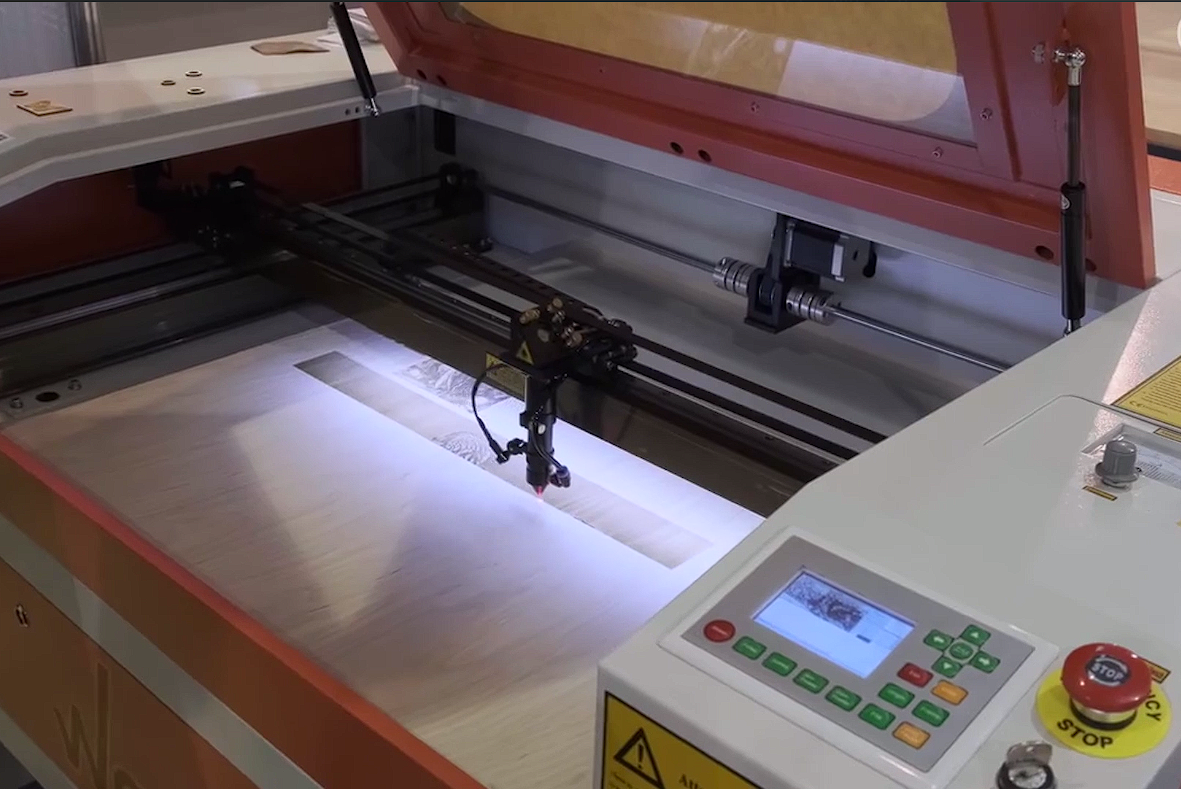
Ceramics have a rich history and are used in a variety of industries including art, construction and electronics. Recently, there has been an increasing interest in laser cutting ceramics.
The purpose of this guide is to provide a comprehensive overview of techniques and tips for laser cutting ceramics and to emphasize the unique features and challenges of cutting this material.
CONCEPT OF LASER CUTTING
Laser cutting is a precise and efficient technique that utilizes focused laser beams to cut a variety of materials. When it comes to ceramics, understanding the basics of laser cutting technology is crucial.
Both CO2 laser machines and fiber laser machines are used to cut ceramics. Each type of machine has certain advantages and limitations depending on the specific ceramic material and the desired result. Therefore, these factors must be carefully considered when selecting the right laser machine for cutting ceramics.
PREPARATION FOR LASER CUTTING
Before starting the laser cutting process, it is necessary to select the ideal ceramic material to be cut. Some ceramics may be more compatible with laser cutting due to their composition and structure.
In addition, the preparation of the ceramic surface is very important to achieve optimal cutting results. This may include cleaning the surface, removing contaminants and ensuring a smooth surface for accurate laser cutting. Safety precautions and protective measures must also be followed to protect the operator and the ceramic material during the cutting process.
LASER CUTTING METHODS
1. LASER ABLATION
Laser ablation is a technique widely used for cutting ceramics. It involves the removal of material from the surface of the ceramic using laser pulses. Laser ablation has several advantages such as high precision and minimal thermal damage to the surrounding area. However, it has limitations, including low processing speed and possible surface roughness. Understanding the applications and limitations of laser ablation is critical to successful ceramic cutting.
2. CO2 LASER CUTTING
CO2 laser cutting is another widely used method of cutting ceramics. This method uses a powerful CO2 laser beam that reacts with the ceramic material, causing it to vaporize and creating a clean and precise cut. CO2 laser cutting offers excellent versatility, faster cutting speeds, and minimal post-cut machining compared to other laser cutting methods. However, to achieve optimal cutting results, the response of the ceramic material to a particular CO2 laser wavelength must be considered.
3. FIBER LASER CUTTING
Fiber lasers have gained popularity in ceramic cutting due to their high beam quality and energy efficiency. These lasers generate an intense laser beam ideal for precision cutting of ceramic materials. However, cutting with a fiber laser can be challenging, such as possible thermal damage and limitations on cutting thick ceramics. Implementing methods to improve the precision of fiber laser cutting, as well as understanding the advantages and challenges of this method, is critical for successful ceramic cutting.
DESIGN CONSIDERATIONS
Design plays a crucial role in the successful laser cutting of ceramic materials. To ensure that ceramic products are suitable for laser cutting and achieve the desired result, basic design principles must be considered.
Optimizing the design of complex ceramic products is necessary to exploit the precision capabilities of laser cutting. In addition, incorporating aesthetic and functional elements into laser-cut ceramics allows for the creation of truly amazing and unique products.
FINE TUNING OF LASER CUTTING
1. PARAMETERS AND SETTINGS
Understanding and fine tuning laser cutting parameters is very important to achieve the best results when machining ceramics. Various factors such as laser power, cutting speed and frequency can significantly affect the quality and efficiency of the cut. Experimenting and finding the optimal cutting conditions for different ceramic materials can improve the efficiency of the entire cutting process.
2. KERF WIDTH COMPENSATION
The kerf width, i.e. the amount of material removed during the laser cutting process, can affect the precision and accuracy of ceramic designs. The use of kerf compensation techniques can help to achieve the required accuracy and ensure that the final ceramic product matches the intended design. By accounting for kerf widths, laser cutting can produce intricate details without compromising the overall design.
3. DESIGN AND ASSEMBLY OF THE STRUCTURE
Developing appropriate joints in the design is critical to creating seamless and durable ceramic structures. Laser-cut ceramic pieces often require assembly to create larger structures or functional objects. Understanding the various connection options in a design and utilizing appropriate assembly techniques can ensure that high quality and visually appealing ceramic designs are produced while maintaining integrity.
POST-CUTTING PROCESSES
After the laser cutting of ceramics, several operations can be carried out to improve the aesthetic and functional characteristics of the ceramic. Finishing and surface treatments, such as polishing or glazing, increase the visual appeal of the ceramic product.
In addition, these treatments protect the ceramic material from external factors and increase its durability. Removing residual stresses and optimizing mechanical properties through special post-cutting treatments also contribute to improving the quality of the final ceramic product.
LASER CUTTING TROUBLESHOOTING
Although laser cutting is a precise technology, difficulties and problems can arise. Identifying typical problems such as chips, cracks or incomplete cuts is the first step in troubleshooting laser cutting flaws and defects.
Methods to solve these problems, such as adjusting the laser parameters or fine-tuning the cutting approach, will help to achieve the desired cutting results and minimize the loss of ceramic material.
SAFETY AND MAINTENANCE
Ensuring safety during laser cutting of ceramics is of paramount importance. Both the operator and the equipment must be protected throughout the process. Utilizing safety measures, such as using appropriate safety gear and having safety protocols in place, reduces potential risks. Regular maintenance and cleaning of laser cutting machines is also critical to ensure optimal performance and longevity.
FUTURE TRENDS AND INNOVATIONS
The field of laser cutting ceramics is constantly evolving. Emerging technologies and advances such as more powerful lasers and more precise control systems are revolutionizing the industry. Exploring future applications and opportunities in this field offers exciting opportunities for ceramic manufacturers to push boundaries and create unique products.
CONCLUSIONS:
Laser cutting has proven to be an indispensable tool in the fabrication of ceramic products. Mastering the techniques and tips outlined in this guide is essential for ceramic manufacturers to fully utilize the potential of laser cutting and create exceptional ceramic products. By understanding the intricacies of laser cutting and taking into account the specific requirements of ceramics, remarkable results can be achieved.