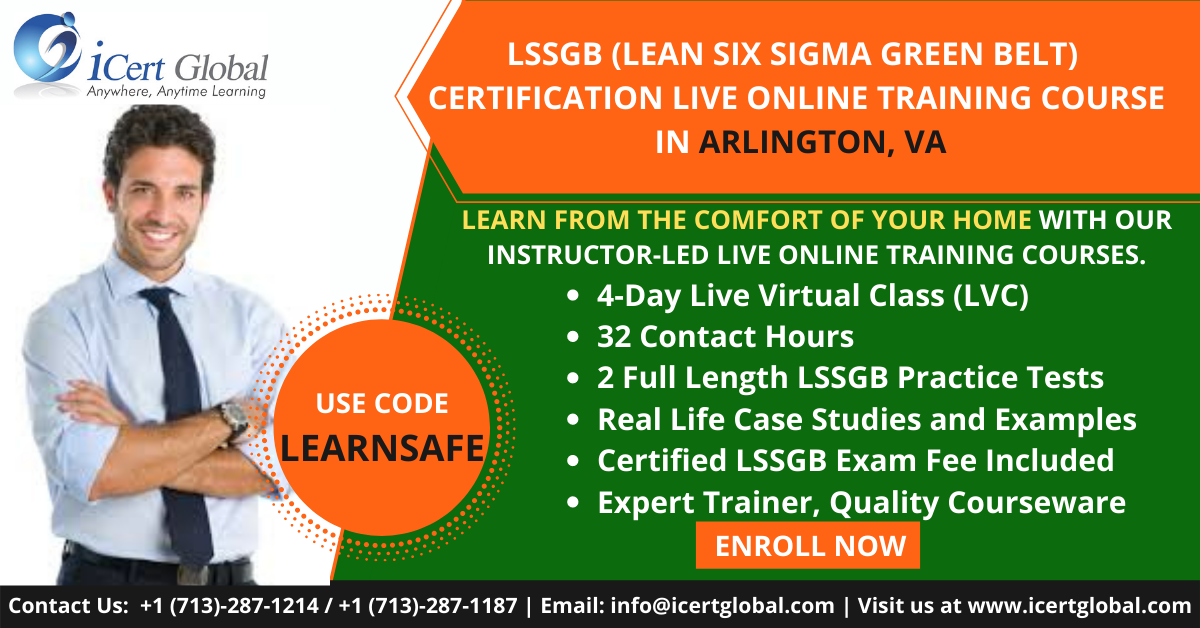
iCert Global is conducting 4-day Instructor-Led LSSGB Live Online Training (LVC) Course in Arlington, VA.Register Now!
For LSSGB Live Virtual Class in Arlington, VA scheduled fromApr 27-30, 2021 | May 25-28, 2021 | June 22-25, 2021Use code LEARNSAFE for 20% discount on our 4-day LSSGB Live Virtual Class (LVC) in Arlington, VA.Key Features for LSSGB Certification Training: • 4 day LSSGB Instructor-Led Online Class Training • 2 Full Length LSSGB Practice Tests • Certified LSSGB Exam Fee included • 100% money back guarantee • Real life case studies and Examples • 32 contact hours certification • Become a Lean Six Sigma Green Belt Certified with this training • 12 Hours Prerequisite Training Our other certifications: CAPM | PMP | LSSBB | LSSGB | PMI ACP | CBAP Register Now!
https://www.icertglobal.com/course/Lean-Six-Sigma-Green-Belt-Certification-Training-Arlington-VA/Classroom/106/228 You may also Call us on +1-713-287-1187 or +1-713-287-1214 for more details.
Value Stream Mapping in Lean Six Sigma offers information flow that can be determined on the basis of value-added or non-value-added actions.
It will help you make your work process more efficient by saving time and will also help you in increasing productivity.Please Like, Share & Subscribe for more Videos.Visit: https://elearning.mindcypress.com/courses/lean-six-sigma-green-belt/Read: https://blog.mindcypress.com/p/what-is-value-stream-mapping-in-lean-six-sigmaFacebook: https://www.facebook.com/MindCypressInstagram: https://www.instagram.com/mindcypress/LinkedIn: https://www.linkedin.com/company/mindcypressTwitter: https://twitter.com/mindcypress
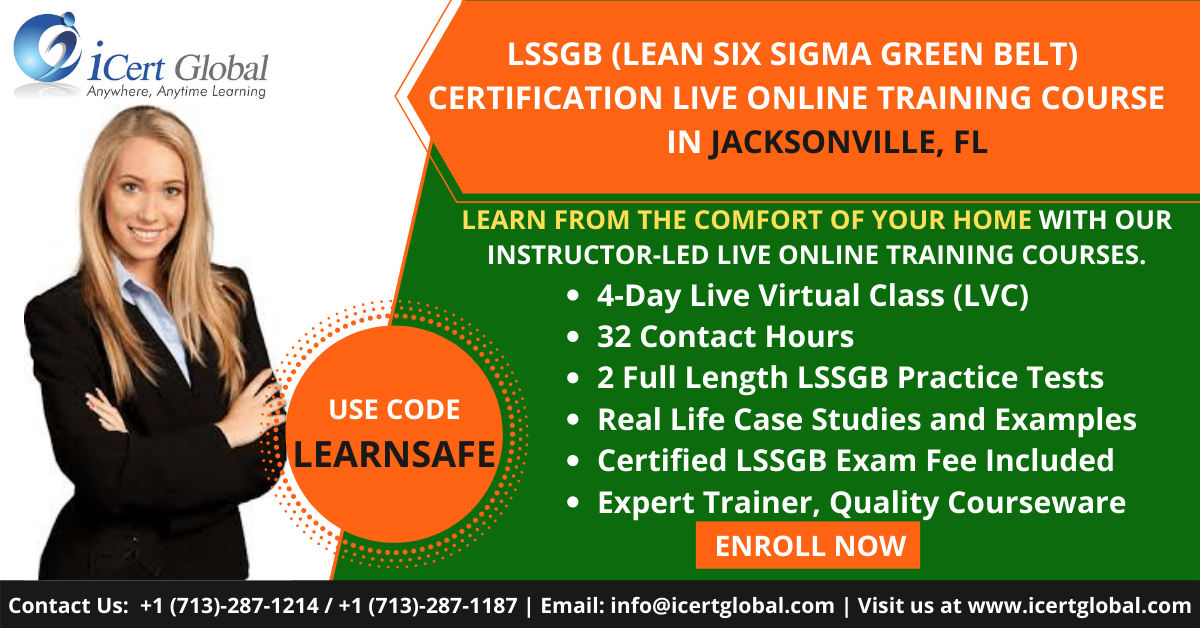
iCert Global is conducting 4-day Instructor-Led LSSGB Live Online Training (LVC) Course in Jacksonville, FL.Register Now!
For LSSGB Live Virtual Class in Jacksonville, FL scheduled fromApr 27-30, 2021 | May 25-28, 2021 | June 22-25, 2021Use code LEARNSAFE for 20% discount on our 4-day LSSGB Live Virtual Class (LVC) in Jacksonville, FL.Key Features for LSSGB Certification Training: • 4 day LSSGB Instructor-Led Online Class Training • 2 Full Length LSSGB Practice Tests • Certified LSSGB Exam Fee included • 100% money back guarantee • Real life case studies and Examples • 32 contact hours certification • Become a Lean Six Sigma Green Belt Certified with this training • 12 Hours Prerequisite Training Our other certifications: CAPM | PMP | LSSBB | LSSGB | PMI ACP | CBAP Enroll Now!
https://www.icertglobal.com/course/Lean-Six-Sigma-Green-Belt-Certification-Training-Jacksonville-FL/Classroom/106/199 You may also Call us on +1-713-287-1187 or +1-713-287-1214 for more details.
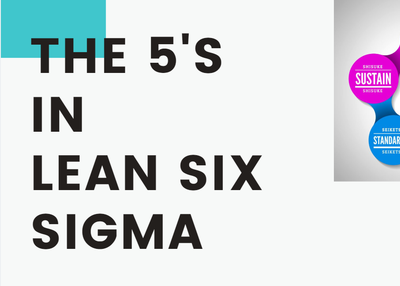
5S was initially a Japanese association strategy made out of the terms: seiri, seiton, seiso, seiketsu, and shitsuke. This philosophy was a structure square to permit Just-in-time Manufacturing.
Extra “S’s” are likewise being used that incorporates SAFETY. Safety is dependably an essential for any undertaking or occasion and ought to be assessed at each stage. All the more as of late there has additionally been an “S” for Client “Satisfactiom” and “Security”
The naming shows areas not as significant as making each stride all together and finishing each before proceeding onward the following.
The accomplishment of 5S is because of its effortlessness, simplicity of seeing, snappy effect, and general applications. It tends to be connected underway zones, office territories, and data frameworks.
Clutter can be irritating or at its outrageous even hindering to a home or workspace. Clutter happens when you wouldn’t dare hoping anymore; precedent, you spare a magazine with the goal that you can peruse it later. At that point before you know it, you have a whole lifetime of National Geographic magazines put away in your storage room! Lean’s 5S instrument is an incredible method to dispose of what you needn’t bother with.
Here’s the 5S device in real life:
Seiri (Sort): Separate garments into heaps. Separate by the required, the additional or copies, and unneeded. Do this for shoes also. To make sense of what you truly needn’t bother with, you could utilize the 5 Whys device. Simply continue asking “why” you would need said thing and if toward the end the reason isn’t sufficient, simply offer it to philanthropy.
Seiton (Straighten): Conveniently mastermind what you need, from the “required” heap. Arrange the garments and shoes in a manner where what you utilize all the more every now and again is anything but difficult to get to. Ensure you compose your things in a manner that everything is unmistakable.
Seiso (Shine): Before you really put the garments and shoes back in the storage room, ensure you clean, vacuum, and residue every one of the spaces in the wardrobe.
Seiketsu (Standardize): On the off chance that you share your storeroom space with your loved one or individuals from your family, at that point ensure they pursue the tidy up after yourself preclude after they take a thing. In the event that you don’t share the storage room space with anybody, at that point you should dependably put things away, and in the event that you purchase a thing you should dispose of a thing so you don’t create clutter once more.
Shitsuke (Sustain): Analyze the outcomes. Maybe take an after image of your recently sorted out wardrobe and relish in your prosperity. Utilize the kaizen approach and continue fixing seemingly insignificant details in your remarkably up. Try not to give them a chance to amass.
For KPMG Lean Six Sigma Training registrations mail to [email protected] or call at +91 9555688555 or +91 9022033666.
Lean Six Sigma Black Belt Training Programme
Lean Six Sigma Green Belt Training Programme
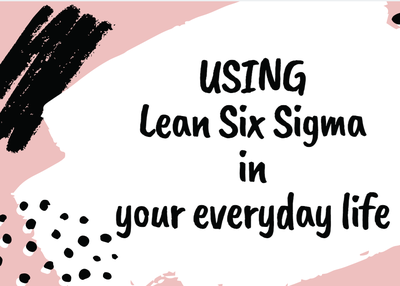
What is Six Sigma?
Six Sigma is a quality improvement process used by many Corporations and Organizations worldwide. There are several benefits for using this methodology for any business large or small. These same valuable tools and methods are ways to use Six Sigma in your daily life. Be it the start of a new year or right now, you can take up the resolution to implement Six Sigma in your daily life.
Your Plan
As a new year begins, resolutions and renewed energy drives us to improve our quality of life, personally and professionally. This is a great time to incorporate the DMAIC methodology to attain any type of goal you set. So many times we make plans to improve our daily life but the factors to achieve success have not been properly laid out.
What is it you want to accomplish; today, this month, this year? Whether it be short term or long term, your plan needs to be clearly defined with what you want to change then identify the factors.
Your Strategy
Maybe this is the year you want to buy a house. A down payment is your long term goal. Here is where using Six Sigma in your daily life will come into play. Defining your plan should clearly state how you want to save money. Determining where and how you spend your money is the Measurement phase of the process. A planned and thought out budget, listing income, expenses, wants and needs will help you see where changes can be made. Easier said than done, you have set this goal before and you still wonder where your money is going? Here is where the Analyzing step comes into play. Identifying the problem and the cause of your spending. To minimize the risk of using your savings for unplanned medical bills or car repairs, planning ahead and preparing for these surprise expenses by listing ways to aid in your savings goal. Once you have your new plan in place Improving and implementing your solutions are the key factors in accomplishing your goal. Coupons and carpooling, bringing your coffee and lunch to work are approaches to use in your savings process.
Your Accomplishment
Now that you have a solution, stay accountable and in Control. Updating and maintaining your new budget will keep you on track to attaining your savings goal and your new home. Now you can clearly see the process and how easily it can be applied, you are able to integrate the Six Sigma methods in your work, volunteer organizations and your household.
When you begin using Six Sigma in your daily life, soon enough you will integrate these tools in your daily routines, not just for an improvement process in a corporate management project.
For KPMG Lean Six Sigma Training registrations mail to
[email protected] or call at +91 9555688555 or +91 9022033666.
Lean Six Sigma Black Belt Training Programme
Lean Six Sigma Green Belt Training Programme
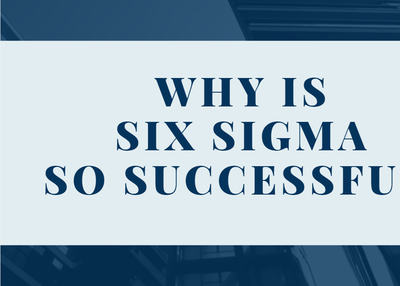
The logical tools and methods no doubt contribute a great deal towards the achievement of Six Sigma improvement ventures, yet they just can’t be taken as the sole elements in charge of Six Sigma’s viability since they just compliment the inborn rationale underlining Six Sigma and in that capacity are close to an unfortunate obligation.
So what truly makes Six Sigma so viable? All things considered, for that, you just need to investigate the most normally used Six Sigma quality improvement technique, for example, DMAIC that represents Define, Measure, Analyze, Improve and Control.
Pay special mind to similitudes between standard strategic approaches and the DMAIC stages expressed over, some of which are depicted beneath:
The Define Phase
The Define stage is very like the standard business routine with regards to recognizing basic issues of a given business process with the expectation to devise successful answers for beating the given issues and issues. It can without much of a stretch be contrasted with a business visionary’s exertion with improving the conveyance frameworks of his business by leading a survey of all the different major and minor parts of the general conveyance framework.
The Measure Phase
On the off chance that we think about the above model, the Measure stage will appear to be the same as the business visionary’s push to evaluate the negative effect that the distinguished issues can conceivably have on his general business. This is very fundamental for the business visionary since it is at exactly that point will he have the option to focus his endeavours on conquering issues that hold the most potential for harm.
The Analyze Phase
The Analyze stage is very like the business person’s push to make a rundown of all the accessible options and test every one of them exclusively to realize which elective will work best for getting the ideal outcomes.
Much the same as the business visionary would like, the Analyze stage also calls for choosing just those choices for definite execution, which hold the most potential and are financially savvy.
The Improve Phase
This stage is the same as the business person’s push to guarantee that the activities chose for improvement are executed in an endorsed way. Much the same as the business person would like, the Improve stage also stresses finishing ventures inside the stipulated time and expenses.
The Control Phase
Similarly, as the business person might want to check the viability of the improvement extends, the Control stage also stresses surveying whether the improvement activities are executing according to desires. Taking medicinal measures if there is a befuddle is inborn to the Control stage, similarly as a business person might want to do.
For KPMG Lean Six Sigma Training registrations mail to [email protected] or call at +91 9555688555 or +91 9022033666.
Lean Six Sigma Black Belt Training Programme
Lean Six Sigma Green Belt Training Programme
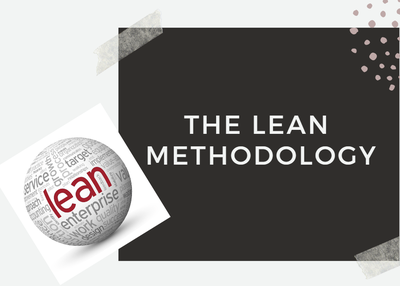
The Lean methodology is gaining a reputation for its capacity to assist companies to obtain their goals in a more fit, smarter, more sustainable manner. Lean allows companies to optimize throughout the cost movement for price delivery, improving speed, excellence, and organizational fitness. Lean originated with the Toyota Production System, which revolutionized the manufacture of bodily goods within the 1950s, ‘60s, and past. Lean keeps its hold in production but has additionally determined new programs in understanding work, assisting organizations to eliminate waste, enhance techniques, and raise innovation.
Of course, the nature of knowledge work differs substantially from that of producing: specifically, the value being created in information work is inside the minds of people, no longer at the meeting line. This affords a unique set of challenges and opportunities when making use of Lean to expertise work. Agencies from all disciplines of understanding work discover the first-rate achievement with lean, using it to propel them into greater efficiency.
To understand how lean is carried out to understanding work, it’s beneficial to recognize the history of lean manufacturing.
A brief history of lean:
Within the '80s and ‘90s, western manufacturers struggled to keep up with the greater efficient eastern groups, in order that they had options: trim down or shut down. They commenced adopting the practices of eastern organizations to enhance their speed, productiveness, and cost efficiency to stay competitive.
During this time, lean changed into boiled right down to overly simplistic ideas, normally used to justify relentless fee cutting. Nowadays, the manufacturing enterprise employs some distance fewer human beings than it once did. There are also fewer gamers in this area; they’re leaner but large.
Many versions of lean methodology were born inside the years following, which include Total Quality Management, Just-in-time, Six Sigma, and the idea of constraints. Each of these moves included numerous practices from what the Japanese had been doing that differentiated them from their competition, even though we will properly say that what they have been aiming for is now called lean. A lot of these famous “lean” management frameworks were tremendously prescriptive by using nature and required enormous education to adopt absolutely.
Today, businesses are looking to transform the way they work with the aid of making use of Lean Standards, especially: continuous development and respect for people.
Lean solutions empower groups to deliver faster by way of visualizing value streams, optimizing the go with the flow of labour and constantly improving their overall performance. Lean delivery gives the following advantages:
● Optimizing float by way of visualizing cost streams and reducing dependencies.
● Fueling non-stop development via studying overall performance, identifying traits, and evolving techniques.
● Leveraging lean principles to empower teams to innovate, adapt, and deliver value quicker.
● Handing over large, extra complex results by way of coordinating workstreams throughout groups.
● Scaling to the portfolio level to stability timing, staffing, and price for delivery of corporation-stage projects.
● Driving strategic tasks with road mapping and iterative funding of cost streams.
For KPMG Lean Six Sigma Training registrations mail to
[email protected] or call at +91 9555688555 or +91 9022033666.
Lean Six Sigma Black Belt Training Programme
Lean Six Sigma Green Belt Training Programme
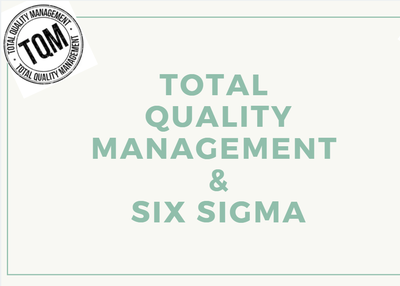
The causes of Total Quality Management (TQM) had numerous progenitors in its initiation, yet was nonexclusive in nature. Which means you could plug crafted by Ishikawa, Juran and Deming (just to give some examples) into any business and you’d get results — just not the best outcomes for your particular business.
Six Sigma has a few contracts from TQM — it puts a significantly more grounded spotlight on client prerequisites; all things considered, organizations are there to serve their clients. Along these lines, Voice of the Client (VOC) is critical in the nature of their item or administration.
Six Sigma likewise requires extra tools utilized in information examination. The budgetary spotlight is on a venture level — with TQM, it is on an authoritative dimension.
The unmistakable comprehension is that Six Sigma’s strategies have an outlook of having a triumph rate of 99.9997% or under 3.4 deformities per million chances. With these high objectives, particularity is an unquestionable requirement.
So as to accomplish this dimension of magnificence, a Six Sigma culture must exist all through the business or association. General Electric has had such an enormous accomplishment with Six Sigma that in the event that you go to their site you’ll see that they are Six Sigma’s greatest backer.
In days gone by, it was trusted that if a business yielded to their client that it would cost that business an excessive amount of cash. Truth be told, the inverse is valid.
Here’s a decent similarity: getting a garden of delightfully planted turf, however you needed to scene your new yard with wonderful shakes and water productive foliage. In spite of the fact that the turf looks incredible, it was not what you needed and it is a major dissatisfaction — to both the client and the business. The client feels unheard and the business feels overlooked for delivering an extraordinary item. It’s not extraordinary in the event that it isn’t what the client required. This can at last lead to lost clients as time goes on.
For KPMG Lean Six Sigma Training registrations mail to [email protected] or call at +91 9555688555 or +91 9022033666.
Lean Six Sigma Black Belt Training Programme
Lean Six Sigma Green Belt Training Programme
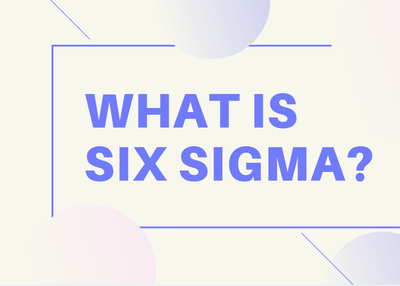
Six Sigma originates from a 19th Century numerical hypothesis, however discovered its way into the present standard business world through the endeavors of an engineer at Motorola during the 1980s. Presently proclaimed as one of the chief methodological practices for improving consumer satisfaction and improving business forms, Six Sigma has been refined and idealized throughout the years into what we see today.
Regardless of the defining, the objective continues as before: Six Sigma looks to improve business forms by expelling the reasons for mistakes that lead to deserts in an item or administration. It achieves this by setting up an administration framework that efficiently recognizes mistakes and gives techniques to killing them.
The individuals who learn Six Sigma practices accomplish assignments at each dimension of achievement, including Green Belt, Black Belt, Master Black Belt and Champion.
The Beginnings of Six Sigma:
The procedure that prompted Six Sigma was started in the Nineteenth Century with the bell curve created by Carl Fredrick Grauss. During the 1920s, analyst Carl Shewhart, an establishing individual from the Foundation of Scientific Insights, demonstrated that a procedure required amendment after it had veered off three sigmas from the mean.
Push ahead to the 1970s, when Motorola senior official Art Sundry grumbled about the absence of predictable quality in the organization's items, as per the 2006 book "Six Sigma" by Richard Schroeder and Harry Mikel.
As indicated by the acknowledged story from various sources, Motorola specialist Bill Smith in the end addressed the call to reliably fabricate quality items by working out the strategies of Six Sigma in 1986. The framework is impacted by, yet unique in relation to, other administration improvement methodologies of the time, including All out Quality Administration and Zero Imperfections.
Some of the Major Aspects of Six Sigma:
With an end goal to carry tasks to a "six sigma" level – basically, 3.4 imperfections for each one million chances – the technique calls for constant endeavours to come to the heart of the matter where they produce steady and unsurprising outcomes.
Deconstructing the assembling procedure down to its basic parts, Six Sigma characterizes and assesses each progression of a procedure, looking for approaches to improve efficiencies in a business structure, improve the nature of the procedure and increment the main concern benefit.
Toward that end, the procedure requires the preparation of workforce in Six Sigma, including learner Green Belts, Black Belts who frequently head up individual projects, and Master Black Belts who search for approaches to apply Six Sigma over a business structure to make upgrades.
A definitive objective is to improve each procedure to a "six sigma" level or better. Does it work? Motorola detailed in 2006 that the organization had spared $17 billion utilizing Six Sigma.
Methodologies of Six Sigma:
There are two noteworthy philosophies utilized inside Six Sigma, the two of which are made out of five segments, as per the 2005 book "JURAN Foundation Six Sigma Breakthrough and Beyond" by Joseph A. De Feo and William Barnard.
DMAIC: This strategy is utilized basically for improving existing business forms. The letters represent:
Characterize the issue and the undertaking objectives
Measure in detail the different parts of the present procedure
Break down information to, in addition to other things, discover the root surrenders in a procedure
Improve the procedure
Control how the procedure is done later on.
DMADV: This technique is commonly used to make new procedures and new items or administrations. The letters represent:
Characterize the undertaking objectives
Measure basic parts of the procedure and the item abilities
Break down the information and create different plans for the procedure, in the end picking the best one
Plan and test subtleties of the procedure
Confirm the plan by running reenactments and a test case program, and afterward giving over the procedure to the customer
There are additionally various administration devices utilized inside Six Sigma. While there are beyond any reasonable amount to list, here are subtleties on a couple of them.
Five Whys – This is a strategy that utilizations inquiries to get to the main driver of an issue. The strategy is basic: essentially express the last issue (the vehicle wouldn't begin, I was late to work again today) and afterward pose the inquiry "why," stalling the issue to its underlying driver. In these two cases, it may be: on the grounds that I didn't keep up the vehicle appropriately and in light of the fact that I have to go out prior to get the opportunity to take a shot at time. The procedure previously came to noticeable quality at Toyota.
CTQ Tree – The Basic to Quality Tree chart separates the parts of a procedure that delivers the highlights required in your item and administration in the event that you wish to have fulfilled clients.
Main driver Investigation – Much like the Five Whys, this is a procedure by which a business endeavors to recognize the underlying driver of an imperfection and after that right it, as opposed to just adjusting the surface "manifestation" of the issue.
At last, the majority of the devices and procedures in Six Sigma fill one need: to streamline business forms so as to deliver the most ideal items and administrations with the littlest measure of deformities. Its appropriation by enterprises far and wide is both a marker of and demonstration of its wonderful achievement in the present business condition.
For KPMG Lean Six Sigma Training registrations mail to
[email protected] or call at +91 9555688555 or +91 9022033666.
Lean Six Sigma Black Belt Training Programme
Lean Six Sigma Green Belt Training Programme
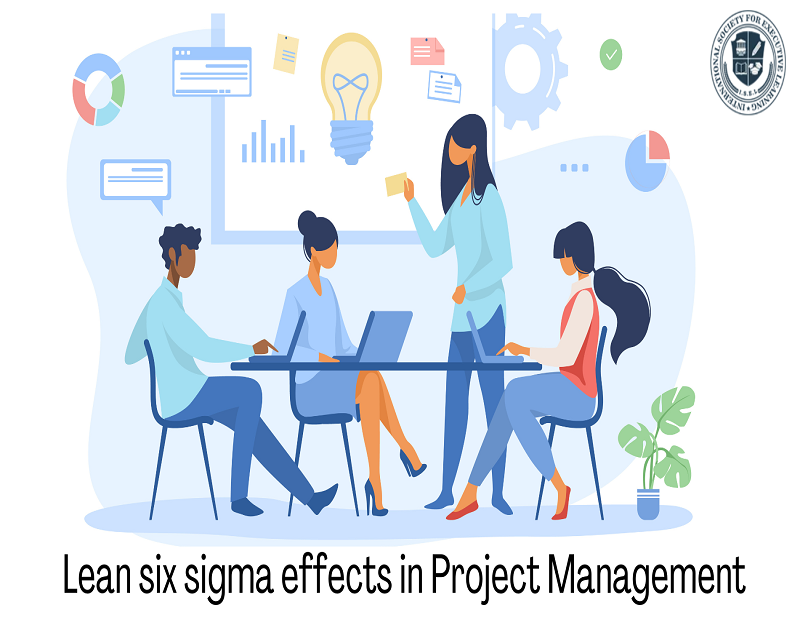
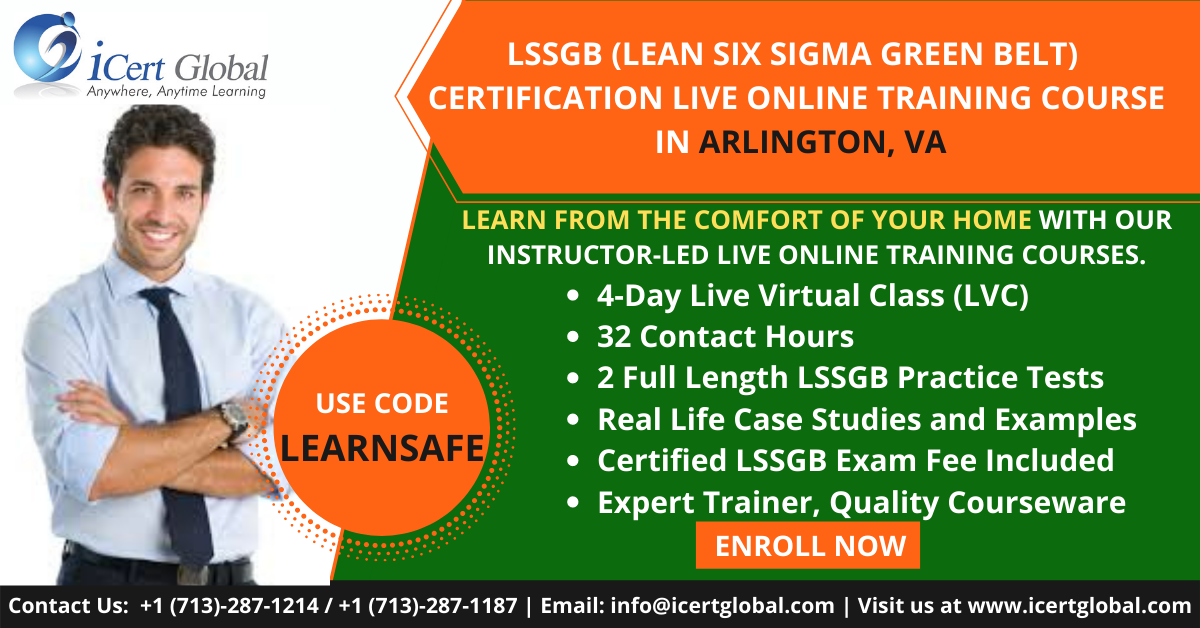
iCert Global is conducting 4-day Instructor-Led LSSGB Live Online Training (LVC) Course in Arlington, VA.Register Now!
For LSSGB Live Virtual Class in Arlington, VA scheduled fromApr 27-30, 2021 | May 25-28, 2021 | June 22-25, 2021Use code LEARNSAFE for 20% discount on our 4-day LSSGB Live Virtual Class (LVC) in Arlington, VA.Key Features for LSSGB Certification Training: • 4 day LSSGB Instructor-Led Online Class Training • 2 Full Length LSSGB Practice Tests • Certified LSSGB Exam Fee included • 100% money back guarantee • Real life case studies and Examples • 32 contact hours certification • Become a Lean Six Sigma Green Belt Certified with this training • 12 Hours Prerequisite Training Our other certifications: CAPM | PMP | LSSBB | LSSGB | PMI ACP | CBAP Register Now!
https://www.icertglobal.com/course/Lean-Six-Sigma-Green-Belt-Certification-Training-Arlington-VA/Classroom/106/228 You may also Call us on +1-713-287-1187 or +1-713-287-1214 for more details.
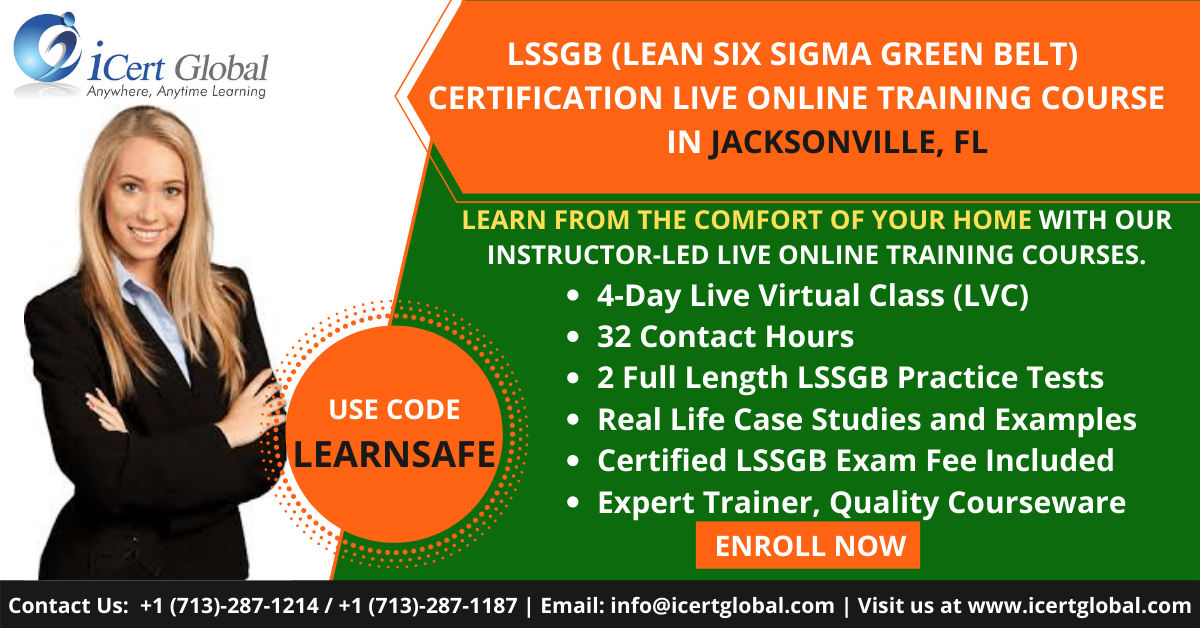
iCert Global is conducting 4-day Instructor-Led LSSGB Live Online Training (LVC) Course in Jacksonville, FL.Register Now!
For LSSGB Live Virtual Class in Jacksonville, FL scheduled fromApr 27-30, 2021 | May 25-28, 2021 | June 22-25, 2021Use code LEARNSAFE for 20% discount on our 4-day LSSGB Live Virtual Class (LVC) in Jacksonville, FL.Key Features for LSSGB Certification Training: • 4 day LSSGB Instructor-Led Online Class Training • 2 Full Length LSSGB Practice Tests • Certified LSSGB Exam Fee included • 100% money back guarantee • Real life case studies and Examples • 32 contact hours certification • Become a Lean Six Sigma Green Belt Certified with this training • 12 Hours Prerequisite Training Our other certifications: CAPM | PMP | LSSBB | LSSGB | PMI ACP | CBAP Enroll Now!
https://www.icertglobal.com/course/Lean-Six-Sigma-Green-Belt-Certification-Training-Jacksonville-FL/Classroom/106/199 You may also Call us on +1-713-287-1187 or +1-713-287-1214 for more details.
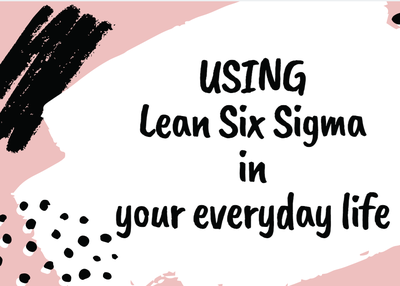
What is Six Sigma?
Six Sigma is a quality improvement process used by many Corporations and Organizations worldwide. There are several benefits for using this methodology for any business large or small. These same valuable tools and methods are ways to use Six Sigma in your daily life. Be it the start of a new year or right now, you can take up the resolution to implement Six Sigma in your daily life.
Your Plan
As a new year begins, resolutions and renewed energy drives us to improve our quality of life, personally and professionally. This is a great time to incorporate the DMAIC methodology to attain any type of goal you set. So many times we make plans to improve our daily life but the factors to achieve success have not been properly laid out.
What is it you want to accomplish; today, this month, this year? Whether it be short term or long term, your plan needs to be clearly defined with what you want to change then identify the factors.
Your Strategy
Maybe this is the year you want to buy a house. A down payment is your long term goal. Here is where using Six Sigma in your daily life will come into play. Defining your plan should clearly state how you want to save money. Determining where and how you spend your money is the Measurement phase of the process. A planned and thought out budget, listing income, expenses, wants and needs will help you see where changes can be made. Easier said than done, you have set this goal before and you still wonder where your money is going? Here is where the Analyzing step comes into play. Identifying the problem and the cause of your spending. To minimize the risk of using your savings for unplanned medical bills or car repairs, planning ahead and preparing for these surprise expenses by listing ways to aid in your savings goal. Once you have your new plan in place Improving and implementing your solutions are the key factors in accomplishing your goal. Coupons and carpooling, bringing your coffee and lunch to work are approaches to use in your savings process.
Your Accomplishment
Now that you have a solution, stay accountable and in Control. Updating and maintaining your new budget will keep you on track to attaining your savings goal and your new home. Now you can clearly see the process and how easily it can be applied, you are able to integrate the Six Sigma methods in your work, volunteer organizations and your household.
When you begin using Six Sigma in your daily life, soon enough you will integrate these tools in your daily routines, not just for an improvement process in a corporate management project.
For KPMG Lean Six Sigma Training registrations mail to
[email protected] or call at +91 9555688555 or +91 9022033666.
Lean Six Sigma Black Belt Training Programme
Lean Six Sigma Green Belt Training Programme
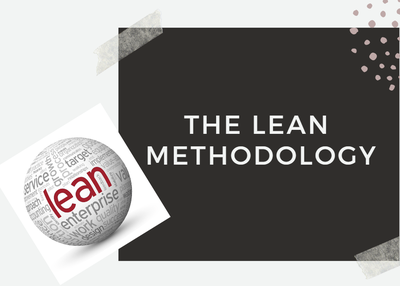
The Lean methodology is gaining a reputation for its capacity to assist companies to obtain their goals in a more fit, smarter, more sustainable manner. Lean allows companies to optimize throughout the cost movement for price delivery, improving speed, excellence, and organizational fitness. Lean originated with the Toyota Production System, which revolutionized the manufacture of bodily goods within the 1950s, ‘60s, and past. Lean keeps its hold in production but has additionally determined new programs in understanding work, assisting organizations to eliminate waste, enhance techniques, and raise innovation.
Of course, the nature of knowledge work differs substantially from that of producing: specifically, the value being created in information work is inside the minds of people, no longer at the meeting line. This affords a unique set of challenges and opportunities when making use of Lean to expertise work. Agencies from all disciplines of understanding work discover the first-rate achievement with lean, using it to propel them into greater efficiency.
To understand how lean is carried out to understanding work, it’s beneficial to recognize the history of lean manufacturing.
A brief history of lean:
Within the '80s and ‘90s, western manufacturers struggled to keep up with the greater efficient eastern groups, in order that they had options: trim down or shut down. They commenced adopting the practices of eastern organizations to enhance their speed, productiveness, and cost efficiency to stay competitive.
During this time, lean changed into boiled right down to overly simplistic ideas, normally used to justify relentless fee cutting. Nowadays, the manufacturing enterprise employs some distance fewer human beings than it once did. There are also fewer gamers in this area; they’re leaner but large.
Many versions of lean methodology were born inside the years following, which include Total Quality Management, Just-in-time, Six Sigma, and the idea of constraints. Each of these moves included numerous practices from what the Japanese had been doing that differentiated them from their competition, even though we will properly say that what they have been aiming for is now called lean. A lot of these famous “lean” management frameworks were tremendously prescriptive by using nature and required enormous education to adopt absolutely.
Today, businesses are looking to transform the way they work with the aid of making use of Lean Standards, especially: continuous development and respect for people.
Lean solutions empower groups to deliver faster by way of visualizing value streams, optimizing the go with the flow of labour and constantly improving their overall performance. Lean delivery gives the following advantages:
● Optimizing float by way of visualizing cost streams and reducing dependencies.
● Fueling non-stop development via studying overall performance, identifying traits, and evolving techniques.
● Leveraging lean principles to empower teams to innovate, adapt, and deliver value quicker.
● Handing over large, extra complex results by way of coordinating workstreams throughout groups.
● Scaling to the portfolio level to stability timing, staffing, and price for delivery of corporation-stage projects.
● Driving strategic tasks with road mapping and iterative funding of cost streams.
For KPMG Lean Six Sigma Training registrations mail to
[email protected] or call at +91 9555688555 or +91 9022033666.
Lean Six Sigma Black Belt Training Programme
Lean Six Sigma Green Belt Training Programme
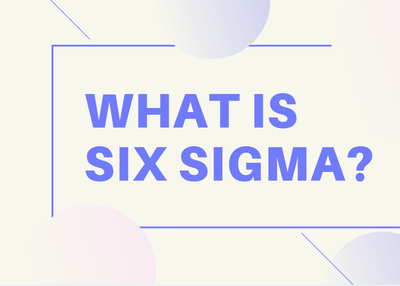
Six Sigma originates from a 19th Century numerical hypothesis, however discovered its way into the present standard business world through the endeavors of an engineer at Motorola during the 1980s. Presently proclaimed as one of the chief methodological practices for improving consumer satisfaction and improving business forms, Six Sigma has been refined and idealized throughout the years into what we see today.
Regardless of the defining, the objective continues as before: Six Sigma looks to improve business forms by expelling the reasons for mistakes that lead to deserts in an item or administration. It achieves this by setting up an administration framework that efficiently recognizes mistakes and gives techniques to killing them.
The individuals who learn Six Sigma practices accomplish assignments at each dimension of achievement, including Green Belt, Black Belt, Master Black Belt and Champion.
The Beginnings of Six Sigma:
The procedure that prompted Six Sigma was started in the Nineteenth Century with the bell curve created by Carl Fredrick Grauss. During the 1920s, analyst Carl Shewhart, an establishing individual from the Foundation of Scientific Insights, demonstrated that a procedure required amendment after it had veered off three sigmas from the mean.
Push ahead to the 1970s, when Motorola senior official Art Sundry grumbled about the absence of predictable quality in the organization's items, as per the 2006 book "Six Sigma" by Richard Schroeder and Harry Mikel.
As indicated by the acknowledged story from various sources, Motorola specialist Bill Smith in the end addressed the call to reliably fabricate quality items by working out the strategies of Six Sigma in 1986. The framework is impacted by, yet unique in relation to, other administration improvement methodologies of the time, including All out Quality Administration and Zero Imperfections.
Some of the Major Aspects of Six Sigma:
With an end goal to carry tasks to a "six sigma" level – basically, 3.4 imperfections for each one million chances – the technique calls for constant endeavours to come to the heart of the matter where they produce steady and unsurprising outcomes.
Deconstructing the assembling procedure down to its basic parts, Six Sigma characterizes and assesses each progression of a procedure, looking for approaches to improve efficiencies in a business structure, improve the nature of the procedure and increment the main concern benefit.
Toward that end, the procedure requires the preparation of workforce in Six Sigma, including learner Green Belts, Black Belts who frequently head up individual projects, and Master Black Belts who search for approaches to apply Six Sigma over a business structure to make upgrades.
A definitive objective is to improve each procedure to a "six sigma" level or better. Does it work? Motorola detailed in 2006 that the organization had spared $17 billion utilizing Six Sigma.
Methodologies of Six Sigma:
There are two noteworthy philosophies utilized inside Six Sigma, the two of which are made out of five segments, as per the 2005 book "JURAN Foundation Six Sigma Breakthrough and Beyond" by Joseph A. De Feo and William Barnard.
DMAIC: This strategy is utilized basically for improving existing business forms. The letters represent:
Characterize the issue and the undertaking objectives
Measure in detail the different parts of the present procedure
Break down information to, in addition to other things, discover the root surrenders in a procedure
Improve the procedure
Control how the procedure is done later on.
DMADV: This technique is commonly used to make new procedures and new items or administrations. The letters represent:
Characterize the undertaking objectives
Measure basic parts of the procedure and the item abilities
Break down the information and create different plans for the procedure, in the end picking the best one
Plan and test subtleties of the procedure
Confirm the plan by running reenactments and a test case program, and afterward giving over the procedure to the customer
There are additionally various administration devices utilized inside Six Sigma. While there are beyond any reasonable amount to list, here are subtleties on a couple of them.
Five Whys – This is a strategy that utilizations inquiries to get to the main driver of an issue. The strategy is basic: essentially express the last issue (the vehicle wouldn't begin, I was late to work again today) and afterward pose the inquiry "why," stalling the issue to its underlying driver. In these two cases, it may be: on the grounds that I didn't keep up the vehicle appropriately and in light of the fact that I have to go out prior to get the opportunity to take a shot at time. The procedure previously came to noticeable quality at Toyota.
CTQ Tree – The Basic to Quality Tree chart separates the parts of a procedure that delivers the highlights required in your item and administration in the event that you wish to have fulfilled clients.
Main driver Investigation – Much like the Five Whys, this is a procedure by which a business endeavors to recognize the underlying driver of an imperfection and after that right it, as opposed to just adjusting the surface "manifestation" of the issue.
At last, the majority of the devices and procedures in Six Sigma fill one need: to streamline business forms so as to deliver the most ideal items and administrations with the littlest measure of deformities. Its appropriation by enterprises far and wide is both a marker of and demonstration of its wonderful achievement in the present business condition.
For KPMG Lean Six Sigma Training registrations mail to
[email protected] or call at +91 9555688555 or +91 9022033666.
Lean Six Sigma Black Belt Training Programme
Lean Six Sigma Green Belt Training Programme

Value Stream Mapping in Lean Six Sigma offers information flow that can be determined on the basis of value-added or non-value-added actions.
It will help you make your work process more efficient by saving time and will also help you in increasing productivity.Please Like, Share & Subscribe for more Videos.Visit: https://elearning.mindcypress.com/courses/lean-six-sigma-green-belt/Read: https://blog.mindcypress.com/p/what-is-value-stream-mapping-in-lean-six-sigmaFacebook: https://www.facebook.com/MindCypressInstagram: https://www.instagram.com/mindcypress/LinkedIn: https://www.linkedin.com/company/mindcypressTwitter: https://twitter.com/mindcypress
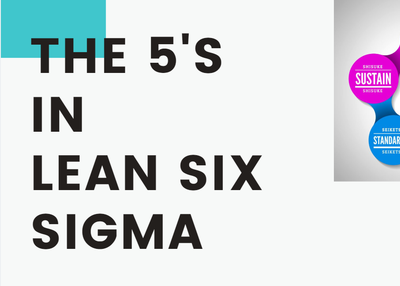
5S was initially a Japanese association strategy made out of the terms: seiri, seiton, seiso, seiketsu, and shitsuke. This philosophy was a structure square to permit Just-in-time Manufacturing.
Extra “S’s” are likewise being used that incorporates SAFETY. Safety is dependably an essential for any undertaking or occasion and ought to be assessed at each stage. All the more as of late there has additionally been an “S” for Client “Satisfactiom” and “Security”
The naming shows areas not as significant as making each stride all together and finishing each before proceeding onward the following.
The accomplishment of 5S is because of its effortlessness, simplicity of seeing, snappy effect, and general applications. It tends to be connected underway zones, office territories, and data frameworks.
Clutter can be irritating or at its outrageous even hindering to a home or workspace. Clutter happens when you wouldn’t dare hoping anymore; precedent, you spare a magazine with the goal that you can peruse it later. At that point before you know it, you have a whole lifetime of National Geographic magazines put away in your storage room! Lean’s 5S instrument is an incredible method to dispose of what you needn’t bother with.
Here’s the 5S device in real life:
Seiri (Sort): Separate garments into heaps. Separate by the required, the additional or copies, and unneeded. Do this for shoes also. To make sense of what you truly needn’t bother with, you could utilize the 5 Whys device. Simply continue asking “why” you would need said thing and if toward the end the reason isn’t sufficient, simply offer it to philanthropy.
Seiton (Straighten): Conveniently mastermind what you need, from the “required” heap. Arrange the garments and shoes in a manner where what you utilize all the more every now and again is anything but difficult to get to. Ensure you compose your things in a manner that everything is unmistakable.
Seiso (Shine): Before you really put the garments and shoes back in the storage room, ensure you clean, vacuum, and residue every one of the spaces in the wardrobe.
Seiketsu (Standardize): On the off chance that you share your storeroom space with your loved one or individuals from your family, at that point ensure they pursue the tidy up after yourself preclude after they take a thing. In the event that you don’t share the storage room space with anybody, at that point you should dependably put things away, and in the event that you purchase a thing you should dispose of a thing so you don’t create clutter once more.
Shitsuke (Sustain): Analyze the outcomes. Maybe take an after image of your recently sorted out wardrobe and relish in your prosperity. Utilize the kaizen approach and continue fixing seemingly insignificant details in your remarkably up. Try not to give them a chance to amass.
For KPMG Lean Six Sigma Training registrations mail to [email protected] or call at +91 9555688555 or +91 9022033666.
Lean Six Sigma Black Belt Training Programme
Lean Six Sigma Green Belt Training Programme
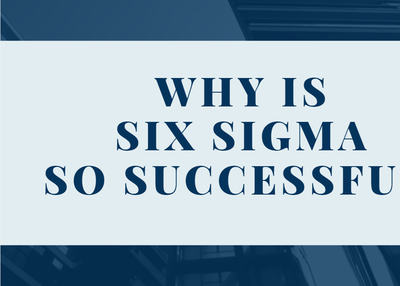
The logical tools and methods no doubt contribute a great deal towards the achievement of Six Sigma improvement ventures, yet they just can’t be taken as the sole elements in charge of Six Sigma’s viability since they just compliment the inborn rationale underlining Six Sigma and in that capacity are close to an unfortunate obligation.
So what truly makes Six Sigma so viable? All things considered, for that, you just need to investigate the most normally used Six Sigma quality improvement technique, for example, DMAIC that represents Define, Measure, Analyze, Improve and Control.
Pay special mind to similitudes between standard strategic approaches and the DMAIC stages expressed over, some of which are depicted beneath:
The Define Phase
The Define stage is very like the standard business routine with regards to recognizing basic issues of a given business process with the expectation to devise successful answers for beating the given issues and issues. It can without much of a stretch be contrasted with a business visionary’s exertion with improving the conveyance frameworks of his business by leading a survey of all the different major and minor parts of the general conveyance framework.
The Measure Phase
On the off chance that we think about the above model, the Measure stage will appear to be the same as the business visionary’s push to evaluate the negative effect that the distinguished issues can conceivably have on his general business. This is very fundamental for the business visionary since it is at exactly that point will he have the option to focus his endeavours on conquering issues that hold the most potential for harm.
The Analyze Phase
The Analyze stage is very like the business person’s push to make a rundown of all the accessible options and test every one of them exclusively to realize which elective will work best for getting the ideal outcomes.
Much the same as the business visionary would like, the Analyze stage also calls for choosing just those choices for definite execution, which hold the most potential and are financially savvy.
The Improve Phase
This stage is the same as the business person’s push to guarantee that the activities chose for improvement are executed in an endorsed way. Much the same as the business person would like, the Improve stage also stresses finishing ventures inside the stipulated time and expenses.
The Control Phase
Similarly, as the business person might want to check the viability of the improvement extends, the Control stage also stresses surveying whether the improvement activities are executing according to desires. Taking medicinal measures if there is a befuddle is inborn to the Control stage, similarly as a business person might want to do.
For KPMG Lean Six Sigma Training registrations mail to [email protected] or call at +91 9555688555 or +91 9022033666.
Lean Six Sigma Black Belt Training Programme
Lean Six Sigma Green Belt Training Programme
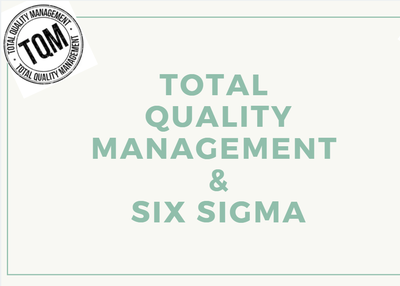
The causes of Total Quality Management (TQM) had numerous progenitors in its initiation, yet was nonexclusive in nature. Which means you could plug crafted by Ishikawa, Juran and Deming (just to give some examples) into any business and you’d get results — just not the best outcomes for your particular business.
Six Sigma has a few contracts from TQM — it puts a significantly more grounded spotlight on client prerequisites; all things considered, organizations are there to serve their clients. Along these lines, Voice of the Client (VOC) is critical in the nature of their item or administration.
Six Sigma likewise requires extra tools utilized in information examination. The budgetary spotlight is on a venture level — with TQM, it is on an authoritative dimension.
The unmistakable comprehension is that Six Sigma’s strategies have an outlook of having a triumph rate of 99.9997% or under 3.4 deformities per million chances. With these high objectives, particularity is an unquestionable requirement.
So as to accomplish this dimension of magnificence, a Six Sigma culture must exist all through the business or association. General Electric has had such an enormous accomplishment with Six Sigma that in the event that you go to their site you’ll see that they are Six Sigma’s greatest backer.
In days gone by, it was trusted that if a business yielded to their client that it would cost that business an excessive amount of cash. Truth be told, the inverse is valid.
Here’s a decent similarity: getting a garden of delightfully planted turf, however you needed to scene your new yard with wonderful shakes and water productive foliage. In spite of the fact that the turf looks incredible, it was not what you needed and it is a major dissatisfaction — to both the client and the business. The client feels unheard and the business feels overlooked for delivering an extraordinary item. It’s not extraordinary in the event that it isn’t what the client required. This can at last lead to lost clients as time goes on.
For KPMG Lean Six Sigma Training registrations mail to [email protected] or call at +91 9555688555 or +91 9022033666.
Lean Six Sigma Black Belt Training Programme
Lean Six Sigma Green Belt Training Programme