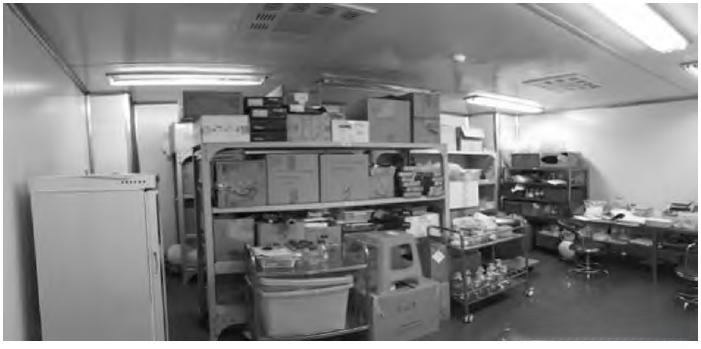
The main function of the clean room is to continuously provide a clean environment that meets expectations, and the cleanliness is the core technical indicator for evaluating the clean room level. From the perspective of clean room engineering construction, the factors affecting cleanliness include architectural design and construction quality; From the perspective of clean room management and operation, including personnel, materials and dynamic process control. When the cleanliness is evaluated statically, the categories of each element appear to be independent, but when the dynamic cleanliness performance is abnormal, the butterfly effect can appear among the influencing factors. This study puts forward a control idea based on the influence factors of the defect on the cleanliness of the example.
The clean room is also called the dust-free workshop. Its function is to ensure that the exogenous pollution particles in the outdoor environment will not affect the cleanliness of the clean room environment, ensure that the endogenous pollution particles generated in the clean room environment can be diluted and filtered out, and continually maintains the dust-free status of controlled environments. With the innovation and development of research and development of sterile hygiene products, the demand for the use of clean environments is becoming more and more extensive; At the same time, with the innovation and development of precision electronic technology, the application requirements for clean environments are becoming more and more lean. For example, the particle load in the production process of medicines, medical devices and other products will cause adverse reactions or infection of the affected people, and the dust contamination of precision instruments, electronic chips and other products in the production process will lead to abnormal wear or product scrapping.
Cleanliness level
The evaluation of the cleanliness of the clean room is based on the control level of suspended particles in the indoor environment. The higher the cleanliness level, the smaller the particle size of the controlled suspended particles and the lower the controlled particle concentration threshold. Cleanrooms for aseptic and hygienic products focus on the control of microorganisms in the environment, also known as biological cleanrooms. The control of suspended particles ≥ 5.0 μm can indirectly control the microbial level in the clean room, so the cleanliness of the biological clean room is usually controlled at level 5 or below. Clean rooms for precision machining and integrated electronic products are mainly used to control suspended particles in the environment, also known as industrial clean rooms. With the technological innovation of nano-manufacturing process, the demand for cleanliness in industrial clean rooms has reached level 1 and above.
According to the risk assessment of the impact of suspended particles in the production environment on the product, or the cleanliness level of the controlled environment specified in the relevant regulations, For example, the "Guidelines for On-site Inspection of Sterile Medical Devices in the Good Manufacturing Practice for Medical Devices" stipulates that "sterile medical devices (including medical materials) processed by aseptic techniques shall be localized under 10,000 grades (level 7). Production is carried out in a class 100 (class 5) clean room. The particle control requirements of the air cleanliness level are shown in Table 1, and the derivation formula is shown in the picture.
Among them, Cn is the maximum allowable concentration of particles (pieces/m3); N is the number of the cleanliness level; D is the particle size of concern (μm).
Factor analysis
2.1 Interior design
The construction and decoration principle of the clean room is to use materials that do not produce dust, the surface is smooth and easy to clean, and the gaps are closed and dust-free. The door of the clean room should not have a threshold, and unnecessary concave and convex surfaces will make the cleaning work of the clean room less effective [2-3]. The threshold in Fig. 1 a is close to the ground, and the settled large particles of dust are easy to deposit on the threshold, and are entrained and diffused with the flow of people; The light hood in Figure 1 b is located at a high position in the space, and the suspended small particles of dust are easy to deposit on the cover surface, and are touched and diffused by the turbulent flow generated by the air supply port. Dust that is difficult to detect and remove is a potential source of danger that affects cleanliness.
2.2 Filter integrity
The core technology to ensure that the clean room is not affected by dust particles is the air purification and filtration function in the ventilation system. The air filter is the core equipment for creating a clean environment. The coarse-effect filter can filter out particles above 10 μm, the medium-effect filter can filter out particles between 1 and 10 μm, and the high-efficiency filter can filter out particles ≥ 0.3 μm[ 4]. As the last barrier in the clean room, the high-efficiency filter installed at the end of the ventilation duct can be regarded as the core technology, the integrity of its installation determines the cleanliness of the clean room. According to the aerosol photometer test, not only the air supply surface transmittance of the filter is required to be ≤ 0.01%, but also the evaluation standard for the airtightness of the installation frame should be ≤ 0.01% [5]. This requirement indicates that the unfiltered part of the airflow in the air supply duct should not enter the clean room, and the airflow must be effectively filtered before entering the clean room. At multiple ends in the non-unidirectional flow clean room, the integrity of the high-efficiency filter should be 100% confirmed, and the leakage of any filter may affect the cleanliness of the clean room.
a. door frame with threshold b. pendant light with shade
2.3 Airtightness of the building structure
The clean room is a closed space formed by splicing panels, and the splicing gap between material units will have an important impact on the cleanliness of the clean room. Good airtightness can protect the clean room from the infiltration and pollution of suspended particles in the outdoor atmosphere during shutdown. Suspended particles of 0.1 ~ 1.0 μm in the environment have a typical Brownian motion [6], and Brownian motion will cause the macroscopic diffusion of suspended particles from a high-density environment to a low-density environment [7].
The door in Figure 2a is not equipped with a sealing strip and has no airtightness. The sealing strip on the door in Figure 2b is in an invalid state of sealing. When the ventilation system is shut down, the suspended particles in the outdoor atmosphere will penetrate into the clean room through the gaps. The diffusion effect of the particles is positively related to the cross section of the gaps. The particles attached or deposited in the clean room will destroy the cleanliness of the clean room.
a. Seal not installed b. ineffective seal
2.4 Protection of personnel
Personnel come and go frequently in the clean room and have a large amount of activity. The metabolism of the human body will secrete pollutants, and the clothing will also release pollutants. Therefore, personnel are the main source of pollution in the clean room. The best measure for controlling personnel to reduce particle pollution in a clean room is to wear clean clothes, which wrap the body surface and daily clothing. Purification of human pollution sources. Due to the greater impact of personnel on the clean room, the role of clean clothes is particularly important. Clean clothes with good performance should ensure that the material does not produce dust, and has good dust resistance, antistatic properties, and wear resistance [9]. The amount of dust generated by personnel is related to the action of the operation, the material of the clean clothes, and the form of the clean clothes. The amount of dust generated is shown in Table 2 [10].
2.5 Material selection
2.5.1 Selection of sanitary ware
When there is no special requirement, the materials entering the clean room should at least comply with the basic principle of no dust production. Figure 3 shows the cloths commonly used for sanitary ware in clean rooms. When improperly selected, sanitary ware items may become a source of pollution in the clean room; a is a special fabric for clean rooms, the fiber structure is tight and orderly, and its good capillary effect can realize the transfer of dirt, and the dirt retained in the fiber gap is not easy to be settled and transferred [11], so the application of this material can ensure the cleanliness of the cleaning surface; b is an ordinary cloth with loose fiber structure and poor toughness, and it is easy to break due to rubbing, and fiber residues are easy to occur on the cleansing surface after wiping.
a. Clean cloth b. Normal cloth
2.5.2 Selection of paper
Three types of paper that are common in clean rooms were selected for evaluation, using the airflow organization characteristics of the vertical unidirectional flow environment, in the dust-free experimental condition, the sample was shaken by stretching to collect the particles emitted from the 100 cm2 sample per minute. The results are shown in Table 3, and the experimental schematic diagram is shown in Figure 4. Toilet paper has the loosest fiber structure and produces the most dust; weighing paper has the tightest fiber structure and produces the least dust. When materials with high dust generation cannot be avoided in the clean room, the necessary conditions for their use should be limited to reduce the impact on cleanliness.
2.6 Airflow organization in a clean room
The clean air flow conveyed in the clean room can dilute the generated suspended particles, so as to realize the control of cleanliness. The ideal airflow organization should fill all the spaces in the clean room, and the evaluation index is the self-cleaning time of the clean room. The use of the clean room will directly affect the organizational form of the indoor air supply airflow. As shown in Figure 5, the stacking of items in the clean room is high and the storage volume is large. The layout of the shelves has seriously affected the diffusion of clean air in the room, and the storage of logistics turnover boxes has the potential risk of releasing a large amount of dust. The clean room is in a state suitable for dust production and not suitable for self-cleaning. The above analysis results are the main reasons for the unqualified cleanliness of the clean room.
2.7 Process control
2.7.1 Dynamic differential pressure
The specification requires that the static pressure difference between adjacent clean rooms of different levels should be ≥ 5 Pa, and the static pressure difference between the clean room and the outside should be ≥ 10 Pa [12]. During the production process, due to the dust or odor generated during the mixing or configuration process, local exhaust ventilation is required to limit the spread of pollutants in the clean room.
The dynamic partial exhaust air intervention will change the static balance of the air supply and return air volume in the clean room, and disrupt the static pressure difference. In extreme cases, the positive pressure clean room can be turned into a negative pressure state, and the negative pressure air flow will cause the outdoor air carrying suspended particles to penetrate into the clean room through structural gaps, reducing the cleanliness of the clean room.
2.7.2 Management O&M
Cleaning is a necessary maintenance behavior to maintain the cleanliness of the clean room, and immediate cleaning can avoid secondary pollution of settled particles. The hygienic status in Figure 6 reflects that there are obvious defects in the management of the clean room, which may be due to insufficient cleaning program documentation or irregular cleaning work. Figure 6 a shows the top of the locker in the second locker room. The dust accumulation is obvious, indicating that it has not been wiped clean for a long time; Figure 6 b shows the foot of the sink in the washroom. The obvious discoloration of water stains indicates that it has not been cleaned and disinfected for a long time. The higher or lower areas in the clean room are very easy to form a hygienic dead corner due to out-of-control blind areas, which becomes a safety hazard in the clean room.
Conclusion
The dynamic cleanliness of a clean room is determined by the cross-linking of independent elements in the static state. The static cleanliness can only show that the controlled environment basically meets the clean conditions, while the dynamic cleanliness plays a decisive role in controlling the risks of activities in the clean room. The control of personnel, materials and processes has a critical and complex impact on the dynamic cleanliness. The fluctuation of any element will affect the dynamic cleanliness, and the regulation and optimization of elements will play a positive and beneficial role in controlling the cleanliness.