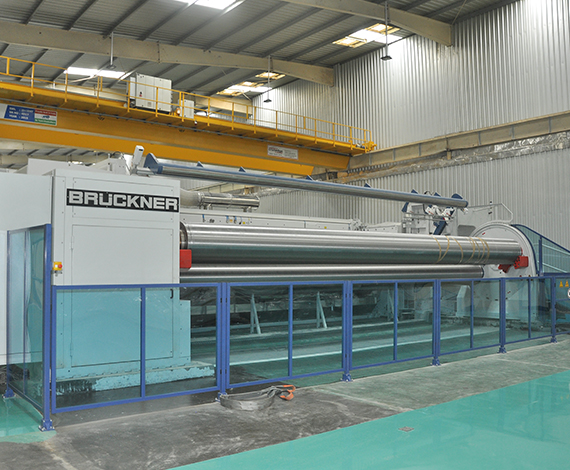
The in-mold label is now the most common, fast, and cost-effective way to manufacture labeled containers. Technological advancements make the manufacturing process cost less to increase its demand. The other primary reason is that it is waterproof and resistant to wear and tear.
The rapid rise in the food packaging industry, in-mold label global market share, is to reach 8.78 billion USD from 5.56 in 2018 with CAGR at 5.9%. The increasing awareness of the consumers about the need for attractive and informative labeling is also helping its use and growth worldwide.
In-mold provides a no-label look
The in-mold labels provide the no-label look on the products on any container shapes. Since it removes many production bottlenecks, post model labeling, and even larger manufacturing space, it is now becoming the favorite of the flexible packaging sector. PP or Polypropylene is the raw material that manufacturers use to make in-mold labels. It is because of it being an extremely versatile plastic material.
Three methods In-mold label manufacturing process
In-mold manufacturers place a pre-printed PP label on the mold of the packaging to start its manufacturing process. The mold gives shape to the plastic packaging and adds the label to the packaging, and after curing time, both the packaging and labeling become a single piece. There are three methods for this in-mold label manufacturing process including:
Injection molding
Butter and ice cream cups are the best examples of injection molding and in-molding labels. It is the standard form of injecting heated or liquefied plastics or polymers to mold and made to cool to give the shape for the container. Some excellent manufacturers use computers to use this manufacturing technology.
Blow molding
Blow molding makes hollow plastic parts wherein the manufacturers extrude a heated plastic mass to take the shape of a mold.
Thermoforming
During thermoforming, the pre-printed labels accompany the heated plastic sheets stamped into a mold to bind them both to one piece.
Benefits of in-mold labels
With its many unique features, in-mold labels have many benefits that include:
- With it stretching correctly on the container as one piece there are no glue resides, wrinkles or blisters
- As it is recyclable, it is environment friendly
- Delivers manufacturing efficiencies and economies without the need to sacrifice the aesthetics of product packaging
- Since it is impossible to remove them from the product, it ensures its security
- Due to being hygienic, resistant to moisture and temperature the are best for frozen products
- Makes the product to stand apart from the crowd to attract the customers
- Ensures high-resolution images due to the offset printing techniques
- Helps to decorate all sides of the container with one single label
- Automation of its manufacturing provides quick design changeovers, a wide range of look and feel options
Jindal Poly is one of the best in-mold label manufacturers in India and worldwide, providing many of the above benefits. They also offer the best quality with minimal production time and with a wide range of customized options.