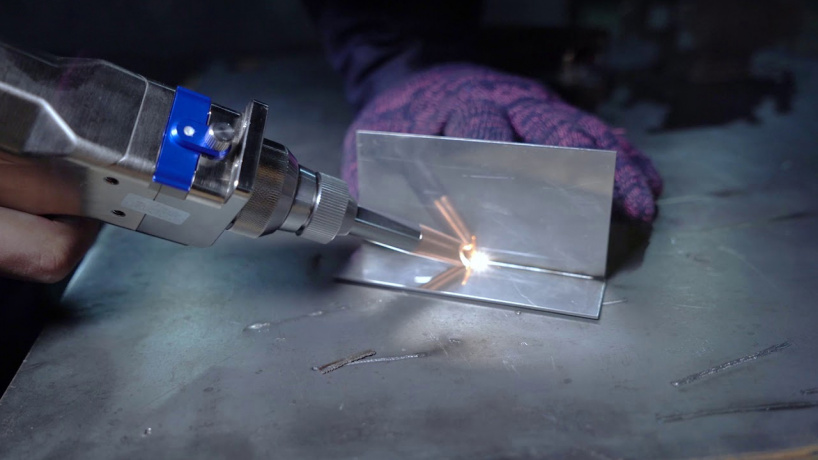
Laser welding is a method of joining metals or thermoplastics using a laser beam to create a weld. Due to the highly concentrated heat source, laser welding of thin materials can be done at high speeds of up to several meters per minute, and in thicker materials narrow and deep welds can be created between parts with rectangular edges.
is a device for processing materials with a laser.
CLASSIFICATION BY TYPE OF LASER SOURCE:
- Fiber laser welders
Fiber laser welders are ideal for processing metal parts, providing high welding accuracy of about 25%.
- CO2 laser welders
CO2 laser welders create a continuous welding beam, providing efficient and strong welds capable of penetrating a variety of materials.
How to choose a laser engraving machine for home
- Nd: YAG laser welders
Nd: YAG lasers are less energy efficient than fiber lasers, but they offer certain advantages, such as improved laser control that is not available with other types of laser sources.
Welding materials
Pressed steel
Laser welding machine can be used to weld various models of stamped steel such as S136, SKD-11, NAK80, 8407, 718, 738, H13, P20, W302, 2344 and others. The welding quality of these materials is good.
Carbon steel
Laser welding is good for carbon steel, but the quality of welding depends on the impurity content. When welding steels with different carbon content, the laser beam can be adjusted for optimum welding results.
Stainless steel
Laser welding of stainless steel provides high quality welded joints due to its high speed and small heat affected zone. Defects such as pores and inclusions are minimized.
Copper and copper alloys
In welding copper materials, incomplete penetration and undercutting are common problems. These problems require the use of strong heat sources, preheating, and measures to prevent warpage and thermal cracking. Porosity can also be a problem when welding copper alloys.
Polymer materials
Laser welding technology is used for a wide range of thermoplastics and thermoplastic elastomers. Popular materials for welding include polypropylene (PP), polystyrene (PS), polycarbonate (PC), acrylonitrile butadiene styrene (ABS), polyamides, polymethyl methacrylate (PMMA), polyoxymethylene (POM), polyethylene terephthalate (PET) and polybutene terephthalate (PBT).
However, engineering plastics such as polyphenylene sulfide (PPS) and liquid crystal polymers cannot be directly laser welded due to their special properties.
To enable efficient laser welding, carbon black is added to the underlying material to enhance its ability to absorb energy and meet the welding requirements.
Aluminum alloy welding
One of the main challenges in welding aluminum and its alloys is their high reflectivity.
Aluminum is highly conductive of heat and electricity, making it an excellent reflector of light due to its high density of free electrons.
Due to the very high reflectivity of the original surface - more than 90% - deep penetration welding requires less than 10% of the input energy, which requires high power to carry out the necessary processes. This can lead to the formation of shallow holes at the beginning of welding.
Welding of magnesium alloys
Magnesium alloys have 36% lower density than aluminum alloys, which makes them interesting due to their high specific strength.
Experiments using pulsed YAG lasers and continuous CO2 lasers were conducted to weld magnesium alloy. For optimal welding conditions of AZ31B-H244 alloy (Al content 3.27%, Zn 0.79%) with a thickness of 1.8 mm, the following parameters were selected: average power 0.8 kW, pulse duration 5 ms, pulse frequency 120 Hz, travel speed 300 mm/s and focal length 0.42 mm.
A high-quality weld seam is achieved with a continuous CO2 laser.
Low-alloy high-strength steel
Laser welding of low-alloy high-strength steel can produce a joint with mechanical characteristics close to the base material if the required welding parameters are met.
An example of low-alloy high-strength steel is HY-130 steel, which has high strength and crack resistance after quenching and tempering.
Conventional welding methods usually produce a combination of coarse grain, fine grain and original structure in the weld and heat affected zone.ethods usually produce a combination of coarse grain, fine grain and original structure in the weld and heat affected zone.
The characteristics of the weld are often inferior to those of the base metal, and the weld / HW structure is more sensitive to the appearance of cold cracks in the welding condition.